The World FIRA event near Toulouse, France, brought together agricultural robotic enthusiasts from across the globe. Tech Farmer was there to spot the bots with promising potential.
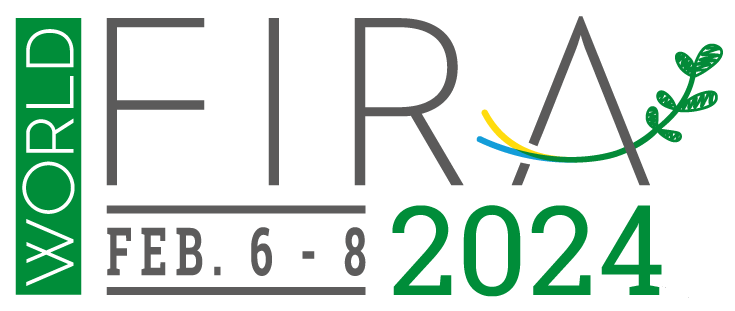
With 35 autonomous solutions on display and demonstrated, more than 70 exhibitors and 2500 visitors, World FIRA (Forum for Agricultural Robotics) is gradually establishing its reputation as the world’s largest exhibition of agricultural robots.
The three-day event, that took place at the beginning of February was its eighth edition (the second from the field), bringing farmers, scientists, investors, journalists, and robotics enthusiasts from over 50 countries to the Agrobiopôle near Toulouse, France. Organised by the Global Organisation For Agricultural Robotics (GOFAR), it runs in conjunction with FIRA USA, with the next event taking place on October 22-24, 2024, in Sacramento, California.
The fifth FIRA Scientific Workshop explored four of the challenges facing robotics, and in particular how it helps farmers meet agroecological targets. FIRA’s first Hackathon tested the latest algorithms in a head-to-head problem-solving exercise to develop solutions for improving robotics safety. And start-ups got the opportunity to pitch to World FIRA investors.
At the heart of the show were demonstrations of autonomous robots, specifically designed for crops. There was a marked emphasis on kit for the European market, with plenty of innovations for vineyards, orchards and specialist crops. Row-crop growers had to search a little harder among the exhibits for credible autonomous successors to the tractor and implement. Nevertheless, a few solutions stood out in the triticale, garlic, bean and radish demonstration plots.
A star attraction was the Robotti by Danish manufacturer Agrointelli. It received the gold medal, voted by participants as Best World FIRA Robot. The new Robotti LR (Long Range) was on show, with the older 150D due to be phased out in 2024.
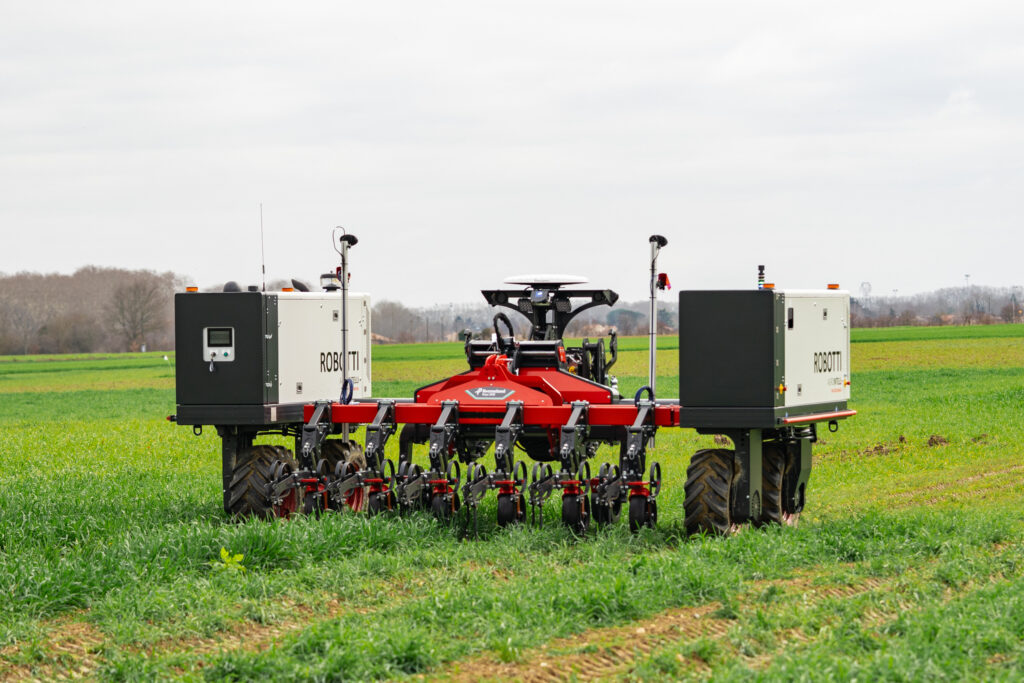
The key difference with the LR is that it has just one 72hp diesel engine, whereas the 150D has a gas-guggling pair. One engine has now been switched out for a larger 300-litre diesel tank, which means the LR can run non-stop for up to 60 hrs before refuelling.
