With high value, comes high risk, something Will Parrott knows all too well.
Springhill Farm – part of Evesham Vale Growers – in Worcestershire. The farm is home to a crop fed anaerobic digester and is the UK’s third largest grower of salad onions with a total area of production stretching upwards of 1,600ha (4,000 acres) annually. In addition, as a group, they supply almost a fifth of the total UK market for tomatoes, 52 weeks of the year – supplying both supermarkets and wholesale customers.
Cereal crops grown include maize, wheat and triticale, grown for grain and wholecrop as well as grass. “All of these crops provide feed for
our own AD plants,” explains Will. “Our teams manage the entire growing process from seed, drilling, agrochemical and digestate applications, as well as harvesting, and packing for all of the spring and salad onion varieties we sell.” “We harvest every product by hand, and we then process the onions in our purpose-built packhouse at Springhill Farm. All salad and vegetable growing is carried out within a 20-mile radius of our packhouse, helping us provide the freshest produce possible.”
With such a high demand and value for the crop, careful management is required at all stages of the growth cycle to ensure maximum yield and quality crops.
Dealing with disease
Disease is a huge threat to vegetable crops, and so Will works closely with his consultant Dominic Swainson, senior agronomist at Agrii.
“Downy mildew is the biggest problem and sometimes means we can be spraying weekly for it,” explains Dominic. In terms of the programme, mancozeb and metalaxl-p in the form of Fubol Gold, is key for protection he adds, together with Amistar (azoxystrobin) and Orondis Plus (oxathiapiprolin). There are also early applications of Signum (boscalid + pyraclostrobin) employed to help with white rot, a soil borne disease of alliums.
The main risk timings are April-May and also August-September because this is when moisture and dew points on the leaf are at their highest. “Shorter days means longer time for the dew to be sat on the leaf,” says Dominic. “Irrigation in hot dry weather also runs the risk of raising humidity levels and conditions conducive for downy mildew.
Many of the fields suitable for onion growing are on lighter soils close to the rivers which also adds to the humidity. Some of our summer production is moved up to the Cotswolds to spread growing period and risk, but they also run the risk of staying damp longer in cool conditions.”
The location also impacts fungicide application, forcing Will and his team to frequently spray in less-than-ideal conditions, meaning he often needs to incorporate an adjuvant into the mix. We apply all fungicides with the adjuvant Kantor as the drift reduction and rainfastness it provides are critical to us.
“We never have time to spray in a timely fashion, spray days seem to be getting less and less as the years go by. We end up against it most of the time and Kantor buys us more time.” Kantor, from Interagro, is a highly versatile activator adjuvant which contains a compatibility agent – a self-emulsifying agent which helps products mix thoroughly together, even in cold water, and remain in solution without phase separation. “Kantor also works as an anti-drift aid and benefits coverage and retention, helping keep chemicals where they need to be,” explains Interagro’s Stuart Sutherland.
Agrii agronomist Kathryn Styan, who also works alongside Will and Dominic, adds that as well as the rainfastness benefits on the farm, Kantor helps fungicide retention on salad onions in particular. “Onions grow very upright, and the leaves are very waxy so it can be hard to get the fungicide to stick on.
But effective coverage is absolutely crucial to keep the downy mildew out, so the other major reason we use the Kantor is to help maximise coverage and adhesion to the crop.”
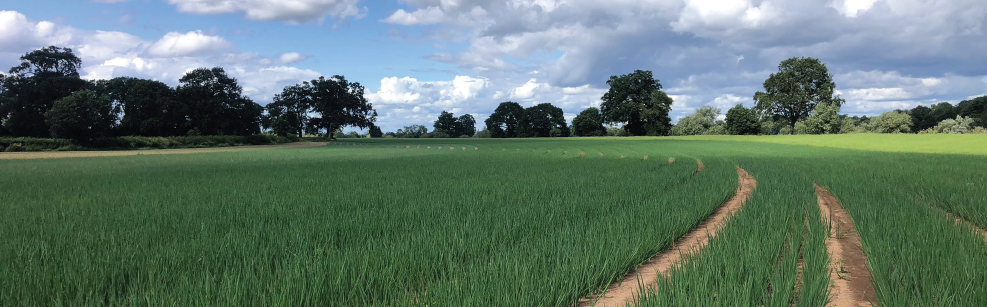
Battling weeds
Keeping the salad onion crop weed-free is also essential as onions are not very competitive and this is worsened by a groundsel endemic at the farm, notes Dominic. “With this in mind, we mostly use repetitive low doses of residuals with the addition of Backrow Max to protect the crop.”
