Concentrated light technology has passed proof of concept as a form of weed control and is being developed through field trials. Tech Farmer sees the Earth Rover ‘CLAWS’ in action.
By Tom Allen-Stevens
CLAWS moves forward, a little more than 0.5m, and stops. There’s a flash from under the hood which lights up the young crop of lettuce below. This is quickly followed by dozens of tiny spots of blue light and there’s a rasping, crackling sound.
You realise that the spots of light are focused on the weed seedlings around the lettuces, and each one gives up a tiny wisp of smoke as it’s momentarily lit. Then there’s the rather satisfying smell of weeds being fried to death.
“We call it concentrated light technology – it works in much the same way as sunlight being focused by a magnifying glass,” explains Earth Rover CEO James Miller from behind a pair of red safety specs. “You can do the same job with lasers, but this is far more effective, efficient and safer.
“At a distance of more than 2m, you don’t really need the safety specs – these are a precaution because the operating regulations haven’t caught up with our technology yet. If we were using direct lasers, there’d be a risk of the light bouncing off a shiny surface and causing injury.”
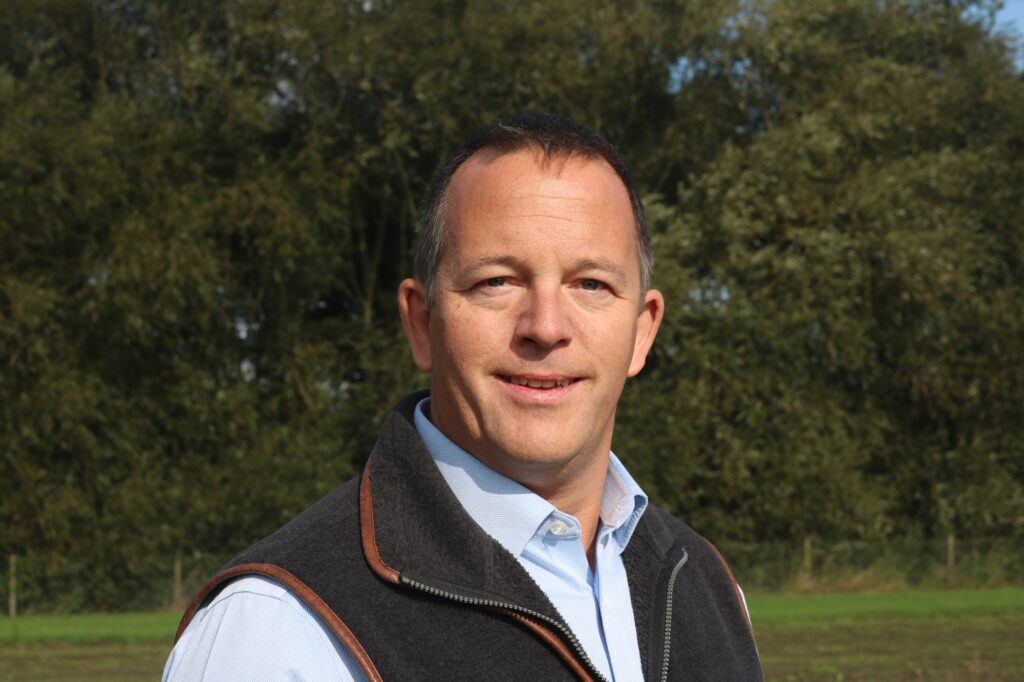
Developed as the LightWeeder, it’s claimed to be the world’s first eye-safe, herbicide-free, carbon neutral, commercially viable weeding system. It uses semiconductor LEDs to generate light that is then concentrated precisely onto the meristem of a weed seedling – the most sensitive area of the plant and the point at which it emerges from the soil.
By now the CLAWS rover has finished picking out the weeds and is moving on to the next section – flash, crackle, pop. While it takes a fraction of a second for each weed to be fried, the length of time it pauses over an area of soil – about 1m² – varies, depending on the weed burden.