The Robotti boasts a high on-wheel torque, improved hydraulics and a lifting capacity of 1.2t on its Cat 2 linkage. You can opt to have a PTO installed which gives you 540rpm at 14kW/18hp.
The 3t modular design allows you to vary working width from 1.5-3.3m. Typical tasks are seeding, weeding, ridging and spraying, with some of the K.U.L.T. kit ideal for the jobs, propelled autonomously at speeds up to 8km/h. The wider width and speed has come in as a result of the Bosch RexRooth-based hydraulic propulsion system, introduced with the LR in 2022.
At FIRA, Agrointelli was keen to show off its latest advance: Control Tower – software designed to provide farmers with greater control of the Robotti’s autonomous mechanism.
The Robotti has already been driving either in row-by-row scenario, grouped in several rows or in an optimised route-driving pattern. New patterns include “Coiled” as well as “Back and Forth”, claimed to add stability, reduce tilting and side slip while driving, especially when working in vegetables grown in raised beds.
When using this pattern, both sides of the Robotti drive in tracks in the same state, so either both sides are worked or left out. Load-dependent planning allows you to optimise operations based on the capacity of the implement. It means you can specify the maximum area or the number of rows to be worked out, aligning with the available resources.
Also new is Subfield Management, allowing you to sub-divide fields with unconventional shapes and designs. Each subfield is given its own AB line, which means the autonomous driving aligns with field terrain conditions.
“Robotti Control Tower makes constant upgrades and improvements automatically while the machine is online,” notes Ole Green, Agrointelli founder and CEO. “They’re also available for most of our older Robotti versions.”
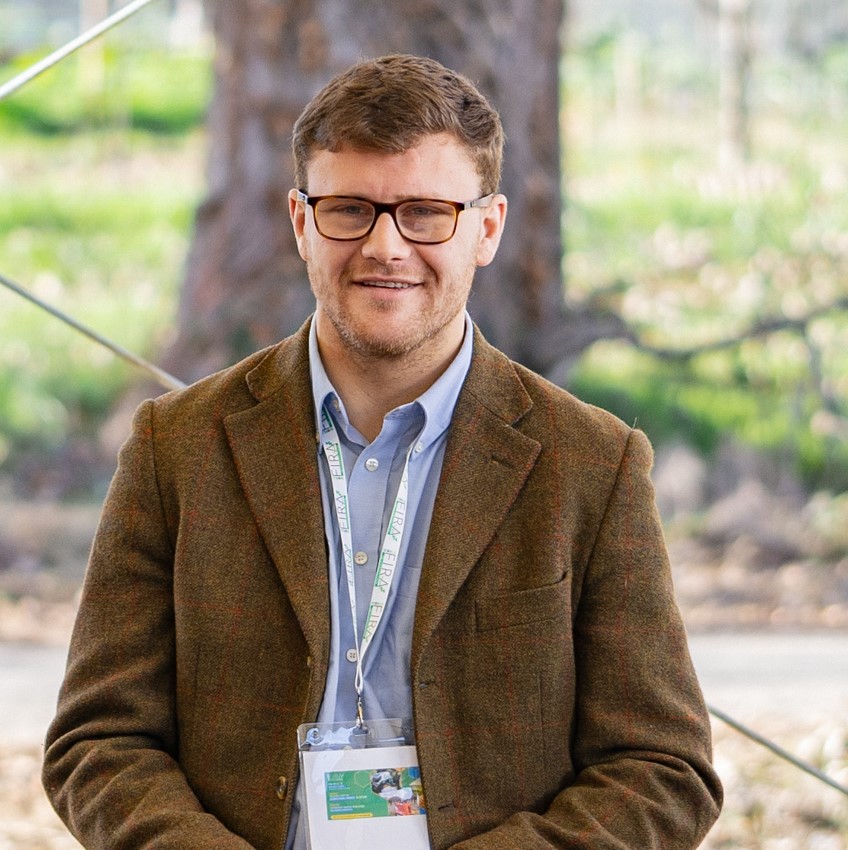
UK farmers can now take advantage of the new precision farming actions available through the Sustainable Farming Incentive (SFI) points out Tom Beach of Autonomous Agri Solutions, UK agents for Agrointelli. “It qualifies for the £150/ha payment for robotic mechanical weeding,” he says.