Designed to enhance residual herbicide performance in challenging conditions, Backrow Max is another specialist activator adjuvant from Interagro which has been proven to reduce drift and enhance retention in the soil.
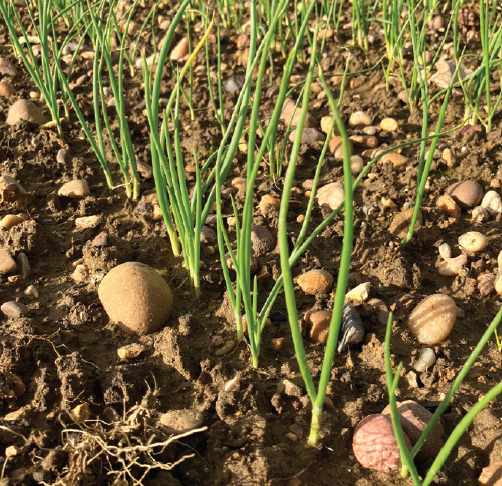
Delving further into the programme, pre and peri-emergence applications of Wing-P (dimethenamid-P + pendimethalin), Stomp Aqua (pendimethalin) and Backrow Max. This is followed by repeat low doses of Wing-P and Emerger (aclonifen) all within three weeks of
each other.
As well as optimising the efficacy of the herbicides, Backrow Max brings valuable crop safety because it retains the residual herbicides in the weed germination zone – the top 5cm of the soil, explains Dominic. “Consistency of emergence is crucial so we cannot afford to knock the crop with herbicide damage, particularly if we’re irrigating in the drier conditions to aid emergence.”
Being a minor crop reliant on EAMUs, weed control is also equally challenging in the British Vale of Evesham Asparagus crop — the only asparagus of its type that can be grown in Evesham, says Will.
“We try to use a number of different residual herbicide active ingredients with different modes of action to get season long control,
as there is only one shot – pre-emergence — before the asparagus spears come up. It’s a perennial crop, in the ground for up to
10 years, so crop safety is important too.”
Looking at the programme, Will says they rely on a combination of clomazone, pendimethalin, metribuzin and mesotrione, as well as Roundup Biactive (glyphosate) pre- and post-harvest. “It’s a complicated mix, being applied in the spring when the spraying water is cold, so mixing can be difficult with settling out.”
Saving solutions
The complexities and the associated challenges with this mix came to a head in spring this year. “We went to spray the field on 21 March, and nothing came out the nozzles – it was totally blocked up and we had to spend half a day cleaning out the sprayer and unblocking it, having pumped the contents into an IBC.”
Will says that they looked into the spray tank and could see that the mix had settled out, so Dominic suggested trying adding Kantor to see if it could “rescue” the chemistry. “We decided to test it by taking a couple of cans out and added approximately 200ml in to one of the containers.
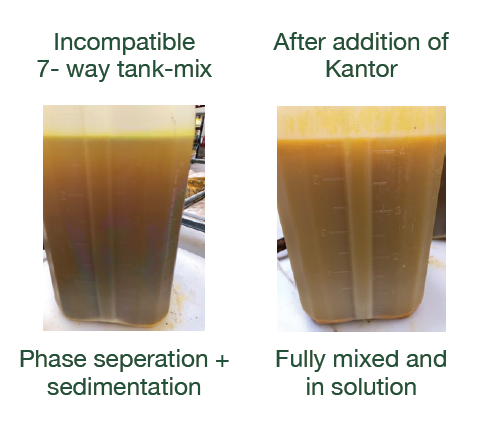
“We shook it all up and Kantor totally brought the whole mix back into a homogenous solution. We left it overnight and it was still in suspension the next morning.
“So we pumped the contents of the IBC back into the spray tank with Kantor and were able to apply to the fields with no issues to the
crop. The lesson learnt was for complicated tank-mixes, always add Kantor. It saves so much time.” Extensive testing over the years has shown
that adding Kantor to the spray tank before filling speeds up the mixing process and helps difficult mixes homogenise in the tank and
stay in solution, explains Stuart.
