By Nick Badger, Frontier Agriculture
Modern sprayers are managed by advanced computer systems, equipped with precision tools and GPS technology to optimise applications and operated by highly skilled, qualified specialists. It’s a practice that has certainly seen advancements over the years.
However, the filling of sprayer tanks has remained a labour-intensive and time-consuming task. The method of physically adding product to such sophisticated machinery hasn’t been afforded the same technological developments.
That is until the emergence of closed transfer systems (CTS).
Adopted extensively overseas for some time, CTS equipment is becoming more established in UK agriculture. We can already see it is delivering tangible benefits, helping growers, manufacturers and sprayer operators improve on-farm safety, reduce reliance on small cans which use single-use plastics, eradicate risks of point source contamination and boost productivity.
Importantly, those investing in the technology look set to be ahead of potential future legislation surrounding the safe handling of nutrition and plant protection products too.
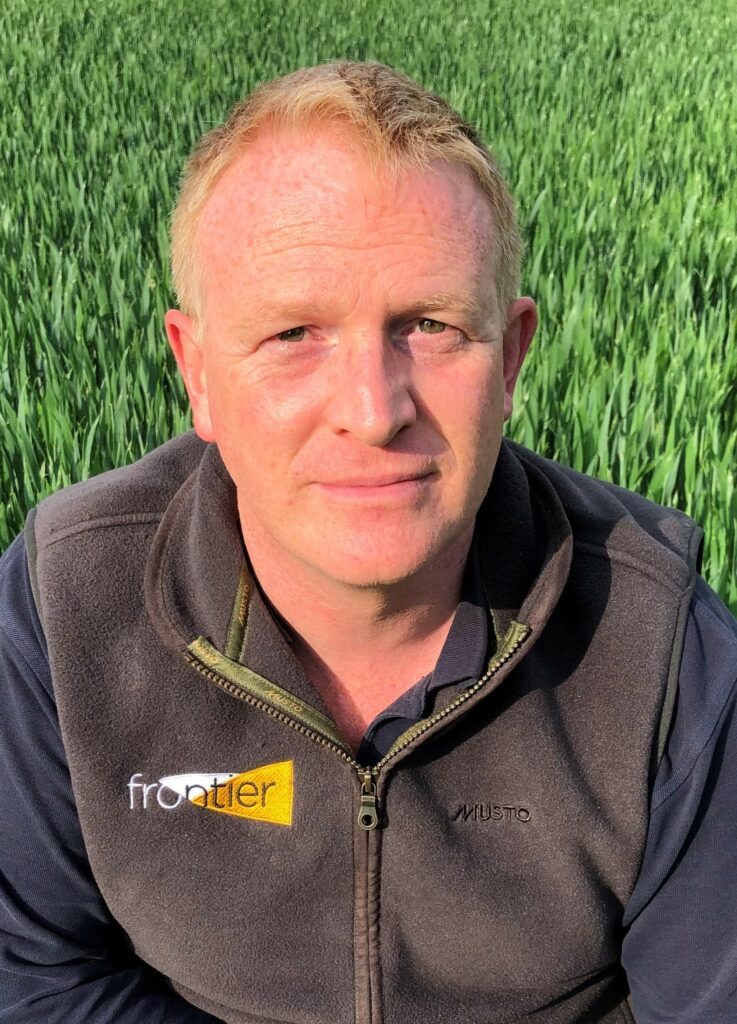
Reducing operator and environmental exposure
At Frontier, health and safety is our number one priority and, having seen the extensive benefits from CTS globally, we partnered with Richard Garnett of Wisdom Systems to help bring the technology to UK farms.
The Wisdom FasTran 850 closed transfer unit comprises a specialist container valve and coupler that ensures a clean, dry connection, and a flow meter that delivers +/- 0.5% accuracy and dispenses at 25 litres/min.
Designed for use with tamper-proof CTS-compatible IBCs, it ensures any product transferred to the sprayer is done so quickly, safely and efficiently, achieving a 95% reduction in operator and environmental exposure.
This is important when we consider the potential risks that concentrated crop chemicals can present to water courses and aquatic habitats.
Under the Water Framework Directive (WFD), water companies must continually assess upstream threats to water sources. Research by ADAS in 2003 showed that concentrated products entered water courses through farmyard drains during sprayer filling.
