I last attended the Agritechnica show in Hanover, Germany in 2019. It was my inaugural visit, and the sheer scale of it all was unlike any agricultural machinery show I had ever seen. Some of the major exhibitors boasted stands almost as large as entire UK agricultural shows. After three days of covering several miles walking a day, I realiszed I had only scratched the surface of the sprawling event, with countless machines and brands previously unknown to me.
The immense scale of Agritechnica serves as a stark reminder to a UK farmer like myself of our relatively small and perhaps inconspicuous role in global food production. While wandering through the exhibits, I found myself puzzled by a machine whose purpose I couldn’t fathom (it turned out to be a peanut harvester). It was a humbling experience that highlighted the vastness and complexity of global agriculture, revealing how much there is to learn.
During the 2019 show, one of the standout features for me was at the John Deere stand. They offered a glimpse of what the farm of the future might look like, featuring a “mission control” style operator seated at a “command hub,” surrounded by monitors displaying data from various sources. They were in live communication with drones and other conceptual autonomous machinery carrying out crop-related tasks. Other manufacturers presented similar concept machinery, mostly smaller in size, envisioning a future where numerous compact machines would work 24/7 to revolutionizse agriculture.
Agritechnica is a biennial event, and I vowed to return in 2021 to witness the progress in autonomous agriculture that I had eagerly anticipated. Unfortunately, the COVID-19 pandemic led to the cancellation of two shows, delaying my return by four years. I was eager to see how many of the concepts from my previous visit had become commercial realities and if the sharp-suited salesmen would be ready to take orders.
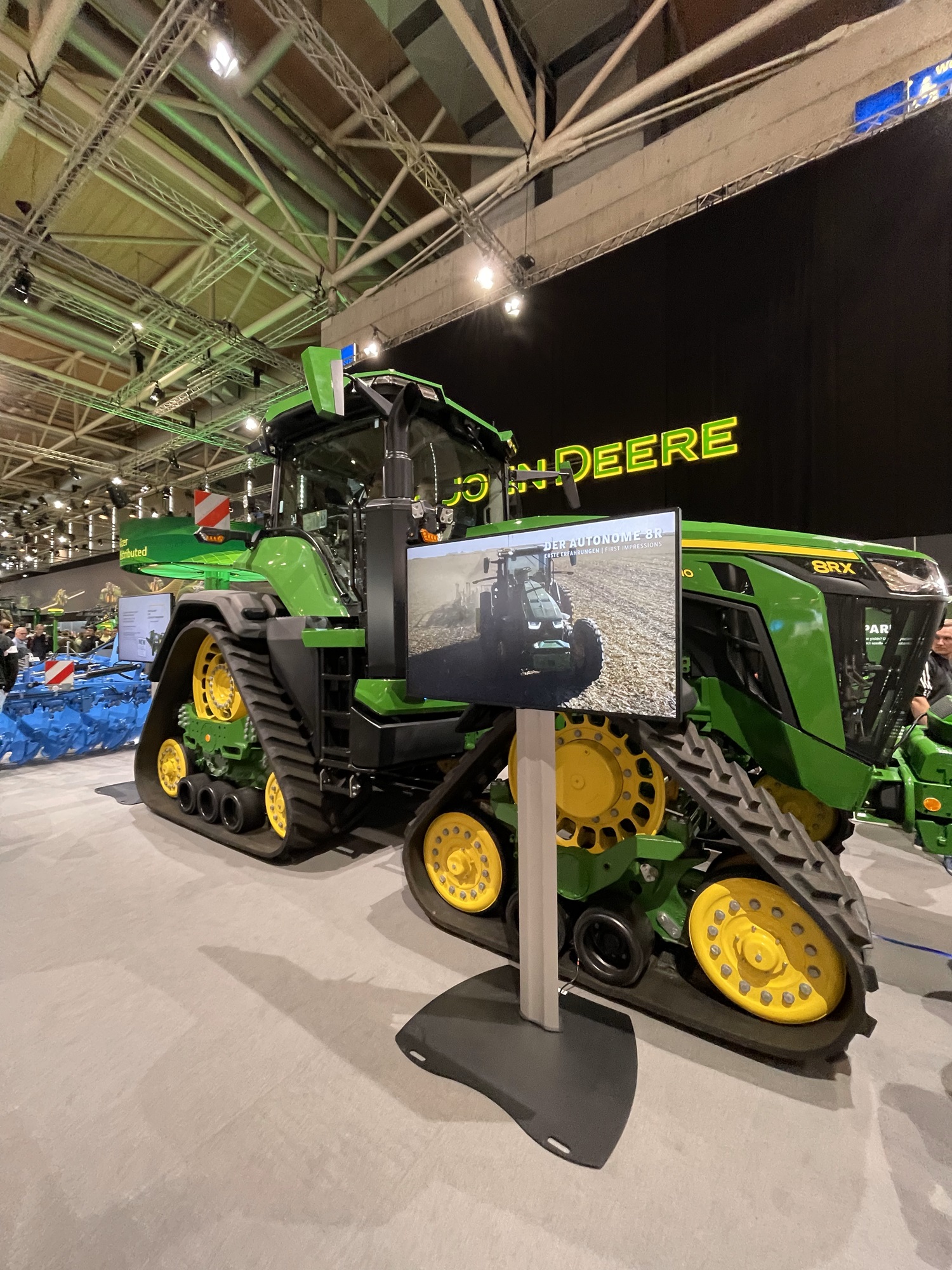
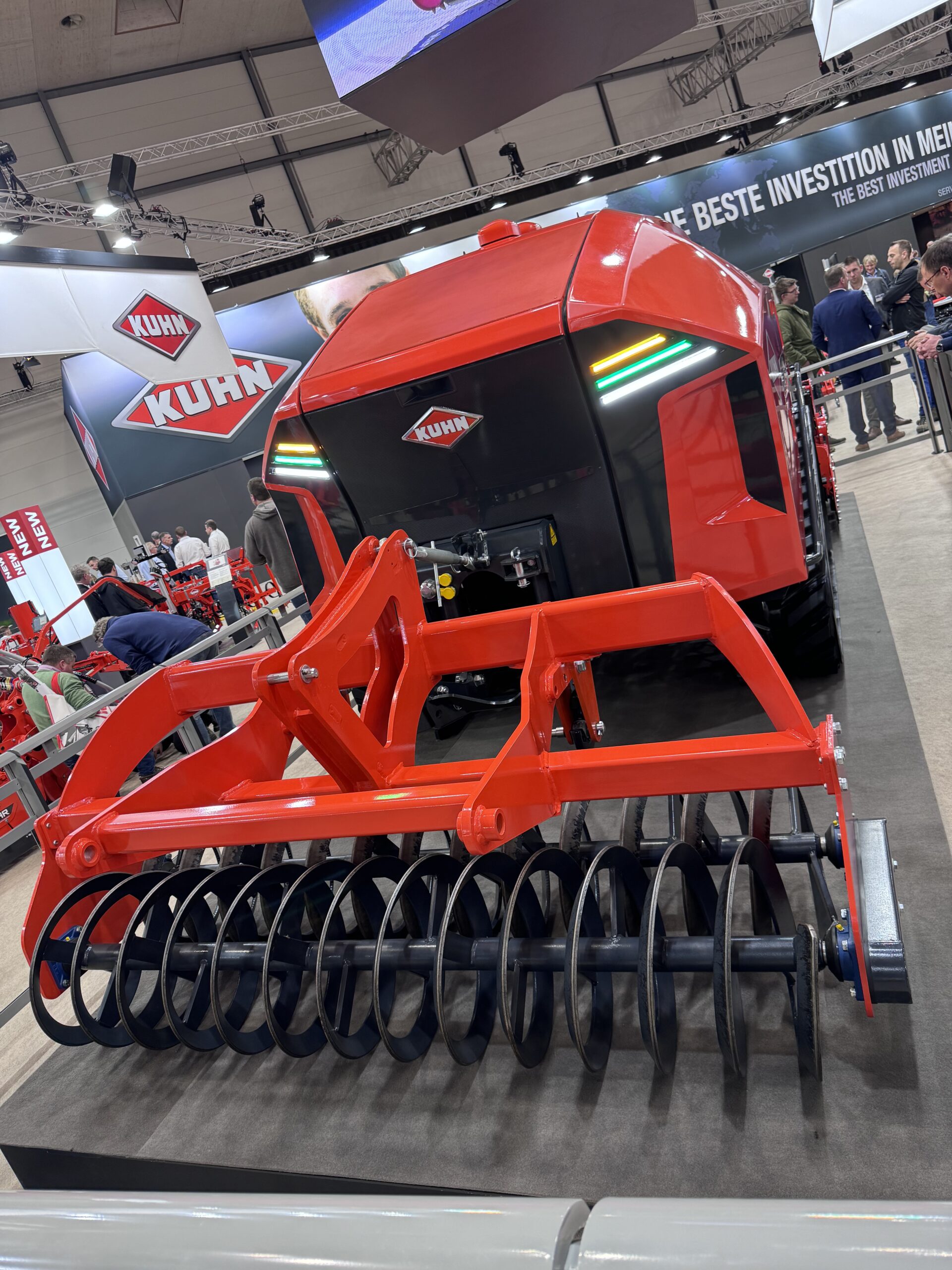
I scoured the halls of the major manufacturers in search of the production-ready versions of the drones and small robots showcased before, but they were nowhere to be found. However, automation was still very much present and, to my surprise, now commercially available. The big industry players seemed to have chosen to focus on fully automating existing equipment, starting with their largest machines. This evolution, while logical, began when the first basic autosteer systems were added to tractors, raising questions about the future job security of operators. As these systems evolved, incorporating features like auto-turn and headland management, the addition of fail-safe and anti-collision systems made operator-free full automation a commercial reality.
