Knowing basic infrastructural information about fields is a key requirement to unlocking technological progress for an Oxfordshire wine producer. Tech Farmer visits JoJo’s vineyard.
By Mike Abram
Three simple words explain why Ian Beecher Jones, and his partner Tess, started the 2ha JoJo’s vineyard that nestles on the chalky slopes of the Chiltern Hills, not far from Henley on Thames.
“We like wine,” he says.
“It was as simple as that. We had a field, don’t have any kids and thought this would be a jolly good idea to do for the next 20-30 years.
“And it still is, despite the trials, tribulations, traumas and costs.”
It was what Ian considered a simple request post-planting in 2019 that led him down a route of actively seeking projects and partners that could improve the use of technology in vineyards.
“When we planted, the contractors were using a New Holland tractor equipped with an IntelliView IV monitor, they’d set up their RTK base station, so I was thinking this is wonderful,” he explains. “The planter will be connected, and I’ll be able to get a USB stick with data pinpointing where each and every vine had been planted.
“But when I asked for that USB, it was as if I was asking for meteorite from Mars because they had never been asked for vine position data before. No one saw any value in it.”
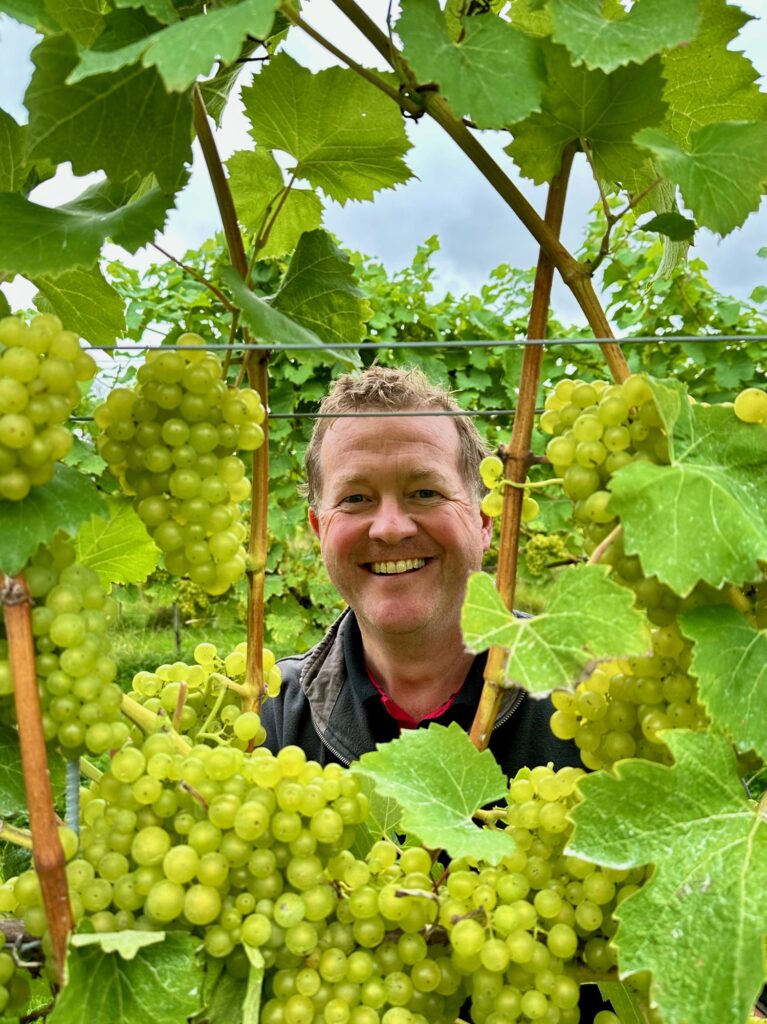
The value in Ian’s mind is that because a vineyard’s infrastructure – the vines – are in the same place year after year, it lends itself to automation, for example. “But if I want to get a robot, drone or section control working in the vineyard, I need to know my infrastructure, where my rows are to then calculate where my mid-row is.