It’s therefore vital that our industry adopts new practices to ensure increasingly high levels of product stewardship and safer handling practices. While improvements have been made through the use of bunding and more secure premises, CTS equipment that meets recognised standards is helping to engineer controls that ensure concentrated products are safely contained until they are diluted and ready for use.
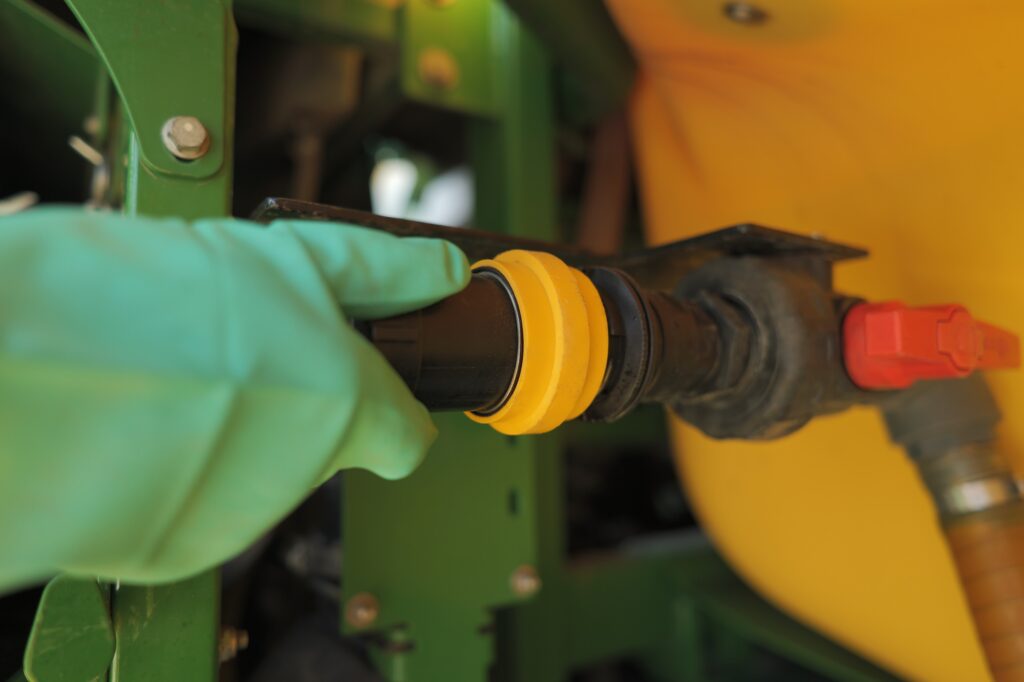
It’s therefore easy to see the value this equipment has on farm. Many water companies recognise this too, with some encouraging farms to use CTS through grant support in catchment areas.
Importantly, this improved stewardship could also help to safeguard the continued use of key crop protection and nutrition products, as well as support the introduction of new, innovative chemistry that’s vital for long-term food production.
Improved physical safety and operator welfare
The Health and Safety Executive (HSE) notes: “Health and safety is a fundamental requirement of a sustainable farming business,” but, unfortunately, agriculture has one of the worst injury rates and it costs the industry millions each year.
Thankfully, we’re seeing farmers experience improvements in this area following CTS adoption. As well as vastly reducing spills and exposure, the use of larger IBCs with a CTS means operators are no longer required to manually lift and manoeuvre multiple heavy cans, twist off tight caps or remove difficult seals. These activities, especially when done repeatedly, are a cause of significant injuries.
Less reliance on single-use plastics
The switch to larger IBCs brings benefits in terms of less packaging too, at a time when the industry is under growing pressure to reduce its use of single-use plastics.
There’s greater attention on the emissions and waste outputs of agricultural supply chains, with food and drink industries, merchants and distributors needing to comply with a range of environmental and climate-related requirements. While this involves businesses reporting on their own activities, on-farm practices can also impact a supply chain’s overall sustainability credentials.
A CTS can have a positive influence, as the compatible IBCs use significantly less plastic packaging than smaller packs of equivalent quantities. For example, a 600 litre IBC uses 20g of plastic per litre of product, whereas a 10 litre container uses 40g per litre.
The time and expense typically spent dealing with waste packaging is also removed. There are no caps or foil seals to wash and dispose of, no cardboard boxes to recycle and no cans to triple rinse, dry and arrange collection for.