“Tank-mixing pesticides offers flexibility, saves time and may increase effectiveness, but it can be problematic. Adding any more than three products to the tank increases the risk of a mixing issue.” Of course, thorough mixing is crucial for pesticide effectiveness, he adds.
“Only active ingredients fully dissolved in water can be absorbed by plants. But mixing can be slow and tricky in cold water and some formulations can be hard to mix together, particularly at high pH and with hard water. You could be losing efficacy without even realising it.”
Therefore, adding Kantor to the tank before filling is a good insurance to avoid a mixing problem and achieve dependable crop protection performance, says Stuart. What’s more, although growers should take every precaution to avoid a tank-mixing issue, with time and effort it may be possible to recover a problematic tank-mix using Kantor, as Will proved this spring.
“Once the products have been successfully re-suspended, apply with constant agitation to avoid any further issues,” advises Stuart. With catchy weather patterns, challenging spraying conditions and crop protection weaknesses all putting pressure on the spring workload, Will says that if you can take the stress out of the operation, save yourself time and make the products mix together properly and perform as they need to then it’s a no-brainer. “Optimising the delivery of your crop protection products to where they are needed is crucial to get the most out of them,” he concludes.
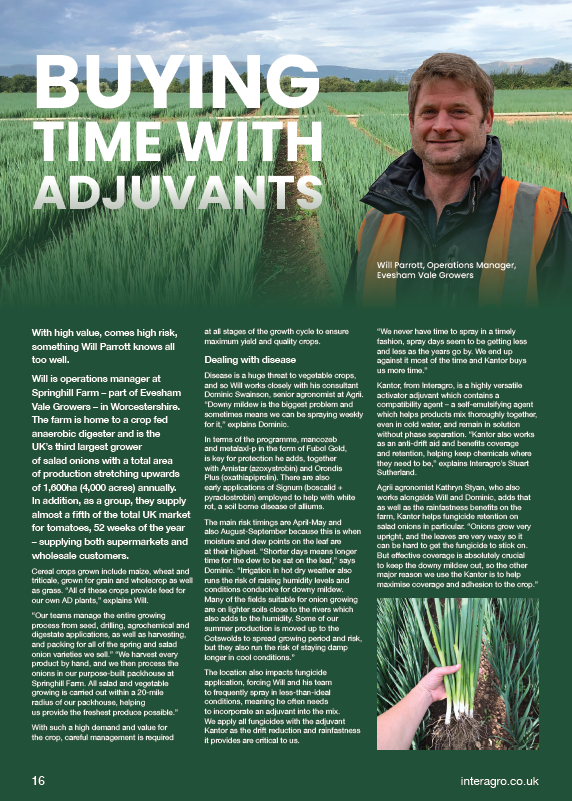
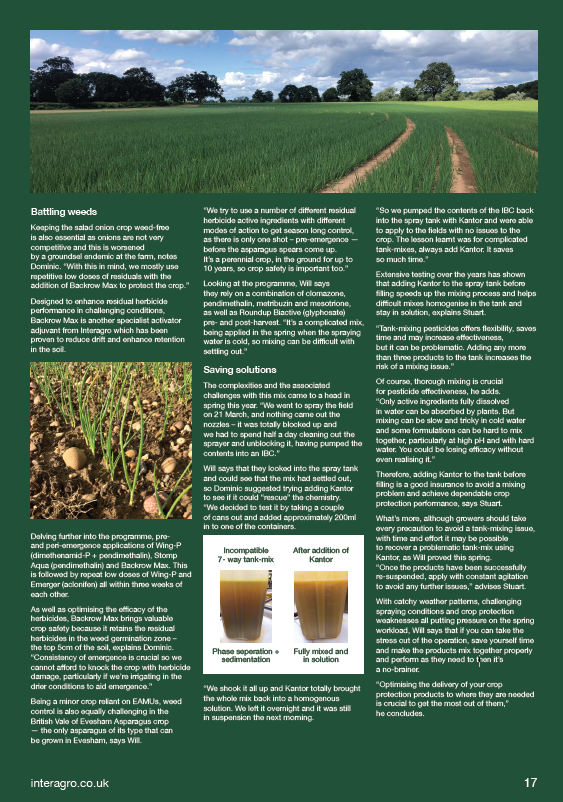