Originally written by Frédéric Thomas – and published in TCS Magazine in August 2013
Cutting with water Ultra High Pressure (UHP) technology is rapidly developing in the industrial world. We appreciate its ability to quickly and cleanly cut virtually anything. In agriculture, the need to precisely cut is just as much as requirement and in many different situations, with one such application being opening a furrow for direct seeding. Greg Butler, one of our Australian colleagues SANTFA (South Australian No-Till Farmers Association) who has had the ingenious idea of using UHP technology. Here are his reflections and the first results of its feasibility study.
The heart of this innovative approach, patented by SANTFA, is to replace the disk opener by a UHP waterjet. This could cut waste and even opening the floor without risk of including vegetation in the furrow. Open the furrow in this way requires much less pulling power and also wear on the components. The device could be provided by manufacturers as an option or available in kit form for mounting on older seeders.
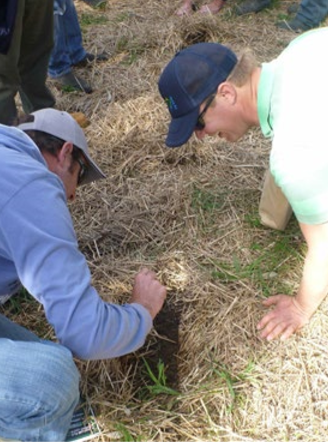
Not Just Water But Also Fertilizer
Although the technology was developed with water, other liquid products such as nitrogen fertilizers may be used in the mixture. For phosphoric acid, which may precipitate under high pressure, tests are needed to determine whether it could be used as a cutting agent for the “liquid coulter.” Although the addition of fertilizer is not fully tested, this combination would reduce the requirement to transport liquid products and double the usefulness of the application with the bonus of a precise location of fertilizer. It appears, moreover, that injecting a fertilizer in this manner increases the dispersion into the surrounding soil furrow, thus reducing the risks of toxicity while increasing efficiency. This method could be particularly interesting for often sown rapeseed varieties in the presence of a large straw mat. Moreover, this little seed is very sensitive to crop residue in the groove and young plant appreciates a bit of a boost in fertility. If chemical fertilizers can provide additional benefits, it is probably best to forget organic products, such as inoculants or other bacteria. They cannot survive the pressure in the pump, or the driving force to the nozzle outlet.
The First Feasibility Tests Are Encouraging
To better assess the feasibility of this innovative idea, a series of experiments were performed in March 2011 at Flow International’s UHP Advanced Testing Facility in Jeffersonville, Indiana USA. The majority of tests were carried out at 15 km/hr; an execution speed is the maximum speed of sowing using disc systems. Depending on nozzles and pressures used, the volume of liquid needed however, is between 80 and 22 l / ha; which is an amount in line with the needs of fertilization and transportation options.
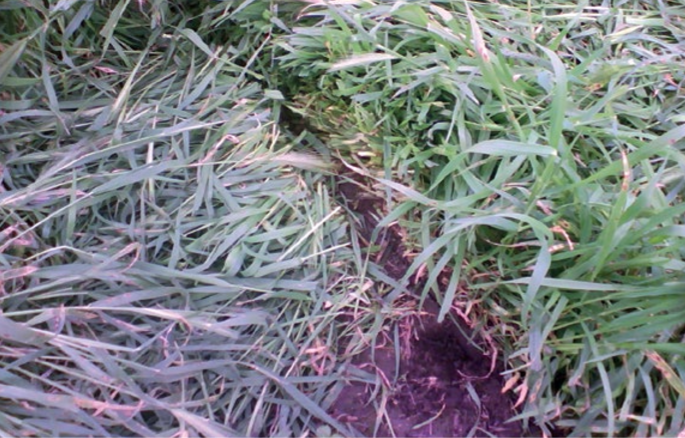
At this point, the spacing between crop rows becomes an important factor by limiting not only the number of cutting nozzles but also by reducing the volume of liquid required per hectare: standard gauge used in all calculations is 33 cm. The nozzle wear was also analyzed. Unfortunately, we are using the smallest holes, as they require the least amount of liquid, but that makes them the most susceptible to wear. Finally, the power demand can be quite important with the UHP, this was also evaluated knowing that the pump can easily be positioned directly over the tractor’s PTO with returns of 90-92% on average against 70% a hydraulic drive. It would be relatively similar to that required for the tension opener discs and the operation of the pressure and volume of water required: between 3.5 hp and 11 hp per item depending on soil conditions and depth seedlings.