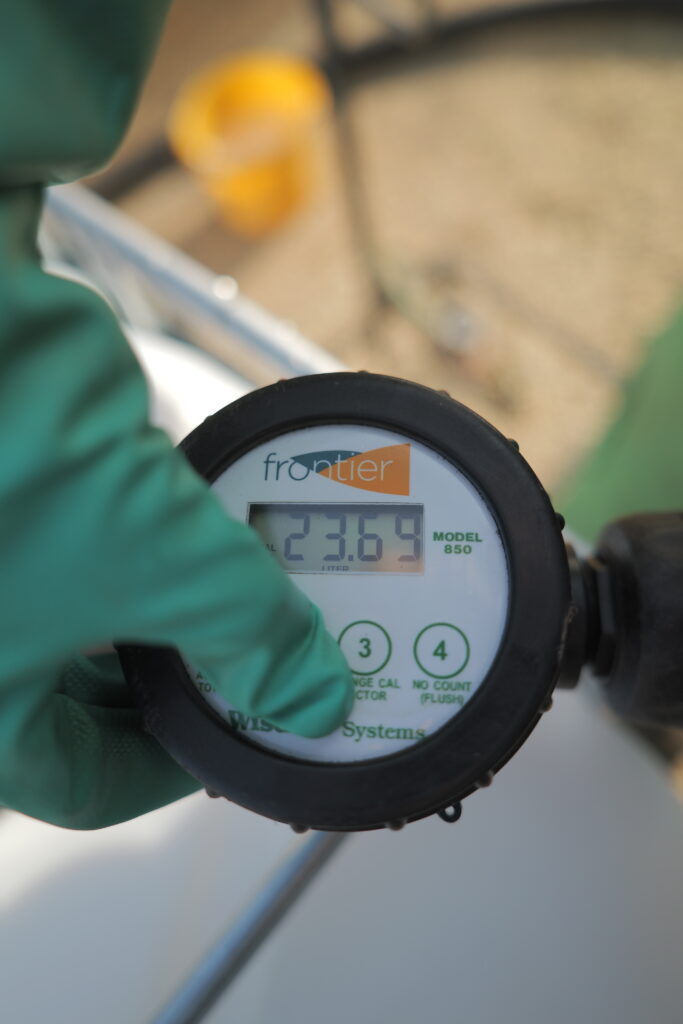
Greater efficiency for improved workloads
Improved operator safety, less manual handling and faster filling are all contributing to more efficient operations on farm – by as much as 20-40%.
Many CTS users are benefitting from one or two extra tank loads per day – a big win given the pressure of increased workloads and compressed application windows, and especially important when we consider the costs associated with having the most advanced sprayers on farm, or even multiple machinery units.
For many it’s simply not feasible, whereas a CTS can provide a simpler, cost-effective, practical solution that can provide the flexibility and time to cover more hectares when ideal conditions exist.
Growing product portfolio
When we first partnered with Wisdom Systems, it was a collaboration with Certis Belchim to launch Crown MH (maleic hydrazide), a sprout suppressant for potatoes, in 640 litre IBCs as well as in 20 litre containers that supported adoption of the technology.
When the product was reapproved by the CRD in a 640 litre container, it was stipulated that the packaging must only have a top-mounted discharge valve for use with a CTS. Growers immediately saw improvements in safety as well as productivity, and demand for more CTS-compatible products has continued to grow.
Today, we’ve equipped more than 500 farms with the FastTran 850 and our product portfolio has expanded to include Stabilan (chlormequat), Roundup Energy (glyphosate) and a range of nutrients including Cearum.
More recently, we’ve partnered with Clayton Plant Protection to officially supply their Clayton Comply product in 300 litre IBCs for use with the CTS too. An emulsifiable concentrate containing 800g/l prosulfocarb for grassweed and broad-leaved weed control in cereal and vegetable crops, Clayton Comply will be an important product this autumn that can now be handled in a safer, cleaner, more efficient way. It signals a positive move for the industry and demonstrates the ongoing recognition from ag-chem suppliers that CTS is the right solution.
At Frontier, we’ve been exploring more 600 litre IBCs versus the typical 1,000 litre units to make adoption of the technology more flexible. More 300 litre IBCs are becoming available and we’re evaluating the feasibility of a 50 litre returnable container too.
If we’re to ensure the longevity and resilience of farm businesses and food production, it’s important we make this kind of technology as accessible as possible. We’re helping many operators now retrofit their sprayers, linking growers to funding opportunities via the Farm Equipment and Technology Fund and looking forward to many more product developments going forward.