This machine tackles up to 60 weeds in a second with its three modules of concentrated light units. These are shrouded beneath the branded hood – the heart of the patent-pending technology – and James wasn’t about to let an inquisitive journo make a closer inspection. There’s a claimed work rate of 1.5ha in an 8hr day.
“Once commercialised and fully autonomous, one 2m-wide machine will look after about 4ha in a day, depending on weed burden, passing continually over taking out the weeds as they emerge,” continues James. “There are optional solar panels, which would keep it charged up for a full day, and the battery alone would power it for about half a day from a full charge.”
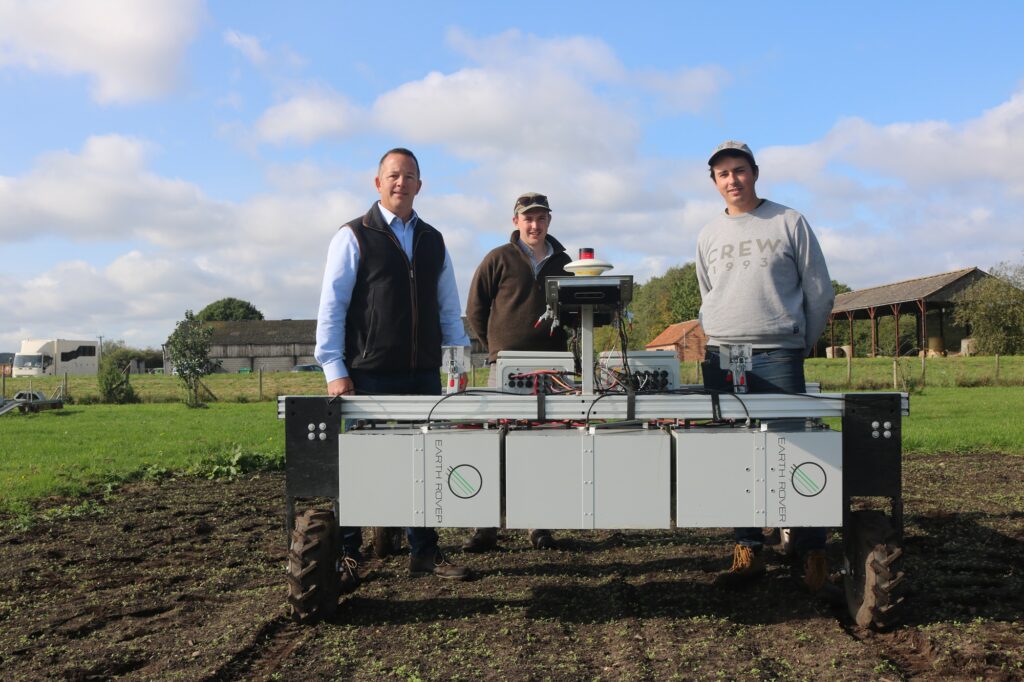
Frying the weeds is just one aspect of the job done by CLAWS, which stands for Concentrated Light Autonomous Weeding and Scouting. On the front and under the hood are eight built-in cameras that detect the exact location of the crop and weed seedlings. This results in a complete data map of the crop after planting, showing the plant’s exact location, size, and any early signs of disease.
The meristem detection technology allows the robot to identify the growing point of the weed, which is the most sensitive area of the plant, and apply the precise amount of light needed to eliminate it. The CLAWS makes use of edge AI processing and can create a 3D image of the crop bed. “You can have the rover scout for the crop, the weeds or both, and have the data available on a laptop, tablet or phone for decision making in real time” he adds.
The 3D image is needed so the blue light can then be focused on exactly the right place to fry the weed. “Range of depth is critical, and currently this is something of a limitation. If the target weed sits on a ridge of soil in the bed, that can put it out of range of this prototype,” notes James.
