Written by Dave Ablett.
I started direct drilling in 1965, and for 21 years was at the front end of spreading the word. I started on machine design and manufacture and was responsible for the first commercially produced and sold seeding machines in the UK in 1967 and in Brazil in 1973. In those early days direct drilling was mainly promoted by the desire of chemical companies to promote sales of herbicides. I was employed by ICI ( under its various names!) and all my design and development work was given to machinery manufacturers free of charge. In those early days considerable problems were encountered because of the lack of follow up herbicides. My main design and development work was done in co-operation with Howard Rotavator Company in the UK and their Brazilian associate company FNI. In those early days the size of a seeding machine was restricted due to the size and hydraulic capacity of tractors.
The first direct drill I was involved with was the “Fernhurst coulter system” on a Massey standard seed drill. It proved to be an efficient rake when working where there was surface trash.
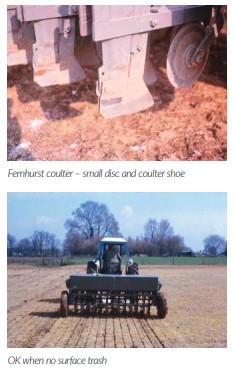
As a result of these trash problems it was thought that a powered slot cutting system would cope better with any crop residues. The first “Rotaseeder” had normal rotavator blades and moved all the soil. In reality the seed only needed to be introduced into the soil with the least soil disturbance possible so the blades were cut down to provide a narrow slot. Moving from complete width rotavating to narrow slot cultivation with coulters placing seed into the slot was a major step forward in maintaining crop residues on the soil surface. The Rotaseeder was mainly intended for grassland renewal, kale seeding and cereals.
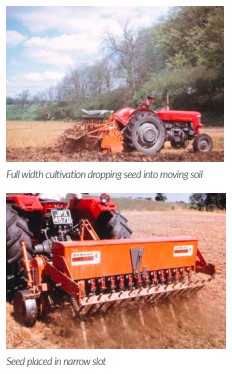
Development field work was carried out throughout Europe. A major demonstration tour through France, Germany, Spain, Holland and Denmark was done in 1966 to get farmer opinion on system.
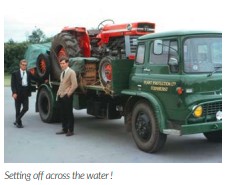
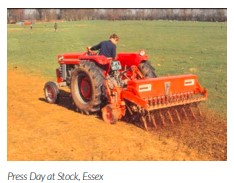
The final design was launched to the press in 1967 on a farm in Essex. Because of my involvement in design and development Howard Rotavator Company asked me to operate the machine for the launch..
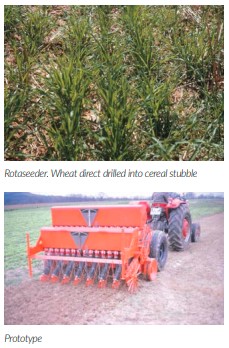
In 1967 the main problem faced by the Rotaseeder was that cutting blade wear was too severe when seeding stony or sandy soils. Also rate of work was slow compared to conventional cultivation seeding machines. Not needing to plough or carry out further tillage operations were not taken in to account when farmers were under pressure to get the seed in the soil. The Fernhurst coulter and triple disc systems left open slots which were an ideal habitat for slugs. The Rotaseeder did not suffer slug problems to the same extent. As a small side diversion I encouraged Howard Rotavator Company to build a trailed machine capable of putting fertiliser on with the seed. It had to be a trailed machine because tractor three point linkage was not strong enough too lift a double hopper machine. I did a little work with it but Howard’s development engineers were too busy involved in big balers and rotary muck spreaders.
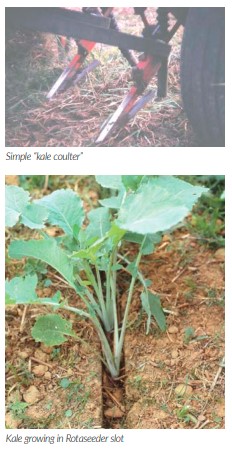
Rotaseeders were produced by both Howard Rotavator Company and WMF, their main use in later years was for grassland renewal. Indeed until a few years ago a machine was being used in Wales to stitch in grass seed after a silage cut. No herbicides needed! Kale was a popular crop with dairy farmers but they had serious poaching problems when grazing a conventionally seeded crop. I designed and developed a simple “kale coulter” to put seed into a simple slot with minimum soil disturbance thereby maintaining a firm surface when grazing. The slot producing coulter was a modified injection tine with a simple brush feed seed mechanism. I went on secondment to Brazil and my successors in the UK got Gibbs of Ripley to make a complete simple machine available. A new team of engineers were taken on by the Machinery Section to work on direct drilling coulter systems and and I moved on to design and development of specialised spray attachments to apply Gramoxone for weed control along the row of plants in orchards and vineyards mainly in Eastern Europe..
