Trials test the tech – December 2023
On-farm trials have always played a key role in exploring new tech, and helped Simon Beddows develop a new use for John Deere’s Harvest Lab.
For the past30 years I have been a farm manager, firstly in Kent and latterly in South Oxfordshire. For 25 of those years, after successfully completing my BASIS and FACTS courses, I have undertaken all my own agronomy. An inquisitive mind and a desire to find out what works best on my farm led me to get involved with on-farm trials.
Life sometimes throws you a curved ball. In October I took on a new position with a John Deere dealer, Farol, as their in-house agronomist. My role will develop over time, but essentially I am there to help farmers and growers work with current and new technology, using data from machines to make agronomic decisions and improve productivity.
My journey into technology began in the early 2000’s, firstly to replace the unreliable foam blob marker on the sprayer with GPS generated A-B lines. Wanting more from my purchase, I added autosteer and began looking at variable rate fertiliser initially using SOYL to provide variable P and K maps based on soil test results. Farming very variable soil types it seemed a good idea to try adjusting the rate of nitrogen according to crop growth. To prove it worked I set up three years’ worth of trials comparing the technique with standard blanket applications. So began my introduction into creating my own farm trials. In the last few years I have worked with major manufacturers and universities covering a diverse range of topics.
It was my link with Reading University on a three year project looking at the probability of profitability that bought me to John Deere and their development of HarvestLab on combines. The project was investigating which factors, during the crop’s growth cycle, had the greatest influence on final yield. Using