The cost of owning a Robotti has now been made easier through the Robot as a Service option, which gives you the use of a Robotti with logistics support and full software back-up for £35,000 per year. “The cost in a 2023 pilot in sugar beet worked out at £70/ha per pass over 150ha for drilling and all the weeding – three to four passes,” adds Tom. The robot’s suitable for sugar beet and field vegetables, but “not quite ready” for cereals.
From the Agrobiopôle you can just about see the headquarters of Naïo Technologies, which is where FIRA began. Naïo is the natural host of the event, and the full family of its robots were on display to greet participants.
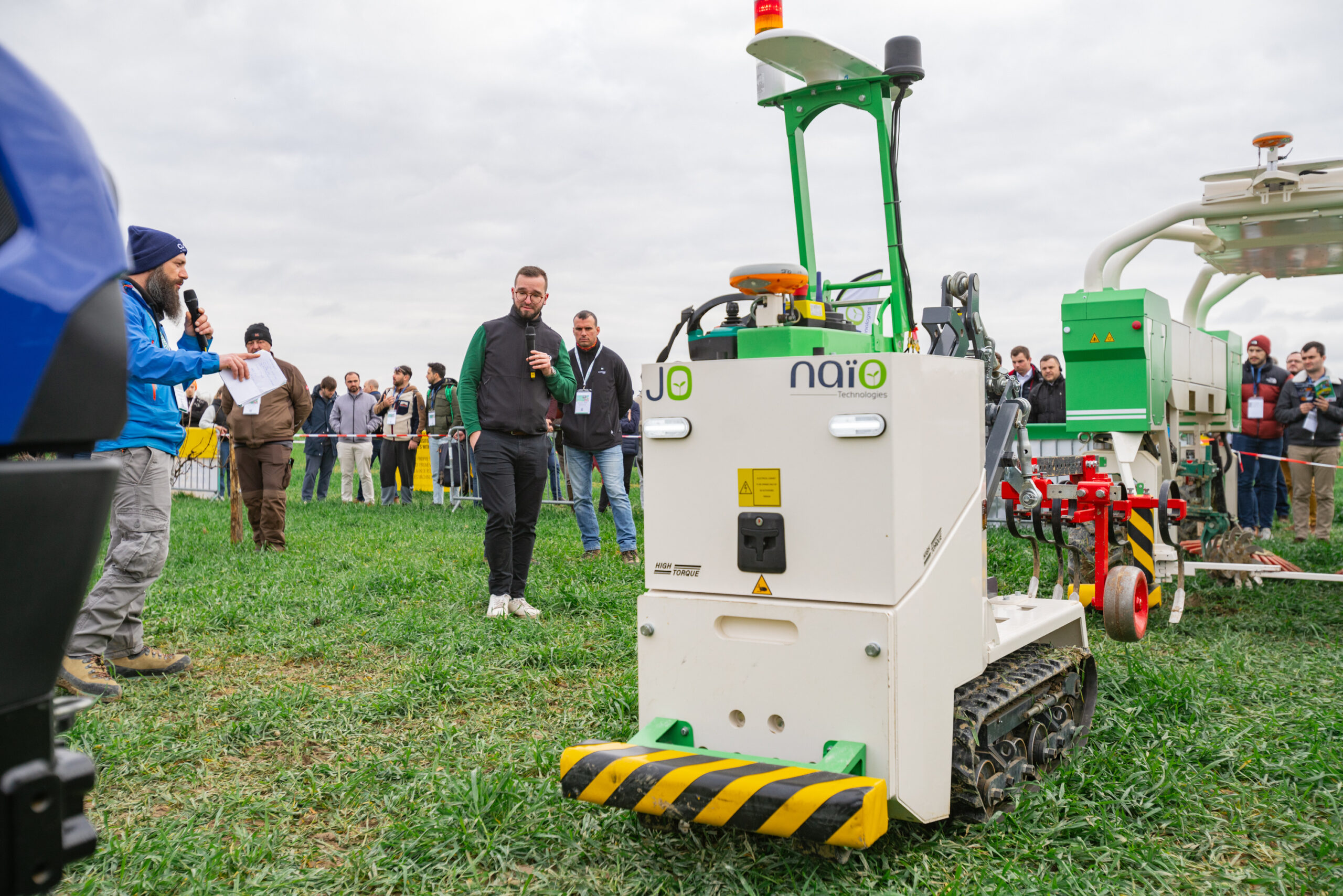
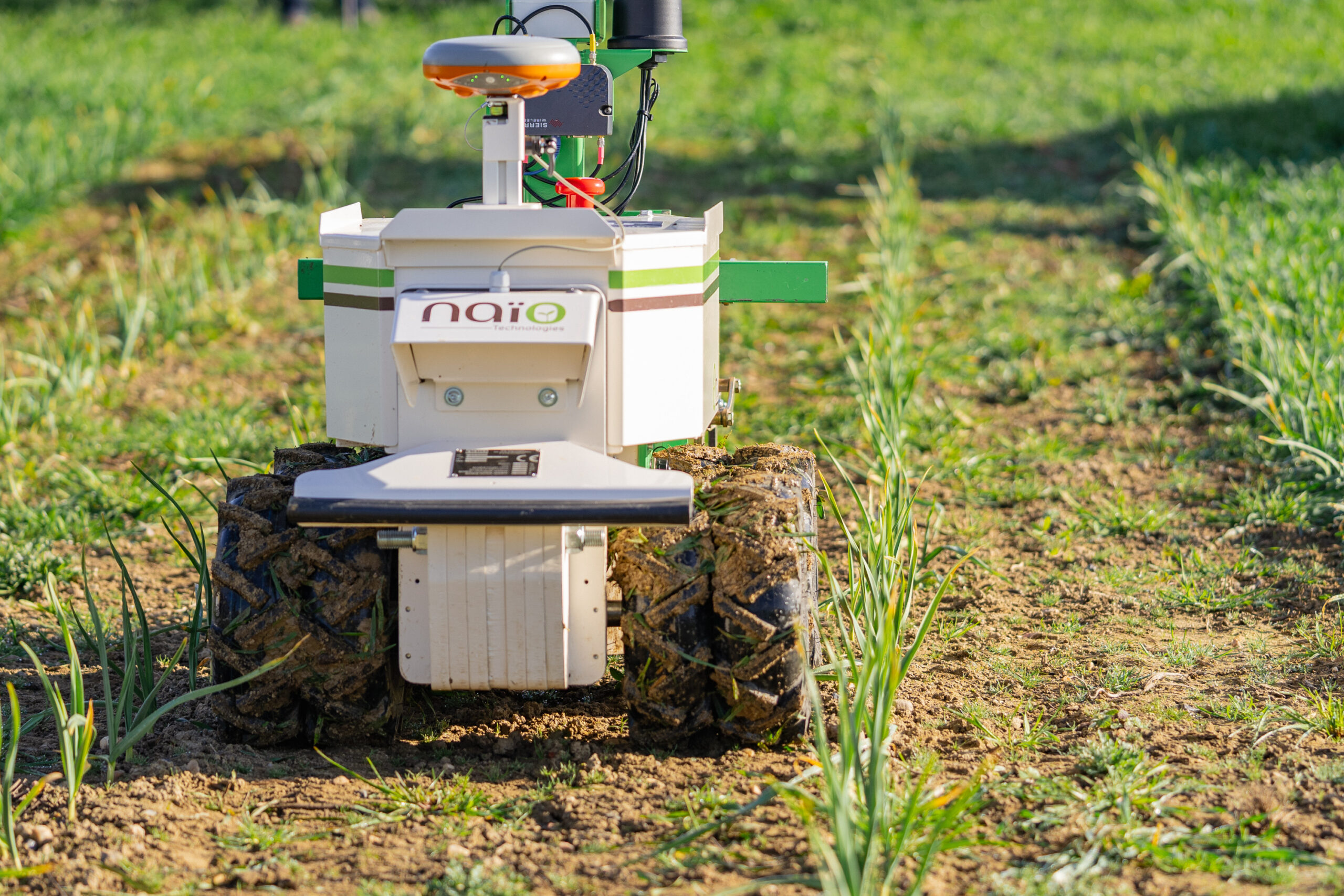