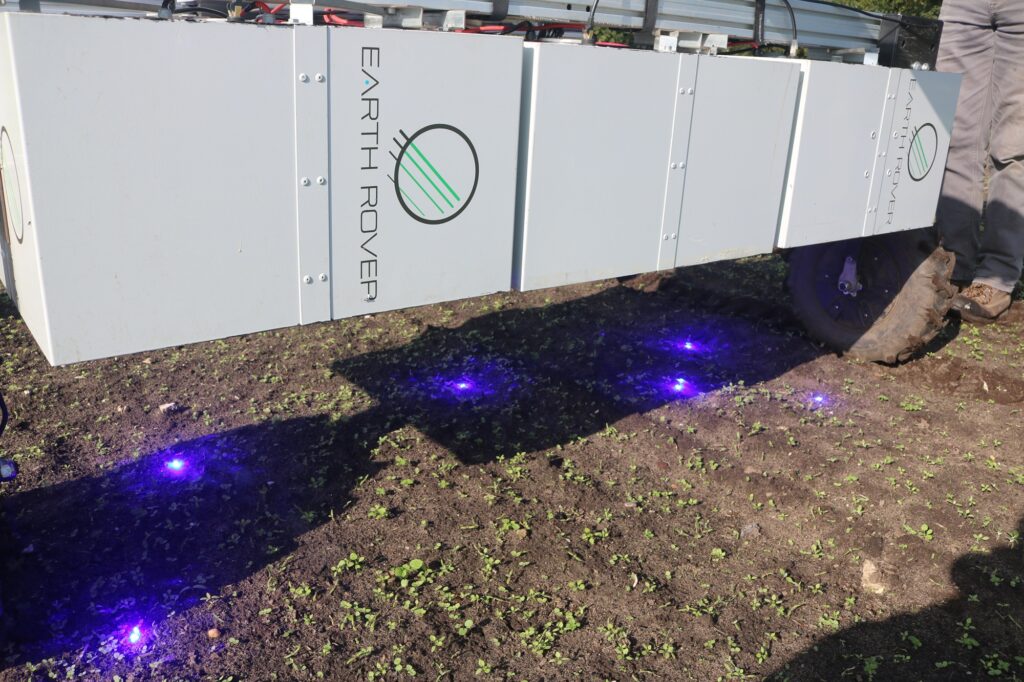
Weed identification is continually improving – every pass allows further training of the algorithms. The final limitation is size of weed. “It can control relatively large weeds, but the power consumption can be prohibitive. So it’s most efficient and effective when the weeds are at seedling stage with the meristem exposed.”
But it is a true kill – independent trials have found the CLAWS technology is as effective as herbicides at controlling both monocotyledon and dicotyledon weeds, and concentrated light offers an improvement over chemistry where there is an element of herbicide resistance. This makes the overall effectiveness of a single pass of the Earth Rover about 60% currently, but James sees no reason why this shouldn’t improve to close to 100% as the machine trains itself and the range of depth improves.
“So far, the team has focused on getting the clever bit right. The improvements will come from refining the simple bits,” he says.

The organic challenge
The farming brain and origin of the business concept behind Earth Rover belong to James Brown, director of Pollybell Farms. He manages the 2000ha Lapwing Estate, an all-organic mixed farming business based at Little Carr Farm near Gainsborough, Lincs.
800ha of arable include 200ha of field vegetables, bringing in broccoli, cauliflower, cabbages and leeks, with 400ha of organic wheat and 200ha of barley. These rotate around fertility-building leys that support sheep and dairy youngstock enterprises. “We’ve moved away from a farm rotation to a field rotation, where the cropping is decided by market demand and field requirement,” notes James Brown.
But it’s the soil type that probably has most to do with how the farming system has evolved. This is Fenland, lying over sand and clay, no more than 1m above or below sea level. “Organic matter is consistently above 30%. We’re farming in compost, which means the soil is incredibly fertile and has a very high weed burden.”
