Horsch, a Return to Direct Seeding
Originally written by FrƩdƩric Thomas and published in TCS in August 2015
While this may be a surprise many, Michael Horsch is first and foremost a farmer, not a designer and manufacturer of agricultural machinery. The opening of East Germany after the fall of the Wall in 1989 allowed him and his family to expand its farming and implement new equipment and test its expertise, while refining its farming strategies. Therefore, his outlook, his analysis and action have always been oriented towards the search for efficiency for farms. A pioneer in simplifying tillage 30 years ago with the Seme-Exact, today it is the management of soils and the development of a comprehensive approach involving the location of traffic that leads back to ideas around tillage.
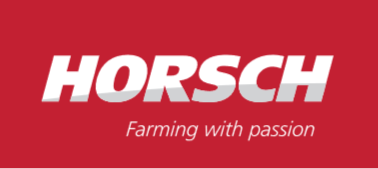
From the Seme-84 through the Delta Sem and soc Duett (PPF) to the Terrano and Focus (a form of strip-till) it is looking for solutions that are efficient, sustainable and consistent agronomically which motivates Michael Horsch. Although his company is still growing and takes the majority of his time, he has always kept his āeye inā as a farmer.
The management of the company farms in the former East Germany and the Czech Republic continue to challenge the way he thinks and mean he has to continually refine his agronomic strategies. It is this collaboration between the field scale tests and the machinery industry that enables the design and development of appropriate technical solutions. This attitude is shown in the way he has tackled the world of spraying, where he does not hesitate to challenge convention by proposing to greatly reduce the risk of drift by tracking the spray target.
It is sufficiently accurate to develop a proactive boom height management system to maintain height above the vegetation to less than 25 cm. In terms of tillage, Horsch has endeavoured to propose solutions for the reduction of the number of passes and therefore the costs of establishment.
In this context, direct seeding has been studied and comparing devices following standard practices on the Schwandorf family farm operating in Bavaria has produced reliable results. It shows that under these specific conditions and without peripheral changes, it is this approach in min-till to 20 cm which is the most effective in providing consistent results, even a slight performance gain while providing mechanization savings (25 l / ha fuel economy compared to ploughing). This notion is also a very important issue in a world where the price of land as an input requires a reliable operating system, notably with major operating sizes.
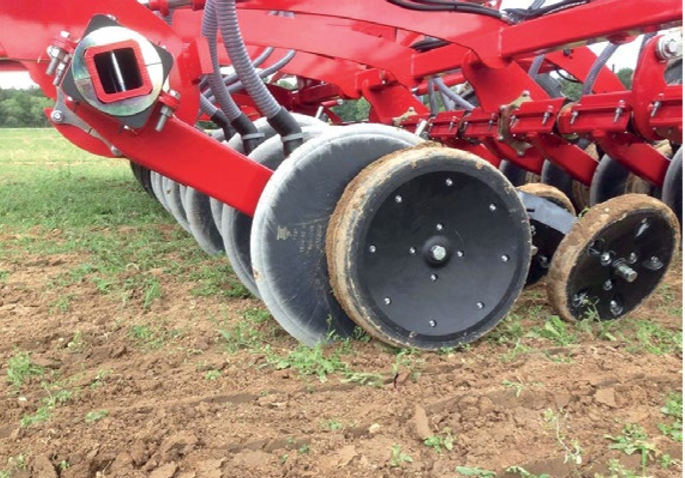
Learning Maize Cultivation
With the acquisition of a farm in the Czech Republic in 2002, Michael Horsch was faced with growing maize in clay soil. This experience promoted the use of the striptill, but also the idea that it is important to minimize traffic. With the acquisition of another farm north of Prague also on very clayey soils, it definitely became worth investing in the location of the traffic (controlled traffic?) of all passes with a correlation on the land between sprayer (36 m), tillage and drill (12 m). This new experience enabled him to understand and then demonstrate that it is primarily the wheels and trafficking, particularly in clayey soil, which requires remedial action to the ground to recreate a porosity and become even easier to till in the next run. Therefore, if the movement of machines is firmly confined to less than 15% of the area (target of only 10%), the soil retains its structure and porosity. The removal of deep work becomes possible and mintill becomes feasible. It is particularly interesting that in CTF (Control Traffic Farming), one must be able to work and sow especially with the equivalent width of the cutting combine to facilitate alignment of the passes.
