What is Near Infra-Red Spectography and how can it benefit the combine at harvest time.
Without a doubt, better information enables you to make better decisions. Information is power, you only have to look to any shopping experience where retailers will try to harvest any personal information presumably in an effort to be able to offer you an opportunity to sell you more. But within agriculture, generating information at harvest time can now provide the building blocks for the decisions that will shape the profitability of the farm for the next year and for years to come.
Yield mapping is a technology that has been around for many years now. However, if you go back fifteen years, a farm’s yield maps did little more than provide a novel wallpaper for the farm office. The key to yield mapping becoming a useful activity has been the ability to action the data generated. As farm management packages become more powerful and user-friendly, the ability to output prescriptions to enable variable fertilizer applications or variable rate seed rates have enabled farms to optimize inputs.
There are those, however, who feel that looking at yield in isolation may not give the fullest picture for example when considering fertilizer applications for following crops and a better indication might well be the quality of the crops harvested, which in turn may give a better clue of the use of nutrients – including inorganic fertilizers.
While crop quality has historically been in the bailiwick of the grain merchant, a relatively new technology has now become available to the farmer – Near Infra-Red Spectroscopy (NIR).
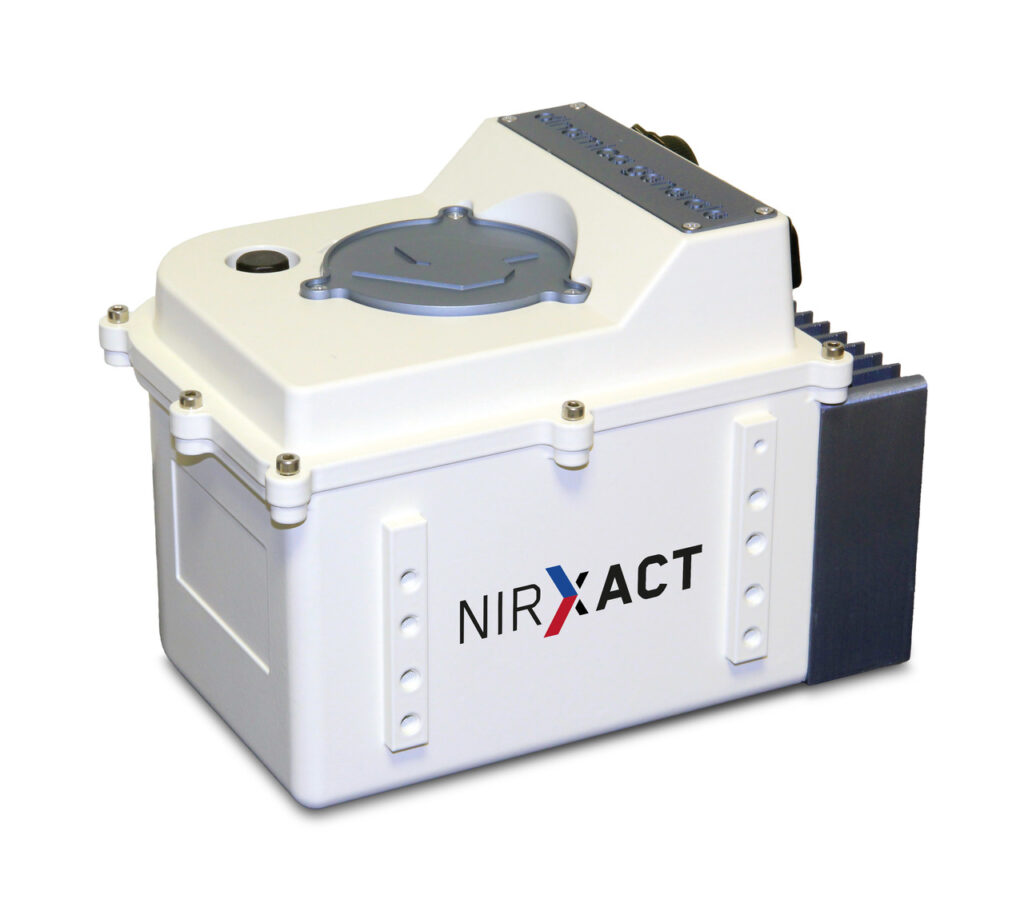
NIR uses a light source to shine at a passing crop, and the reflected light is then interpreted to be able to determine the composition of the crop in real time. While the technology has traditionally been seen used in forager applications, where the knowledge of the nutritional composition of forage was an invaluable tool in establishing effective food rations not just for livestock but also to give those running Anaerobic Digestion plants a more scientific means of balancing gas production. That very same technology is also now available to New Holland combine operators in a factory fitted option for 2024.