The decision to go organic was made in 1997. This may have seemed odd for a business that at the time had its own agchem supply arm, but you get the feeling James Brown enjoys the bigger challenges. “1000 acres of organic are a lot harder to manage than 1000 acres of conventional agriculture. There’s no get-out-of-jail-free card, and a zero yield is perfectly possible.”
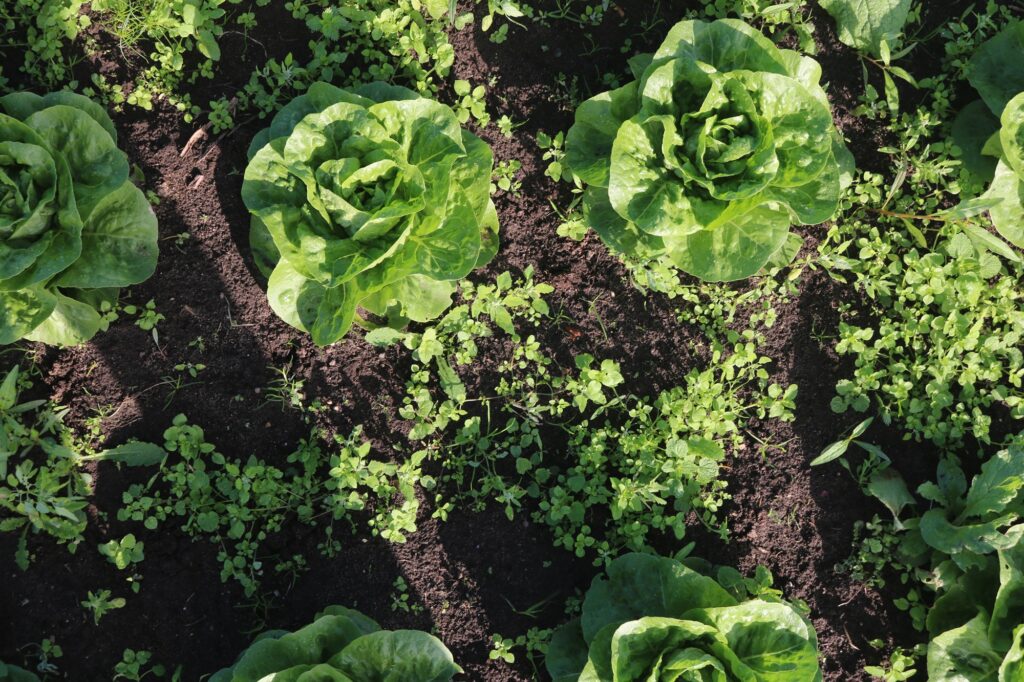
Weed control on a Fenland organic farm soon became the biggest headache, although James points out that the high organic matter tends to erode efficacy of herbicides. “Once you knock out chemistry, the only option is mechanical and that has severe limitations.”
Ploughing is used as a rotational tool, usually brought in before the vegetable crop as this is where the yield suffers most from weed competition. “We also use mechanical hoes, and have used a precision-guided model, but there are two fundamental problems with these: firstly, when conditions are wet you can’t operate it, but that’s when most weeds emerge.
“We’ve also found the action of the hoe interferes with the roots of the crop. The weeds close to the crop plants are the most important ones to control as these are competing hardest. But yield and quality take a hit from the damage to the roots.
“I came to the conclusion that the best solution for weed control didn’t exist, which is why I founded Earth Rover,” says James.
The concept behind CLAWS came about through a chance meeting he had about six years ago with Luke Robinson, a scientist with an interest in AI and robotics. “It was Luke who pointed out that lasers are power-hungry and dangerous, but he had previous experience with concentrated light technology.”