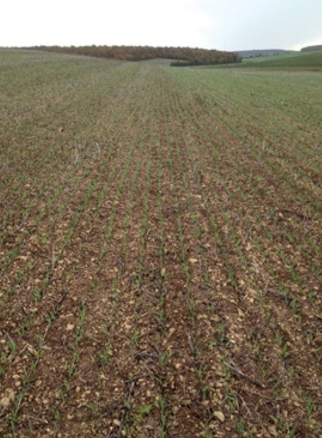
Weed Grasses – And Resistance Develops
The second concern is the weed situation in Northern Germany and other major grain Eastern countries. Grasses, in France, are widespread and are becoming
resistant, control costs are becoming too high and therefore dead ends appear in farming practices. Even if the rotations are a little tight, it is increasingly clear that it is not intensive tillage that is the solution. Rather, it appears that a strategy of non-disturbance of the soil at planting, removing the operation that triggers germination, is more suited to reducing the weed grasses; another plus point for direct seeding. This is a form of holistic approach based on the location of the traffic and decreased risk of weed grass always in combination with a search for efficiency and reduction of production costs which lead to Michael Horschās interest in tillage. With Horschās communication strength and newly developed machines, it is certain to positively move this issue at European level and to change the perception of many farmers and technicians.
Development And First SD Seeder Trials
After the design of a first seeding element for Direct drilling in 2013, Horsch built a drill prototype in 2014 that worked that autumn in Haute-Marne to test and validate the options he considered. After this first round using discs, two new machines, with the latest developments, were trialed in summer and autumn 2015 in the same area and also with clients elsewhere in France. The idea is to challenge the technical choices in different conditions. In parallel, other farms in similar situations are running tests in Denmark
and Germany To limit soil disturbance while maintaining good control of the sowing depth, the single disc solution has become fact for Horsch.
While considering the approach of the JD 750, which has been widely tested, Michael Horsch and his team adapted their drill so that it met their specifications and injected their expertise in the design and construction. The support arm is cast steel to give it more rigidity. At the front it is attached to a square section bar by a flanged system and rubber pads. This choice now has well proven reliability and acts as a damper to stabilize the machine and also individually each element. The penetration pressure is hydraulically adjustable from the cab made possible by pivoting the support square on itself. It should reach 200 kg / coulter.
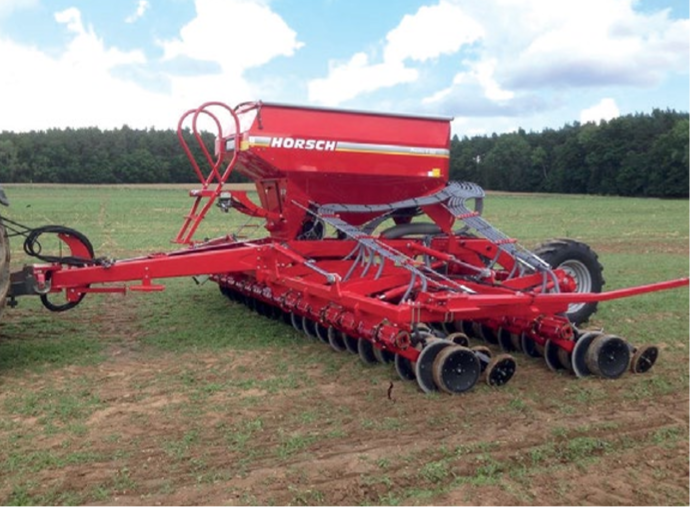
In terms of disk opener, the Horsch has chosen a large diameter (480 mm) to better cut through trash but the working angle has been reduced to a small angle, again to minimize disruption to seeding. The gauge wheel that is attached to it is a smaller diameter (400 mm) and wide enough (115 mm) to be as effective in controlling the depth in previously worked soil as in post-harvest stubble when seeding Direct. Finally and still for reasons of reliability, the bearing is also of a large diameter (65 mm) in an oil bath and with two tapered roller bearings in order to better absorb the lateral forces. The seed boot adjoining the disc was also slightly refined for the same reasons. It is protected by two tungsten plates and is adjustable in height relative to the disc (3 positions).
Finally and like the original, the seed is stopped and pressed in the ground by a wheel that follows in the groove. This is, however, equipped with a scraper and is retractable if the sowing conditions do not allow its use. Then the groove is closed by a side wheel, which it is possible to adjust for pressure (3 positions). Beyond these elements, the originality of the direct sowing Horsch line is the integration of a sweeping tine at the front. This option is not yet finalized really in shape but it is certainly useful to establish seedling lines including through straw for rape or to sow in straw covered stubble immediately after harvest.
The location of fertilization is also integrated to compensate the non-mineralization through cultivation at planting. The drill will be equipped with two hoppers with placement of the fertilizer into the same groove. For now only the solid fertilizer version was available. Finally the frame, which we believe now has been completely finalized, will carry fixed hoppers and retractable hydraulic coulters.
Horsch has already integrated in the design integrated ballast masses on the front and rear hoppers. Although this prototype is not yet completely finalized, it is already very functional and will perfectly fit into the overall strategy defined by the manufacturer / German farmer. Mr. Horsch is investing convincingly in the market for no-till seeders.