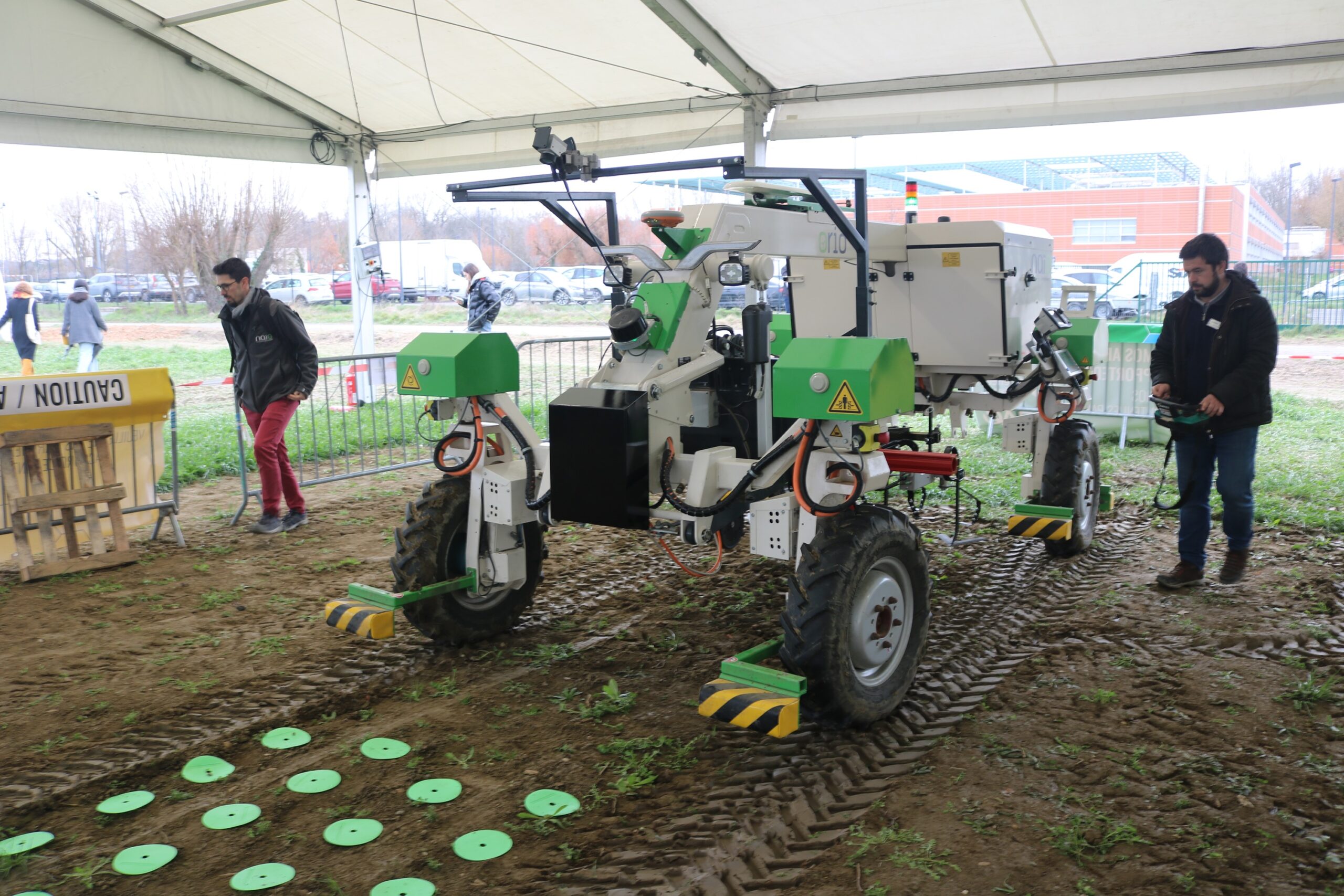
The one to watch is Naïo Orio. Launched in 2022, it’s a seeding, weeding autonomous tool carrier. Orio is 100% electric with a 12kW battery kicking out a 20kW peak from a 21kWh battery pack (32kWh from the HD versions). There are two widths, with the Narrow spanning up to 2.15m and the Large reaching out to 2.38m.