this knowledge, growers could attempt to influence crop growth before harvest, or tailor inputs according to predicted yield. Part of the analysis was taking hand samples of the crop at pre-determined GPS marked points just prior to harvest. Protein content was the main grain quality aspect that was of interest, because of its link to nitrogen fertiliser. Finding students to help the research staff was always a challenge, especially at short notice and I had heard that John Deere were looking to develop their Near Infrared sensor, already proven on forage harvesters, to work on combines.
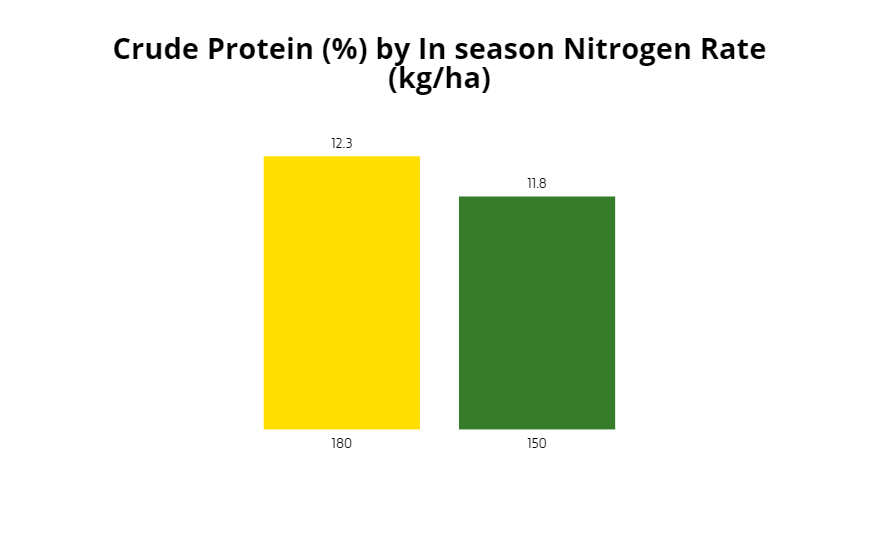
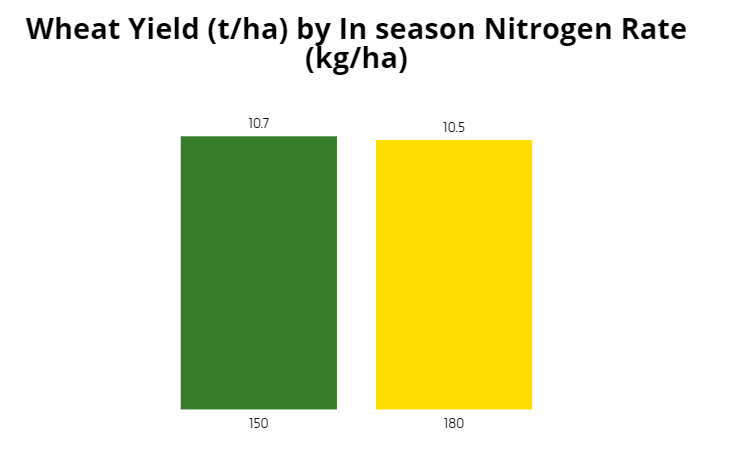
HarvestLab sits on the clean grain elevator and uses an auger to take grain continuously past the sensor. 4000 readings are taken every second. My local dealer, Farol, put me in contact with John Deere who were keen to get a UK grower on board. The first year was spent getting to grips with the system and confirming the calibration curves by collecting samples and sending them for analysis. In my various meetings with John Deere, they were keen to emphasize the value of being able to segregate the grain according to protein content going into the store. At our first harvest wash-up meeting, as we sat looking at the maps generated by the combine, I pointed out that this was a powerful tool for making agronomy decisions particularly around nitrogen fertiliser.
I have always liked John Deere as a manufacturer because they are happy to listen to the customers and look for solutions to the problems they have identified. Still, I knew I had to show them something concrete, so for harvest 2022 I set up a fertiliser trial.