“Once I have that, I can navigate robots or tractors through that. Or if I’m using drones, I want to know where the mid-row zone is, the non-vine signal.
“In our vineyard, it’s about 1.8m which is just grass or cover crop, and if you are looking at NDVI maps or satellite imagery, you have a huge amount of distortion from non-vine signal information. And that comes back to infrastructure. If you know where the row is, you can draw a polygon around it to give the mid-row area that can be cut out of the imagery being gathered.”
Virtually all providers of precision agricultural services concentrate on the perceived high value data, such as sensing, scanning or agronomic information, he points out. “But first we need the fundamentals of the digital farm set up correctly.
“We need our grower, farm and field information, our rows, which then turn into AB lines and our boundaries. From a viticulture point of view it’s more complex than broad-acre agriculture as we have variety boundaries, root stock boundaries and clone boundaries all of which can be different.
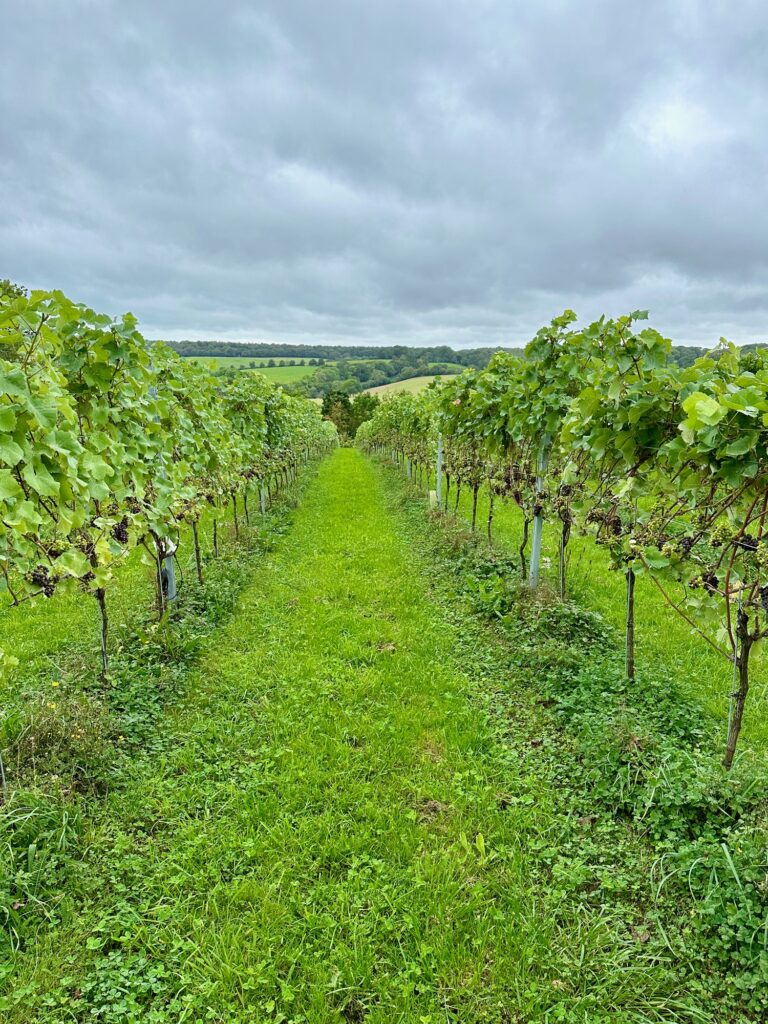
“If we don’t get this right, precision agriculture won’t work,” he says.
What is desperately needed is a simple mechanism for farmers to store their infrastructure data only, which would save huge amounts of time when setting up with service providers, such as robot or drone companies.
“People will say we have shape or ISO files to do that, but it is only part of the story. There’s lots of other pieces of data that are important – telegraph poles, for example, from a safety point of view, footpaths, where gates are and toilets for contractors. There are not many software providers from an ag point of view record that information as it has no agronomic value.”