Orio puts the tool carrier on a three-point Cat 2 linkage arm with a 700kg lift in the middle of its chassis, which spans a total length of 4.28m. There’s a range of compatible weeding and seeding tools, including the K.U.L.T. precision hoe, with an optional camera-guided sideshift to add auto-guidance to inter-row weeding. Sugar beet is the furthest into arable row crops you can take the Orio, with field vegetables, tree nurseries and speciality crops, including raised beds, where it’s most at home.
Augmented Agronomy is how Naïo gives its customers the confidence to leave the robots on their own in the field to do the job at hand. Naïo technicians help you create the geofencing maps and teach you how to launch autonomous modes. This complies with CE certification with back-up LIDAR and bumpers in case an unexpected item turns up in Orio’s working area. It’ll then do its thing, on its own, traveling up to 5.5km/h for up to 10hrs on a full charge. Orio is priced at €200,000 (£171,000).
Joining Orio in the field was the Naïo Jo, a compact, tracked autonomous bot that can do mechanical weeding on the row and inter-row, seeding, mowing, furrow tracing and carrying. Just 1m wide, it’s ideal for narrow and hilly vineyards, and also has potential in speciality crops and orchards, running at a maximum speed of 2.2km/h for up to 12hrs on a full charge. “Jo was designed with the Comité Champagne as a machine to manage the narrow vines and really sharp U-turn bends in Champagne vines,” notes Naïo marketing manager Flavien Roussel. It’s priced at €100,000 (£86,000).
Also running in the field was the Naïo Ted, a specialist tool for vineyards that straddles the vine for mechanical weeding and cultivation. A 12kW drivetrain keeps it going for up to eight hours and will set you back €200,000 (£171,000). Then there’s Oz, where it all started for Naïo, with over 300 units now sold. Weighing just 180kg, Oz has a tool carrier that can lift 60kg. It can seed, plant and mechanical weed for up to eight hours on a full battery charge, autonomously working off waypoints with obstacles detected through a pressure-sensitive sensor on the front. It’s priced at €40,000 (£34,000).
“Oz came about from demand by asparagus growers to reduce the labour burden. It’s a tool for smallholders and nurseries with around 2.5ha. The first prototype attracted huge interest, and that’s what got us started,” recalls Flavien. Crowd-funding and a cash injection from the French BPI bank sped the start-up on its way, and it successfully raised a €32M round led by Mirova in November 2022.
The only notable Brit creation at FIRA was Crover. The grain-management tool has lost its curious rattle shape and no longer burrows into the heap. Now it’s a bot that sits on the top of the grain, crawling along on two Archimedes screws with a probe, currently 1.5m long, although a deeper one is in development.