In February 1972 I was seconded to Brazil, mainly to develop sprayers for weed control in coffee and citrus. I was also heavily involved in the Direct Drilling campaign. Mid August 1972 I was asked to visit a farmer in Parana State to advise on direct drilling soya beans. The farmer had visited me at ICI when he was on a visit to family in Germany. On his farm in Parana he had made a copy of the first prototype UK Rotaseeder. He was using full size rotavator blades cultivating the whole area.
Parana and the other two southern states of Brazil are hilly and all planting was done following contours. Double cropping of wheat followed by soya beans was the standard farming practice. Also heavy rains at soya planting time – late August onwards – gave serious problems of soil erosion. This washed the standard incorporated herbicide down hill and into the water systems and rivers. The terra roxa soil had no stones and made soil moving seeding machines less prone to wear.
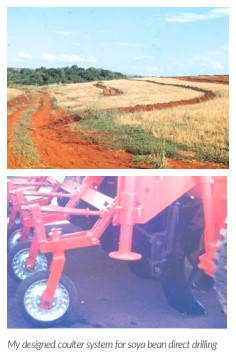
I immediately went to FNI ( Fabrica Nacional de Implementos) who were Howard Rotavator Company in Brazil and suggested we should make a mounted direct drill capable of seeding both soya beans and wheat for use on contour farming system areas of southern Brazil. ICI were in the process of setting up two development teams to promote direct drilling. One based in Parana and the other in Rio Grande do Sul with the principle aim of promoting herbicide sales. They had initially planned to use direct drills imported from the UK but my provision of locally made Rotacaster’s solved their seeding problems.
My design of a new coulter system was rapidly taken up by FNI. Because disturbed soil could dry out the coulter placed the seed at the bottom of the narrow slot and a following press wheel gave excellent seed to moist soil contact. Tractors were getting bigger but still good manoeuvrability in the contoured fields was imperative. This seed placement system consistently gave the best germination performance when compared with others including conventional methods. Direct drilling was called “Plantio Direto” in Brazil and I had helped the Parana development team make an audio visual of the system.
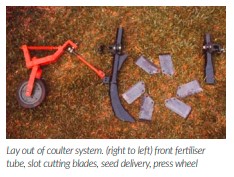
The FNI Rotacaster was launched at the 1973 Sao Paulo state fair. I believe some 80 to 100 machines were made and sold during the few years it was in production. ( Unfortunately FNI followed its parent Howard Rotavator Company into liquidation).
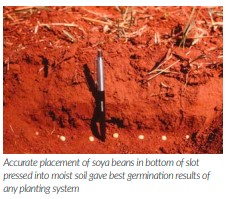
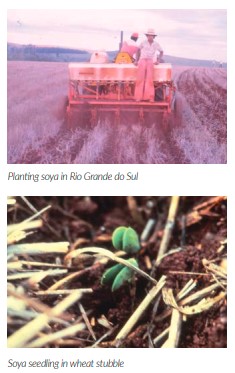
ICI UK had sent a triple disc coulter equipped machine to the team in Parana. It could not cope with soya bean seeds. The double discs both crushed and broke the seed skin and also gave erratic seeding depths. Often on the surface of the slot. I designed an improved “kale coulter” so that the team could use the seeder as a test unit for herbicide application systems. Also Jaime Ozi, president of FNI, had imported a Bettinson triple disc machine with a view to manufacture in Brazil. This had the same problems when seeding soya beans so I made a similar “kale coulter” design for him. My coulter design was to replace the triple disc. The depth wheel which was adjustable to control depth of slot also gave good seed to soil contact to optimise moisture availability.
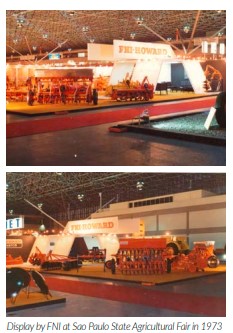
Other planting machine manufacturers were only half heartedly interested in direct drilling.