Without it, each provider has to scan that information before starting which is a cost to somebody, as well as a time requirement. With it, a provider could deploy a robot in perhaps 15 minutes, he suggests.
“That means farmer engagement will be much higher because they’re seeing deployment and results much faster.”
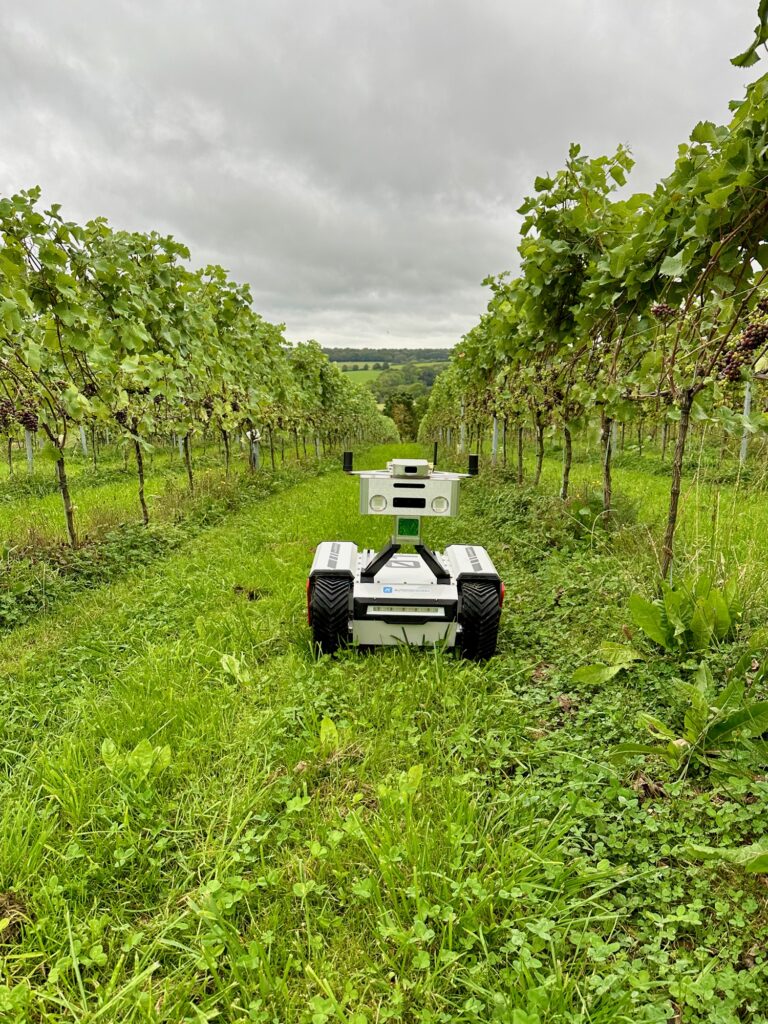
It will also manage risk when using robots or autonomy on farm. “In the Regulatory Horizons Council white paper, the Regulation for the Fourth Industrial Revolution, one of the concerns is manging risk on farm. For me it’s the farmer’s responsibility to help manage that risk, not the tech company. The tech company uses the tools they have to practically reduce that risk.
“But if the robot provider doesn’t know where a telegraph pole is, they always have to be guessing where an obstacle is. If I can digitally pinpoint where my telegraph poles are for example, you can put an exclusion zone around the pole and feed it to the navigation planning software.”
In the vineyard, an EU-based i4Trust project helped Ian map all his vines and posts, using an RTK surveying tool to create a hyper-local GPS grid of the vineyard.
“The attention to detail needed is much greater in this environment because of the consequences of getting it wrong. If you overlap a spray in a broadacre situation, it’s inconvenient and not good practice, but you just lose some crop. Get accuracy wrong here from a steering point of view and I wipe out a row of vines that’s thousands of pounds and at least three years’ production.”