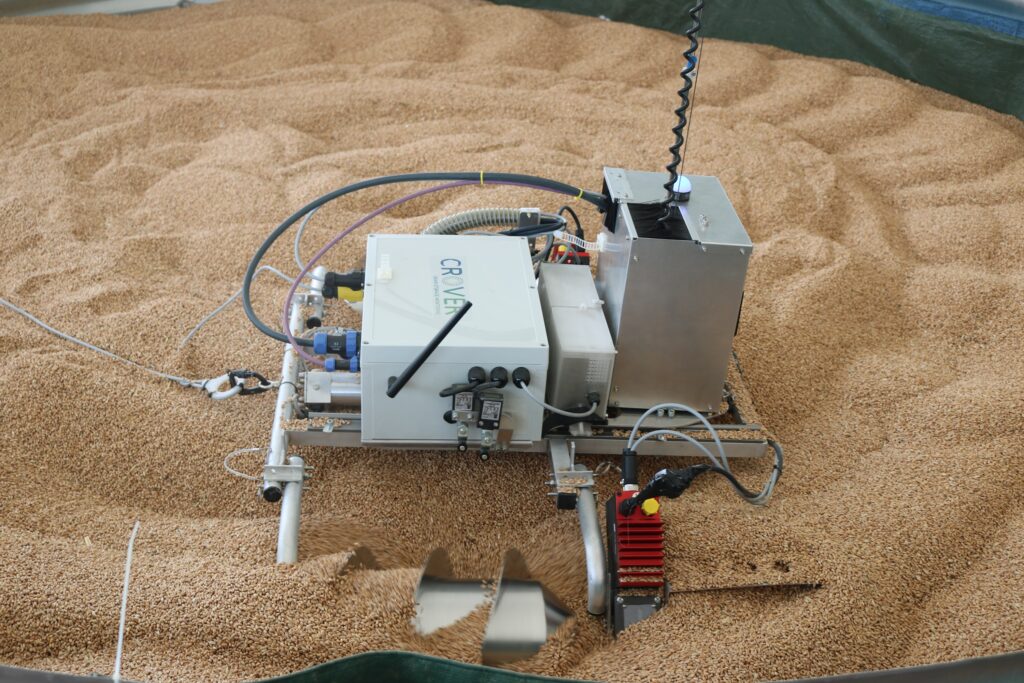
“There were a number of challenges with the burrowing Crover,” explains the company’s Gianlorenzo de Santis. “Navigating accurately was one of them and there was a lot of friction and drag.”
The prototype is expected to be market-ready by the end of the year, and will be available to rent at £5000/yr or buy with its full web platform at £15,000.
The Robot One from Pixelfarming Robotics in the Netherlands drew a crowd. Fully electric, there’s a 13.5kWh battery on board while three large solar panels keep it powered up. Robot One is a weeding tool, working on the principle of “Scan & Act”. It uses 14 high-resolution depth-sensing cameras to create a 3D depth map of the field.
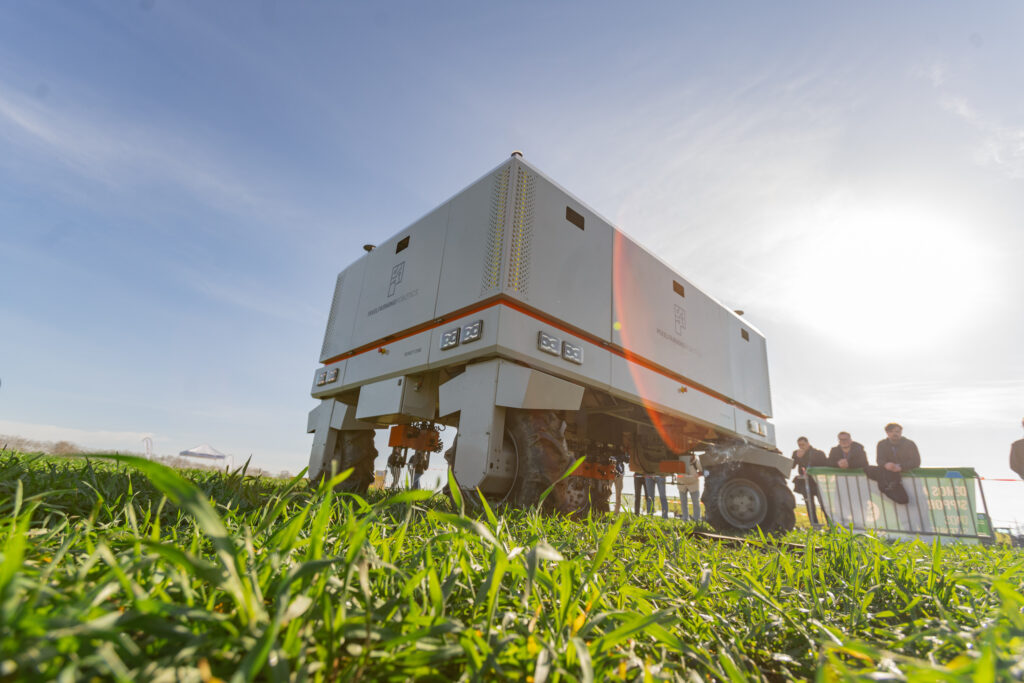
This is when it then gets interesting. The unit can be trained to detect specific weeds that are then targeted for treatment using tools mounted on up to 10 controllable arms that are independently adjustable in row. There are hoes that can be substituted for a streamer, rotor harrow or L-Bow, boasting 2mm accuracy along its 3.5m working width (5m for the Robot One L).