Despite the discreet sensors and cameras that can be found upon close inspection, these smart tractors still closely resembled their non-autonomous counterparts, with cabs designed to accommodate operators still in place. While these machines were smart enough to work in the fields without constant human oversight, we hadn’t reached the point where no human intervention was needed. Operators were still required to transport these tractors to the correct fields, assess field conditions, and “teach” the machine the desired routines across the field. Operators would receive alerts about blockages or obstructions via an app and would have to provide manual assistance in such cases, as well as handle tasks like refuelling and reloading seed and fertilizers. At best, the commercially available automation reduced the need for constant human attention but didn’t entirely replace operators.
So, if operators were still necessary, where did the savings and increased efficiency in agriculture come from? The answer lay in how many machines a single operator could now manage. I met a Canadian farmer who had operated nine of John Deere’s fully autonomous 8RX tractors in one season. A single operator had monitored and serviced these robotic machines, covering a vast area of cultivation work during the autumn. This efficiency significantly lowered the Canadian farmer’s production costs.
While I should have been as excited as I was during my 2019 Agritechnica visit when I saw the smaller “future” machinery that could easily integrate into my UK farm business, this larger-scale automation left me feeling disadvantaged. It seemed that I couldn’t compete profitably against such efficient imported competition.
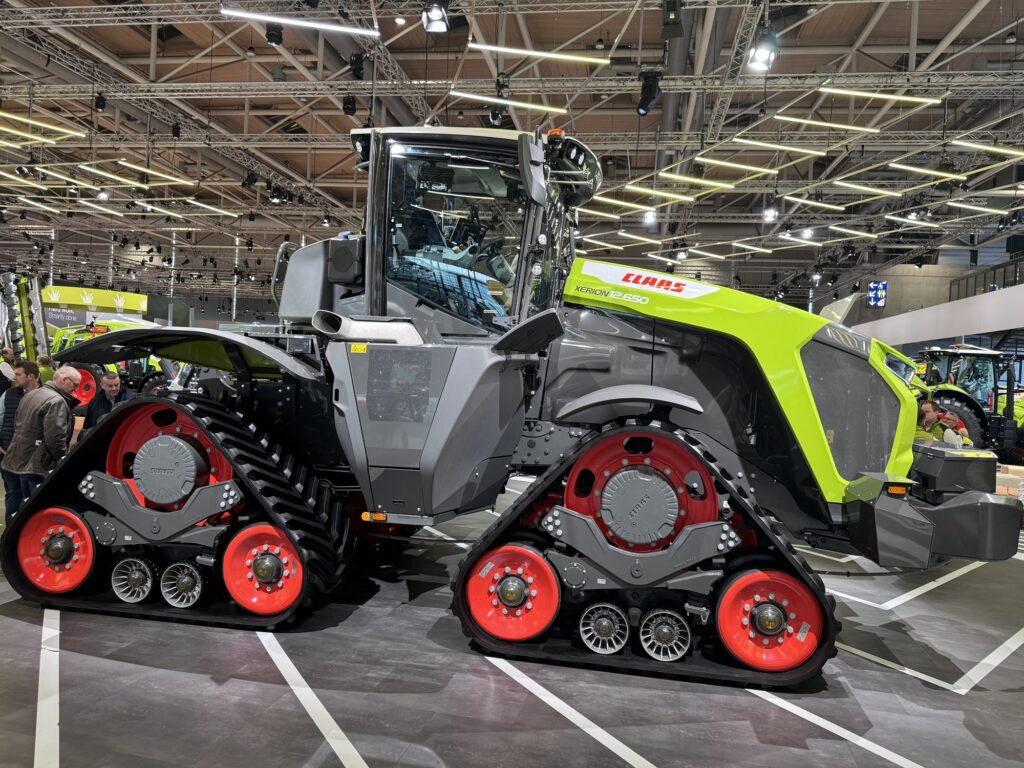
Despite being a larger-than-average UK arable farm, justifying the use of even a single tractor the size of an 8RX remained challenging. Our average field size and logistical challenges meant that the time spent on calibration, loading, and getting to the field for planting, fertilizsing, or spraying often equalled the time spent doing the actual work. There simply seemed to be no suitable application for a large fleet of such massive robotic tractors in the UK, as there was in other parts of the world.