The farm has been involved in a lot of projects (see box) since planting, but it’s logistics where Ian sees, at least initially, the greatest opportunity for technology. “From an immediacy of engagement in tech, logistics in and around a site has a faster win than agronomy.”
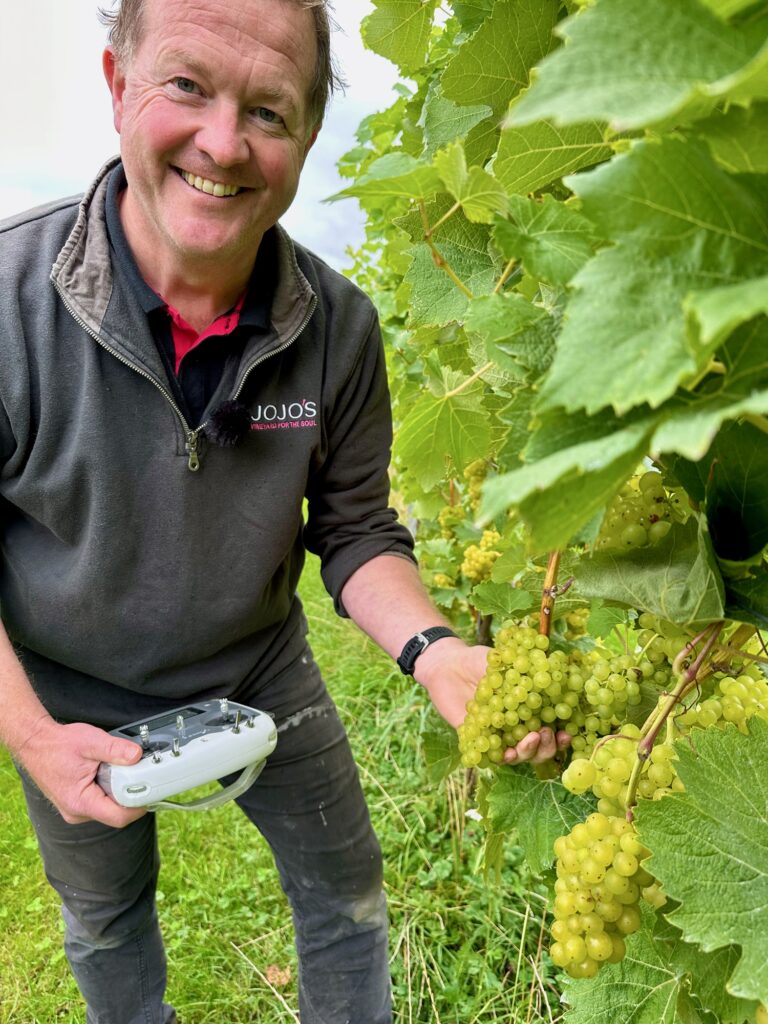
For example, removing prunings is, as Ian describes it, a nightmare job. These can be flailed and mulched, which is relatively quick, easy and inexpensive, but potentially leaves a disease source; they can baled and removed, or removed by gangs, he says.
Robotics could help with mowing grass between vines, for example. “FJ Dynamics have a self-propelled one which theoretically is able to do it, which we want to have a look at next year, while you could also pull a mower using a robot, such as the AgileX one we’ve got from Autodiscovery.”
Other brands such as Husqvarna and Luba are also options. “Automating or reducing the management time means I can do other more skilled jobs.”
Jobs such as carrying frost candles out, which protect vines against late frosts, are also suitable for transport using robots around the vineyard, particularly in wet weather when a tractor and trailer would cause more damage to the soil.
“It takes some of the grunt work out, and will be half the weight of a tractor and trailer.”
Robotic harvesting, while being developed for soft fruits and vegetables, is likely to be more difficult with grapes, he reckons. “It’s more difficult with bunches.”
Theoretically, depending on system and use, a camera could also be mounted on the robot to gather agronomic data at the same time and not cost anything extra, he suggests.