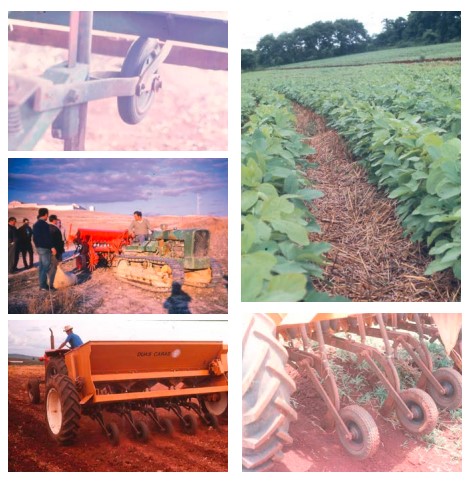
in the southern states because their machines were planters and not suitable for wheat seeding. Main problem stopping uptake of direct drilling during the early/mid seventies was the lack of over the top herbicides to aid weed control during the growth of the soya before a canopy could be formed. If there was poor wheat stubble cover then a few weeks after seeding weeds could take over! I designed many tractor mounted machines with a view to applying herbicide along the row. None were produced because a fortunate development, coinciding with my return to UK, was the availability of selective herbicides.
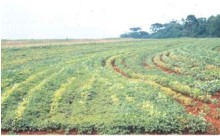
Back in the UK with Alan Bloomfields team from 1976 – machinery technical service and visitors, and specialised Gramoxone application equipment including demonstrations of my citrus machine mounted on a Landrover in north Africa. I was sent on secondment to Argentina in 1978 and moved from machinery design and development to herbicide systems management. Several suitable direct drilling planters were being made suitable for handling soya beans on the flat pampas. I set up a “specialist” team of distributor/ agronomists to promote “Siembra Direto” – local term for direct drilling. I also organised an Argentine conference on direct drilling held in Rosario and sponsored by Duperial the ICI local agents. I produced herbicide tank mix recommendations to improve weed control and an audio visual system for use by the distributors. I also gave a couple of thirty minute technical TV shows on Siembra Direto.
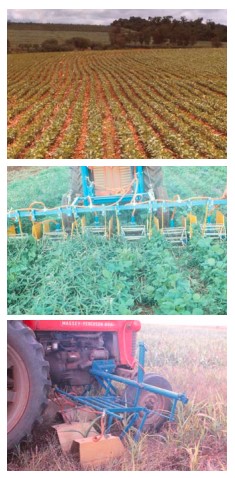
After Argentina I almost immediately went on secondment as Techno/ Commercial manager to Nigeria. Included electrodyn work in cowpeas in cooperation with IITA plant breeders and also writing the users operating handbook/leaflet.
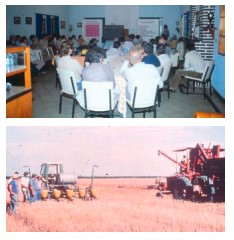
Back to minimal cultivation and maintaining surface crop residues I was sent to Canada in 1984 to put some sense in to chemical fallow. For years ICI had been promoting the use of a herbicide to control weeds during the fallow year of the Canadian prairie wheat producing system. It was clearly apparent that low wheat yields could not support high cost of herbicide so I finally killed the project. I did actively promote the system of minimal cultivations for winter wheat following the introduction of improved winter wheat varieties. This kept the stubble on top and prevented soil erosion by wind. In the prairies there are 400 kms of wind per day! Following on from Canada in 1975 I was seconded to ICI Americas and based in the mid west -Kentucky. Not involved in machine design, as there were many no till planters available for direct drilling. ICI contact herbicide Gramoxone had been sold by Chevron in the USA and it was being taken back in house by ICI Americas.
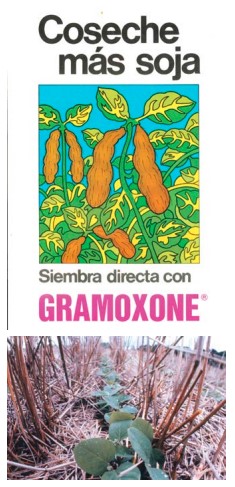
My project was to develop the best tank mixes recommendations and train the ICI Americas local staff in how the herbicides and systems work. I had development sites from St Louis , Missouri across to Delaware and down to Tennessee. Some six sites in all. In September 1986 I left ICI before completing the secondment and was headhunted to run the Cooper, Pegler sprayer company. In 1989 I took on a Hill farm in Wales and in the third year I was loosely involved in direct drilling! Having a suckler cow and sheep enterprise I was making silage. Perusing the local farming press I found a 4 metre Moore Uni drill for sale cheap. I bought it and a local engineer helped me cut it down to two and a half metre width which meant I could get down the narrow Welsh lanes and stitch grass seed into silage stubble for my neighbouring farmers. Stitching in and then applying slurry gave excellent establishment results.
Now retired and reminiscing I realise I was actively involved in Direct Drilling on and off for over 30 years and still maintain an active interest in Direct Drilling and |No-Til worldwide.
NB at a machinery exhibition in Rio Grande do Sul in 2007 the FNI Rotacaster was exhibited at the entrance to the show as the “PIONEER” of direct drilling in Brazil.
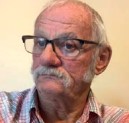