The price per tonne of nitrogen had skyrocketed in the spring and £700/t looked good, so what better time to see how low we could go. The field I chose was milling wheat following a crop of maize and farmyard manure. Two 30m tramlines were selected for each treatment to get over the overlap problem with a spinning disc spreader. The rates were totals of 150kgs/ha and 180kgs/ha of nitrogen. Following on from harvest I had both protein and yield data from the two plots. Every load that went back to the farm passed over a weighbridge, so combine yield data could be checked post-harvest. Grain samples were collected for the trial and sent off for analysis as before, to check on protein.
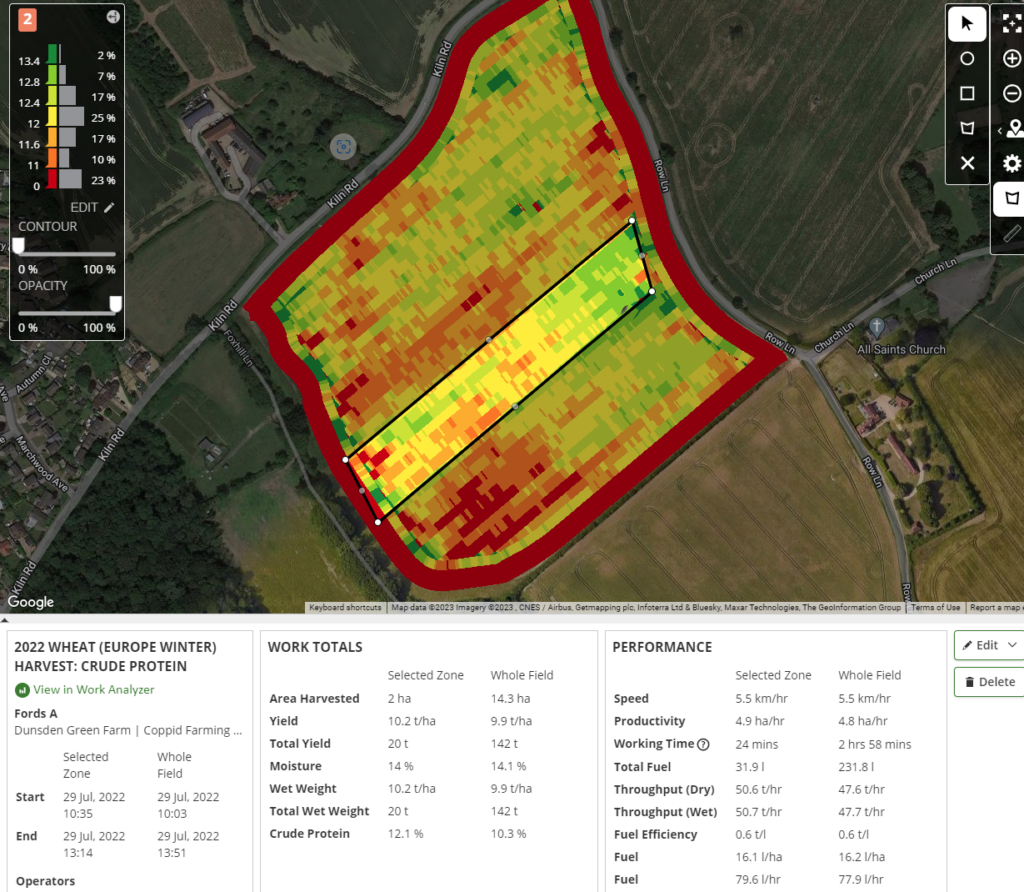
I used John Deere’s Operation Center for machine integration, data collection, work planning and analysis, which allowed me to view the differences in yield and protein maps side by side. The results showed yield to be statistically the same in each plot at just over 10.5t/ha. However, the protein content was 0.5% lower in the 150kgs/ha of nitrogen plot, much as expected, with grain testing showing that both treatments had been above the 11% protein content necessary to reach maximum yield, all other factors being met. Now I had got John Deere’s attention and they could see the added value of HarvestLab as an agronomy tool. They now have a team of agronomists working for them in their technology department, so expect more exciting developments to come.
As part of my new role, I now get access to Agronomy Analyzer. It is a dealer only tool developed to allow much more detailed analysis of farmers and growers own trials. I have run some of my trials through it including this nitrogen trial.
 Hopefully I can work with more of our customers in the future to produce reports for them that can be accessed through Operation Center. With a loss of support systems and more extreme weather events, it becomes even more important that farmers and growers can back up decisions with accurate and relevant data.

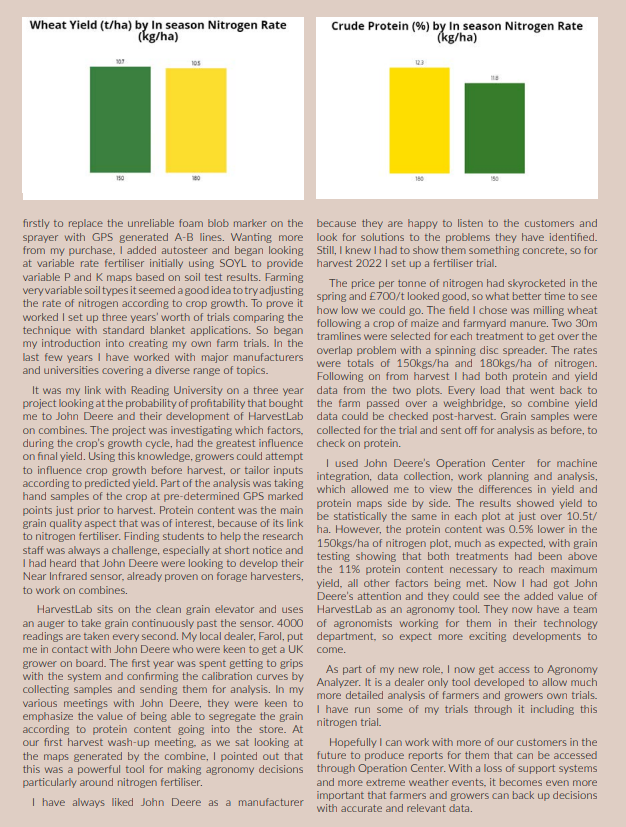