In terms of cutting waste, the tests yielded the expected results: the ultra high pressure jet cuts the same straws if they are wet or positioned on clay and greasy soil. The inclusion of “hairpinning” residues as may be the case with the discs is therefore virtually non-existent with this principle.
In terms of Operation: if nozzles and average pressures are adjusted, penetration is enhanced with larger nozzles and higher pressures. However, this type of equipment and the volume of water required, approaches the limits of what can be seen in agriculture using a mobile tool.
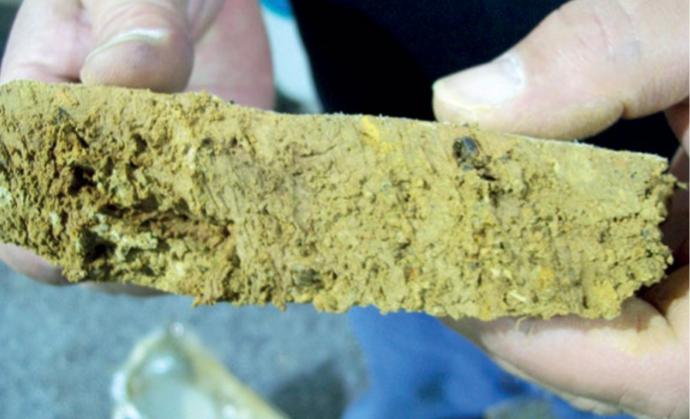
A Great Idea With Many Agronomic Openings
After these initial laboratory tests confirmed the feasibility of this idea, if Aqua-Till is implemented on a drill, it can bring interesting agronomic benefits. Improvements to residue management from the surface of the groove (keeping trash out of the slot and away from the seed), the “coulter liquid” also may allow a significant extension of drilling windows in dry conditions where the power requirement and the wear are the limiting factors. Can when its wet, not having a mechanical element, eliminates chances of smearing, which could lead to anaerobic conditions for the germinating seed. In addition, even if the power required is similar, in proportional conditions and the same sowing depths, the “liquid coulter” requires no pulling power.
The size of the tractor can therefore be reduced due to the design and build of the drill. The Aqua-till concept is perhaps best suited to Seeder drills. Certainly it is seed drills using the Aqua-till concept that are most likely to emerge in the first place. However, Greg Butler went even further in his thoughts. Using a jet under UHP to cut waste, open the fold and place the starter fertilizer, he plans to position the seeds with an “air-gun” located just behind the jet and fertilizer. The only real contact with the ground would be a small press wheel to close the hole.
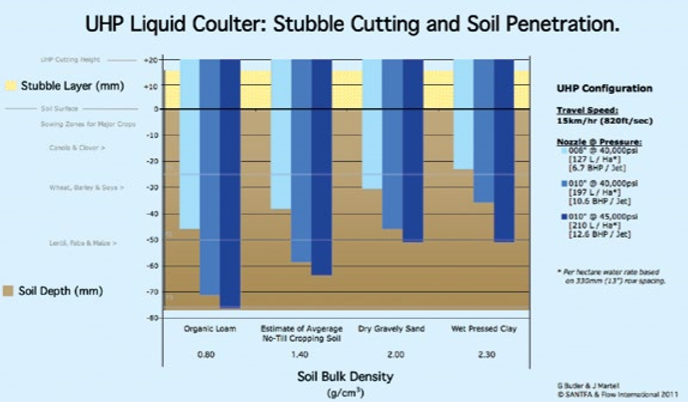
Ideally, the depth control would be determined by an electro-magnetic density sensor that adjusts the working equipment according to the ground variations. Finally, the “liquid coulter” may operate continuously or synchronized with the delivery of seeds. This option would significantly reduce the volume of water required but also the power to the pump level and is particularly well suited to a Seeder and would allow us to exit the compromised “disk” and move towards seeding point by point with the additional benefit of the precise location of fertilizer: ideal for planting.
Although this idea, which is only a concept at the moment, may seem some way off, it is most definitely possible and tests are planned soon in South Australia. It also proves that technical advances such as this, as elsewhere in industry, allow us to take agricultural problems and create solutions that allow us to farm with greater ease and success.