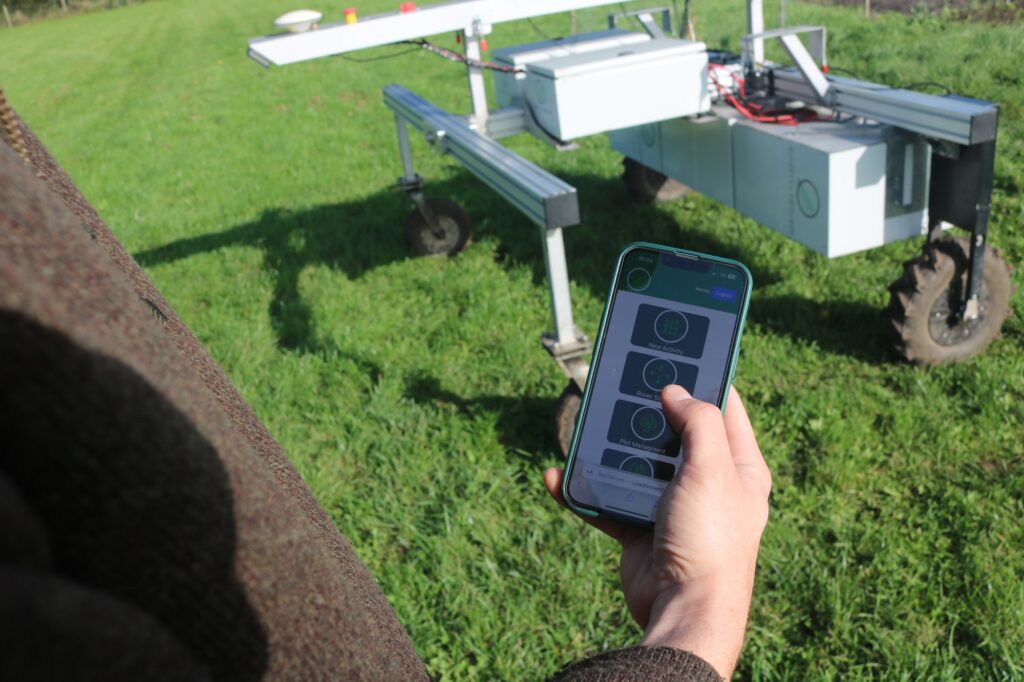
James provided the initial funding – around £200,000 – to develop the proof of concept for Earth Rover. “It was the time when the Mars Rover was very much in the news, which did provide the inspiration for some of the design, as well as the name.”
In 2021, Earth Rover and Pollybell Farms teamed up with Agri EPI and NIAB in a £750,000, 18-month industrial research project, funded by Defra under its Transforming Food Production programme, delivered by Innovate UK. “This took the idea from concept to prototype. We also carried out the efficacy trials of the technology with NIAB and developed what the service would actually look like – we carried out interviews with other farmers.
The venture now has the backing of Mercia Asset management, and has developed the concept into two prototype units. There’s a team of eight, including Tomàs Pieras, Chief Technology Officer, who has developed the robotics and AI weed detection. “Earth Rover also has an R&D facility in Spain where we have been further developing CLAWS.”
The plan is to build the fleet up to a total of five units and run trials on a series of Pioneer farms in 2024. “We put a call out earlier this year, and the places are now all filled, but we’re always looking for more triallist farmers. The aim is for 2025 to be our first commercial season. So we’ll be selling the unit with a service and maintenance package,” explains James.
“The way I see it, up to this point farmers have just had two options for weed control – chemical and mechanical. We’ve now added a third – thermal.”
What is Concentrated Light Technology?
Ancient civilisations are known to have focused the power of the sun through concave reflection or refracted through glass to light fires for cooking and heating. The technology has seen considerable advances in recent years with the increase in renewable, solar power.
The essence of Concentrated Solar Power (CSP) lies in capturing and focusing sunlight to either generate electricity or to enhance the performance of solar arrays. Unlike traditional solar photovoltaic (PV) systems that convert sunlight directly into electricity, CSP focuses sunlight onto a receiver, which then converts the concentrated solar energy into heat. This heat can be used to generate electricity through a steam turbine or stored for later use in thermal energy storage systems.