More information is available at www.frontierag.co.uk/cts
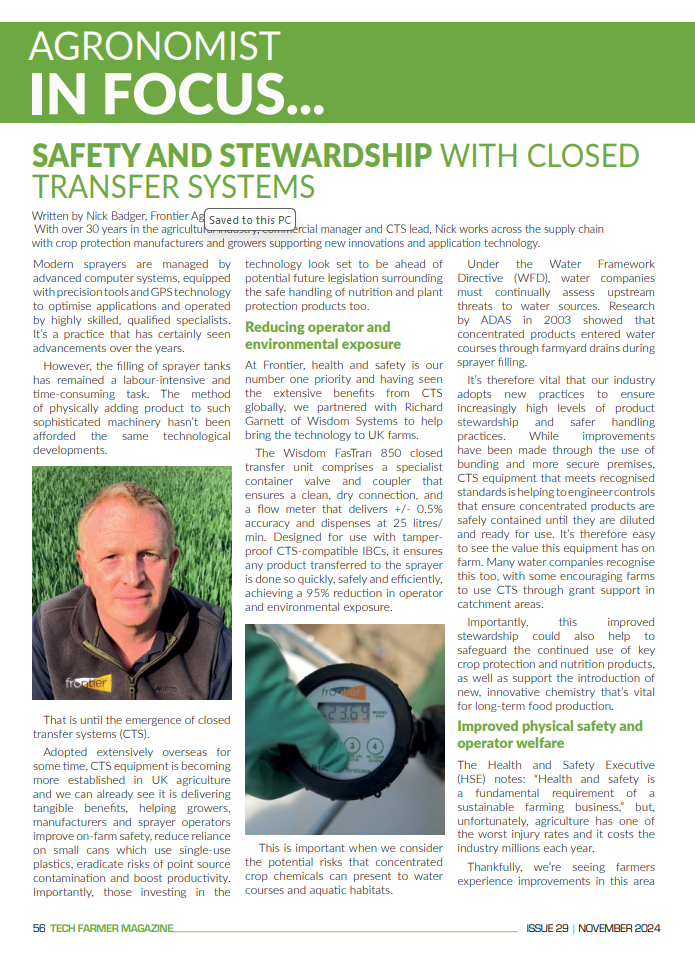
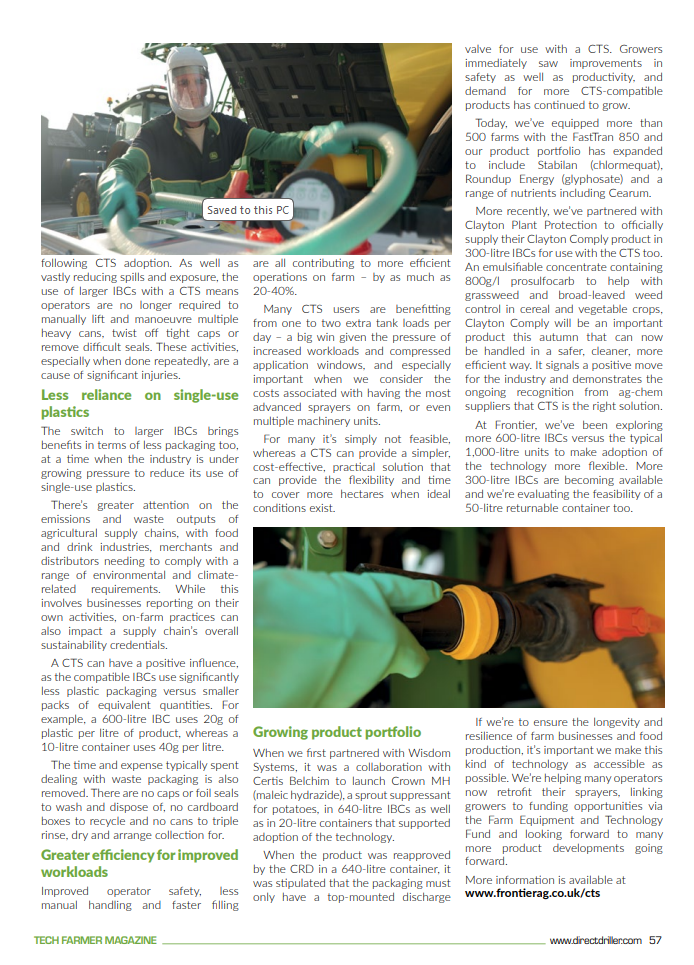