The sensor uses different crop ‘curves’ to allow for the different responses as a result of different crops or even varieties. While three curves are included with the base sensor, more calibration curves can be added at a later date as needs and requirements change.
Mounted onto the lower part of the clean grain elevator, the combine NIR sensor scans all the grain on its journey to the grain-tank, given the farm protein information and moisture in cereals as well as oil content when harvesting oil seed rape.
The information can be displayed on the IntelliView IV monitor in the cab and then is incorporated into a layer on the yield map, where, with further interpretation, it can help shape future fertilizer and seed applications.
An interesting use of real time NIR data come from Australia where the adoption of the NIR sensors is further along than we can see in Europe. Rather than use the data solely as a basis for nutrient applications, combine operators in Australia use the data to be able to segregate grain of different quality.

With clearly defined quality criteria for grain, the farm can then subsequently blend different grain proteins in order to get everything ‘over the line’ for a quality premium. While not many farms in the UK have the facilities to segregate grain in this manner, it may be considered that as this information was never previously available to the farms, the need has never previously arisen. With some already segregating grain for moisture – it is only a small step to separate out crop on another criteria.
One useful aspect of the NIR sensor on a combine is that it is not confined to the combine when the combine is put away for the winter.
The sensor that is used on the combine is the same sensor that is used on a forager as well as being able to be used in a slurry application – either on the output from the slurry lagoon or even on the slurry tanker itself. All that is required to change from measuring grain to forage to slurry is the mounting kit and the dedicated curve for the material being measured. The sensor itself is the same.
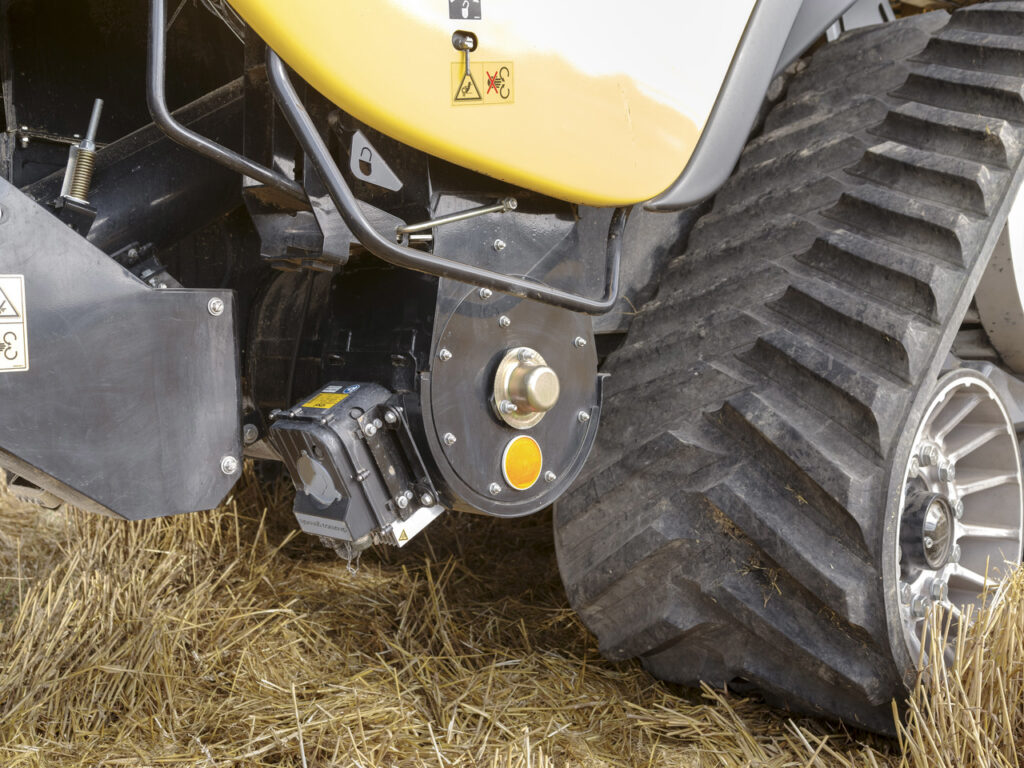
Being able to consolidate the crop quality information within mapping opens up a world of possibilities to the modern farm. Where margins are tight and the cost of inputs is often the deciding factor between profit and loss, having the information at your fingertips to be able to make better decisions may well prove to be the difference. Crop quality information alongside traditional yield information, may prove to be the missing link that raises the usefulness of mapping beyond wallpaper for the farm office.