“In spring we want to count the number of buds on the shoot, and how many burst. From there, we can start to predict yield, or identify whether a vine is underperforming and needs to be managed differently, for example pruned back further so it pushes all its energy through a lower number of shoots.
“But you can only do that with good imagery and by assigning it to an individual vine.”
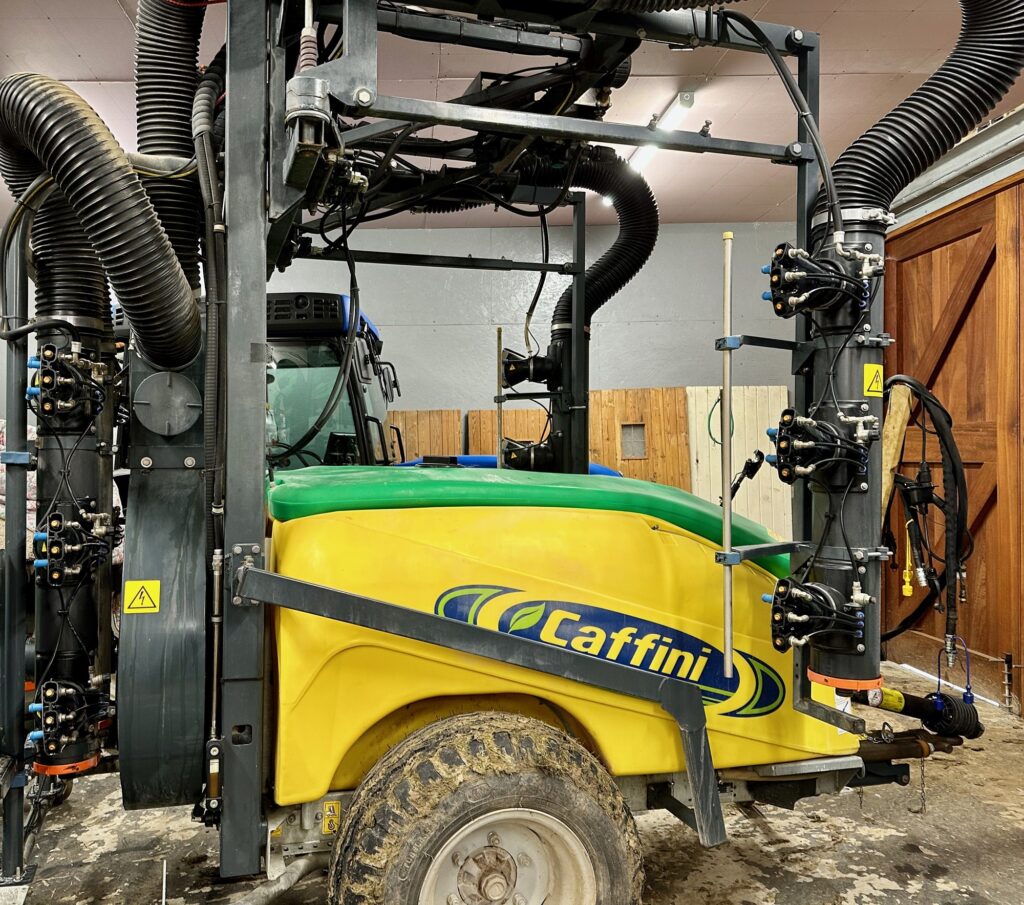
Generally, the issue with agronomic data currently is while it is relatively easy to acquire, acting upon it is much more difficult. “At the moment there aren’t a lot of tools that actually help me do something with the data.”
The main one is the sprayer but the risk-benefit is heavily skewed towards not taking chances because getting it wrong will have serious consequences, but he is looking at whether nutrition can be variably applied after realising this year that he had probably applied too much, increasing plant vigour at the expense of fruit production.
“Unfortunately not too many vine sprayers have controls to variably apply currently from a GPS point of view, so the first step I’m hoping to have is just automatic start and shut off at the start and end of rows. If we can do that, as we have in broadacre crops for 20 years, it will immediately save 10-15% of sprays,” he concludes.