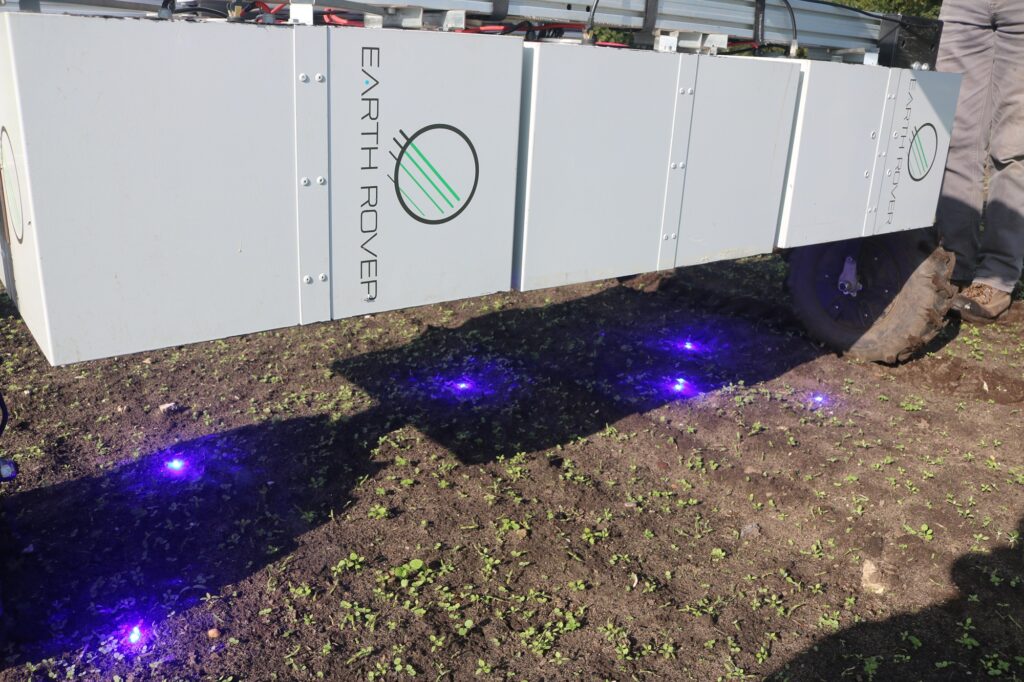
A similar effect is achieved by focusing light-emitting diodes (LED) into a small focal spot. Applications include medicine, cutting and engraving. LEDs inherently emit light under defined angles of radiation, minimizing divergence losses compared to conventional lighting systems that radiate light all around. This means the light can be intensely concentrated producing very high temperatures at the focal point.
The lure of lasers
US startup Carbon Robotics, based in Seattle, has introduced its LaserWeeder implement that fits to a three-point hitch. The 6m wide unit features 30 industrial carbon dioxide lasers, more than three times the number on its original self-driving autonomous LaserWeeder. This gives it a claimed output of about 0.8ha per hour.
The trailed unit draws its power from the tractor, identifies weeds and targets them for elimination. Lasers use thermal energy to destroy the meristem of the weed without damaging nearby crops or disturbing the soil.