Even if logistics and topography allowed for it, current UK legislation prohibits machinery from operating untended. Furthermore, even if it were legal, and despite assurances of robust safety mechanisms, one would still question their peace of mind while a 500hp, 30t robot operated near a motorway, housing estate, or school. It became evident to me that the UK was not the primary target market for this type of autonomy by manufacturers.
So, does that mean we’re at a disadvantage and exposed to import competition due to automation? Is our hope now pinned on the smaller robots initially showcased during my first Agritechnica visit? I inquired about them, but none of the major manufacturers were forthcoming with information. This led me to believe that perhaps, as these smaller robots approached commercial viability, secrecy surrounding intellectual property and patents might be the real reason for their conspicuous absence for this year’s event? Maybe, eventually, UK farmers will gain access to the commercial reality of automation available in other countries. Perhaps, we’ll find out at Agritechnica 2025.
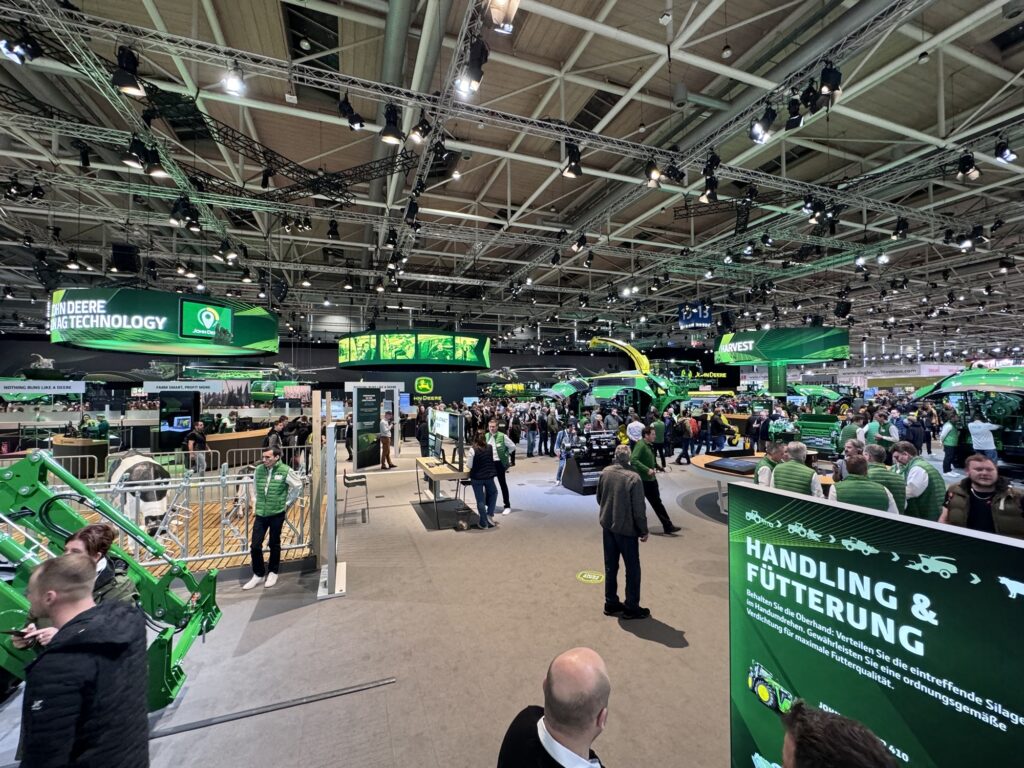