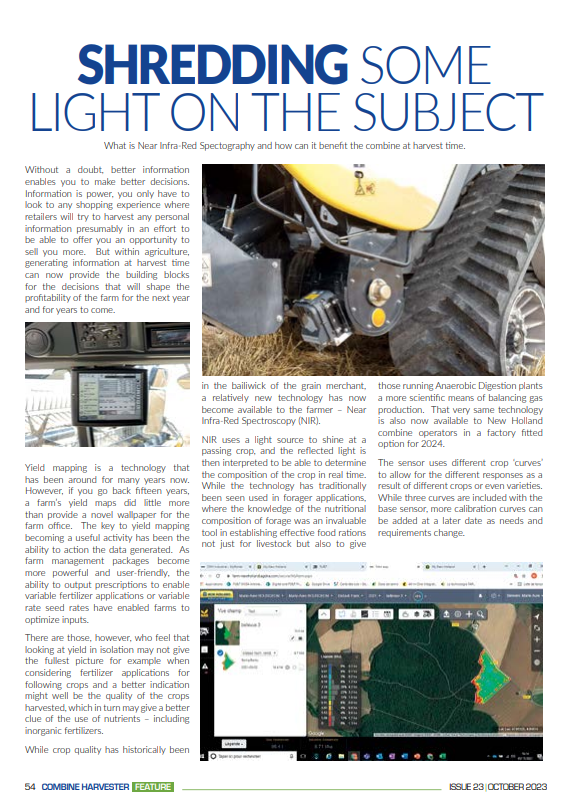
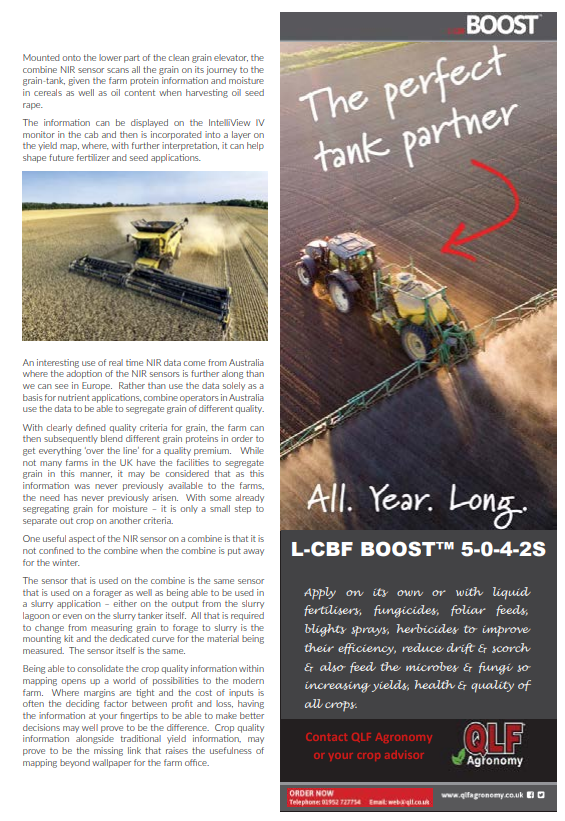