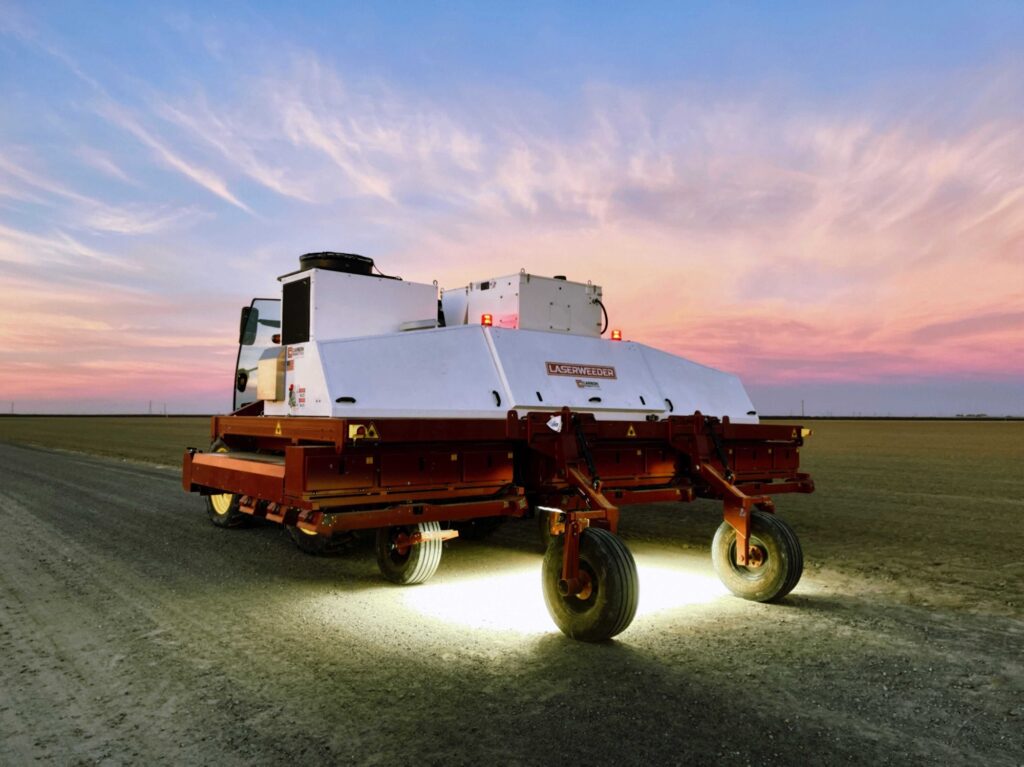
Carbon Robotics says growers who use the implements are seeing up to 80% savings in weed management costs, with a break-even period of 2-3 years. It can eliminate up to 5000 weeds per minute, identifying 99% of weeds. The LaserWeeder can operate on over 40 crops and create and deploy new deep-learning crop models within 24 to 48 hours.
The company raised $30M in series C funding earlier this year, and has units active across 17 US states and three Canadian provinces.

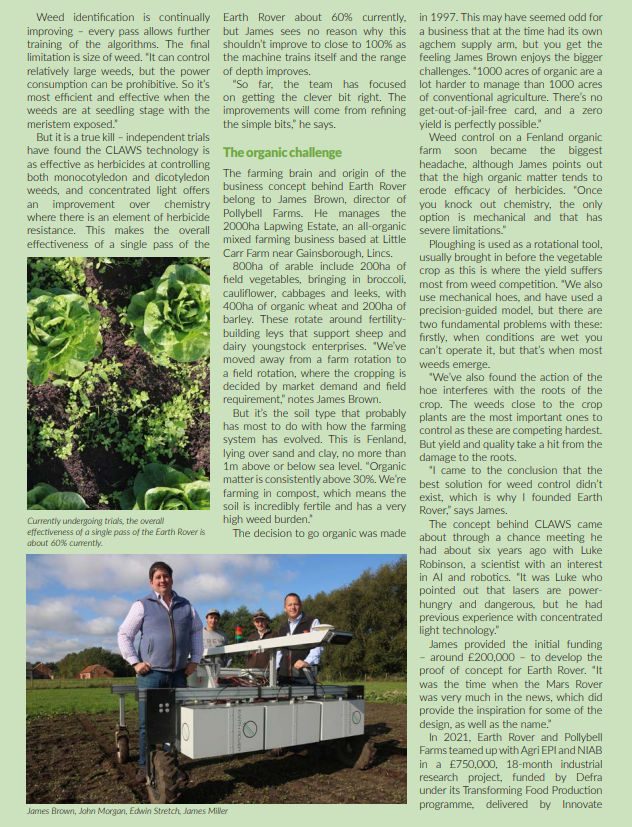