Photocopier technology could pave way for underground insights
A soil project using a mini-rhizotron, which effectively is similar technology to a photocopier scanner, could begin to help unravel some of the mystery of what happens underground, Ian says.
“You basically put a plastic tube in the ground containing the mini-rhizotron into the ground at a 45 degree angle, which the plant roots grow around.
“The rhizotron scans the roots 360 degrees to make a flat image, and because it is in the same place all the time you can compare root growth and mycorrhizal fungi activity around the roots.
“We’re hopefully going to put 32 of these in the vineyard, and hopefully gain a real insight into what’s going on in the soil.”
It also potentially opens up the opportunity to look at various biological or biodynamic products in the soil to see the impact on microbial activity and root growth, or impact of various different cover crops, he says.
Technology being tested at JoJo’s vineyard
• Node and cordon counting and yield forecasting with Bitwise Greenview
• Yield mapping with eVineyard
• Canopy density scanning with TopCon
• Coverage mapping with Trimble
• Vine health with DeepPlanet
• Robots with Autodiscovery and Antobot
• Mowing and logistics with Agile X (Autodiscovery) and Logic equipment
• Steering with New Holland & Trimble
• Weather station with Davis Instruments & Ladybird technology
• Soil moisture and leaf wetness with Davis Instruments
• Soil scanning with SOYL
• Direct drilling and biostimulant application with the home-made S-Rex drill
• Mini rhizotron with Reading University
• Agri-Epi Centre smart farm.
The ups and downs of making English wine
The first batch of wine from JoJo’s was produced from grapes harvested in 2021. Unusually for a vineyard of this size, Ian decided to plant seven different varieties.
“Normally it’s just the three – Pinot Noir, Minot Meunier and Chardonnay – that are used to make traditional sparkling. But we went for a broader selection because we like still wine, and didn’t have the patience to wait an extra three years for the sparkling to come online.”
In addition, the farm grows Pinot Precocé, which is an early ripening red to blend to produce a sparkling rosé wine, a Pinot Blanc that can be both added to sparkling wine blends and used by itself, Bacchus and Seyval Blanc.
“Usually those two, Bacchus and Seyval Blanc, are used on their own to make still white wines, but our winemaker put them together and made something really quite interesting, as people say, in a good way.”
The blend even won a silver medal at the independent English Wine Award, he says. “The thing that’s amazed me was the wine was bottled in June 2022, and we opened the first bottle in August, and it was acidic. It was nice but acidic.
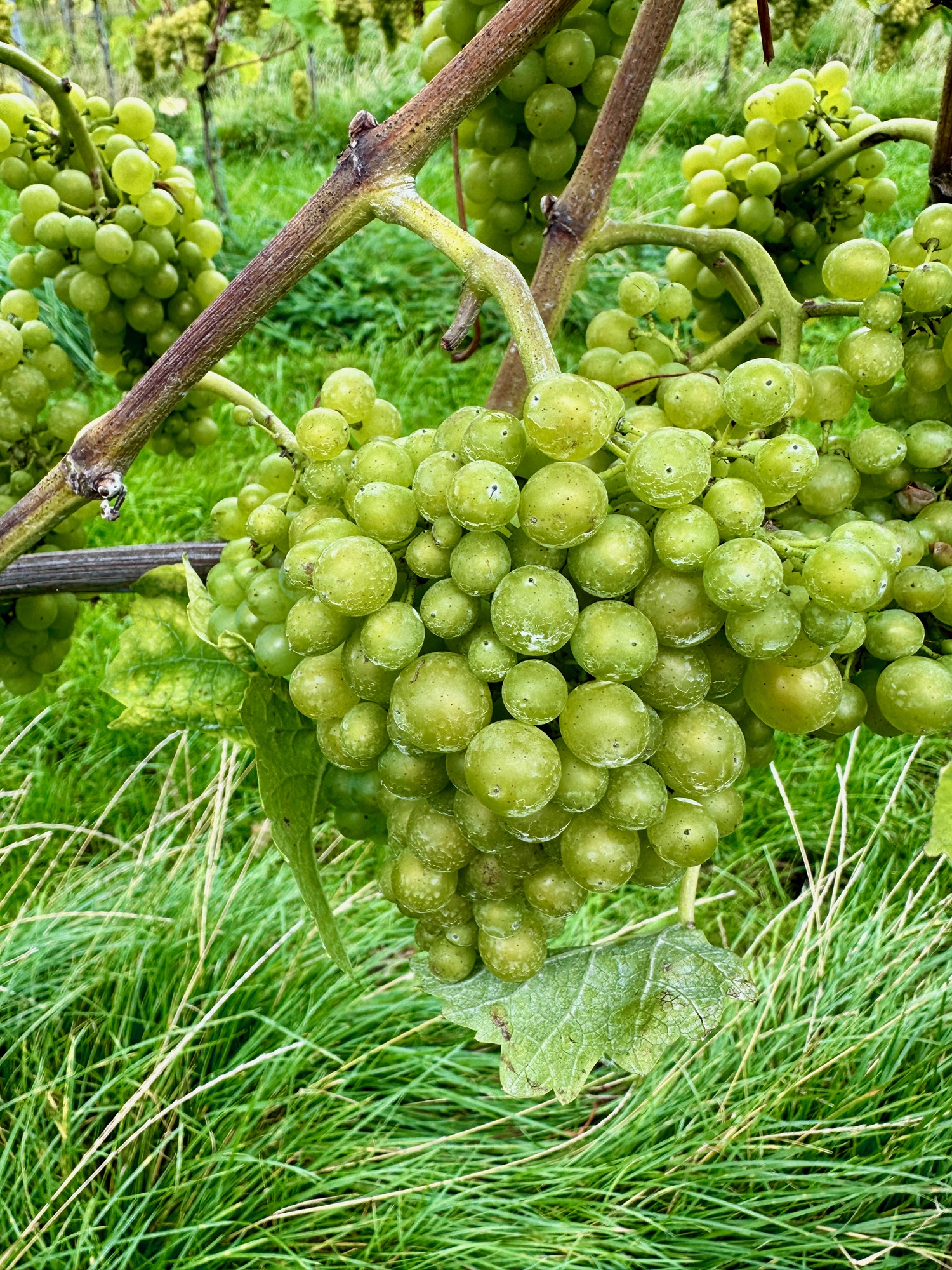
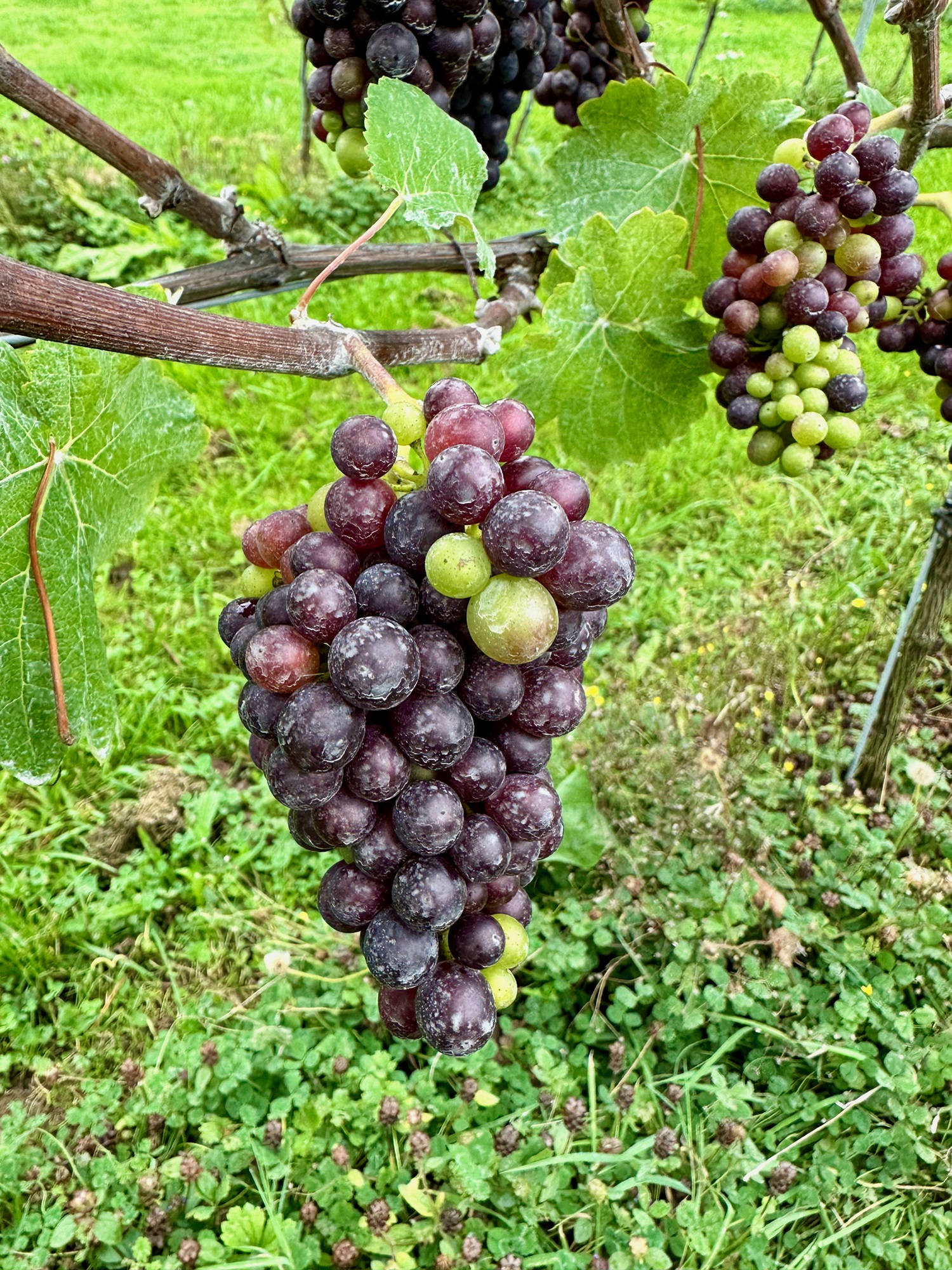
“So we had to keep drinking it every month to see if had changed because it was our own wine. In December it was still quite acidic, but get to February 2023 and oh my god it changed – it totally softened out and the acidity disappeared.”
That was down to something called bottle shock, he suspects. “They’ve been kept as two different varieties in four different vessels, some in a stainless steel tank, some in oak barrels. When they are blended together, you’ve almost got fighting inside the bottle between the different varieties and types and they have to learn to love each other,” he explains.
“Once they’re happy in each other’s space and become friends that’s when the softening out happens and how wine matures. We think this wine can probably stay in a bottle and improve for a couple of years.”
The still white wine retails at around £20/bottle, with a profit margin of around £4/bottle. Taxation at £6.23/bottle is the largest chunk of cost, while growing costs are around £2.50/bottle, and processing £6/bottle.
Around 1700 bottles of that blend were produced from harvest 2021, with a similar amount of sparkling white and sparkling rosé, which will be ready to drink at the beginning of 2025. Last year’s harvest produced similar bottle numbers, but the business is taking a different path with this year’s harvest.
“The one thing we’ve learned is the amount of cash needed in this business is ridiculous, so we’ve had to reassess the way we do things. It’s not until you’re in business do you realise how much cash is tied up that’s sitting in bottles as an asset.”
That means this harvest’s production will be limited to a sparkling white, with the remaining grapes sold to other producers to cover the cost of looking after the bottles for next two to three years.