New to the Robot One is laser-weeding with up to 40 130W lasers capable of zapping up to 400,000 weeds per hour. Targeted at the organic and regen market and capable of working relatively large-scale, the Robot One is priced at €249,000 (£213,000).
Odd.Bot chose FIRA to unveil its new Weader that can be mounted onto any self-driving carrier. Twinned with weed-detection software, Weader can identify and precisely remove weeds within the crop rows, even in high-density plantings, without harming the intended crops. With a pull or a push, depending on the size and type of weed, each arm can remove up to two weeds per second.
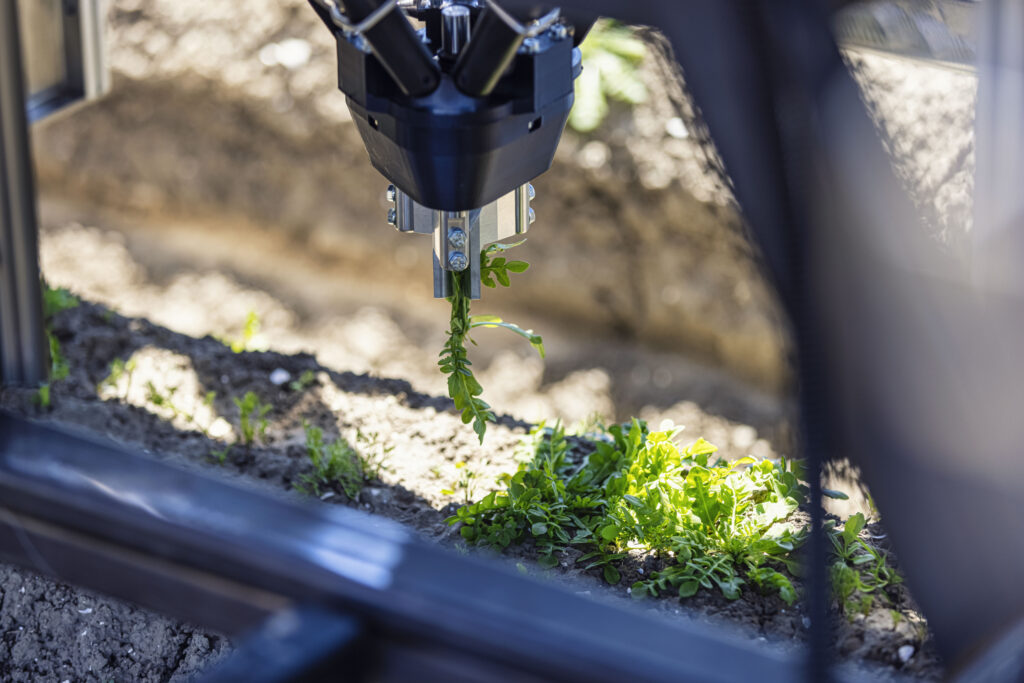
Aimed at organic field vegetable growers, The Weader was developed in the Netherlands through a collaborative initiative with farmers participating in the Odd.Bot Trailblazer Program and Wageningen University.
German autonomous implement manufacturer K.U.L.T. Kress presented its new aiLaser at FIRA. The laser technology can control weeds in the immediate vicinity of the crop without affecting the soil structure from as early as the cotyledon stage. Optical sensors continuously capture images of the crop, with weeds identified through AI, which are denatured in a targeted way by the heat of the laser.
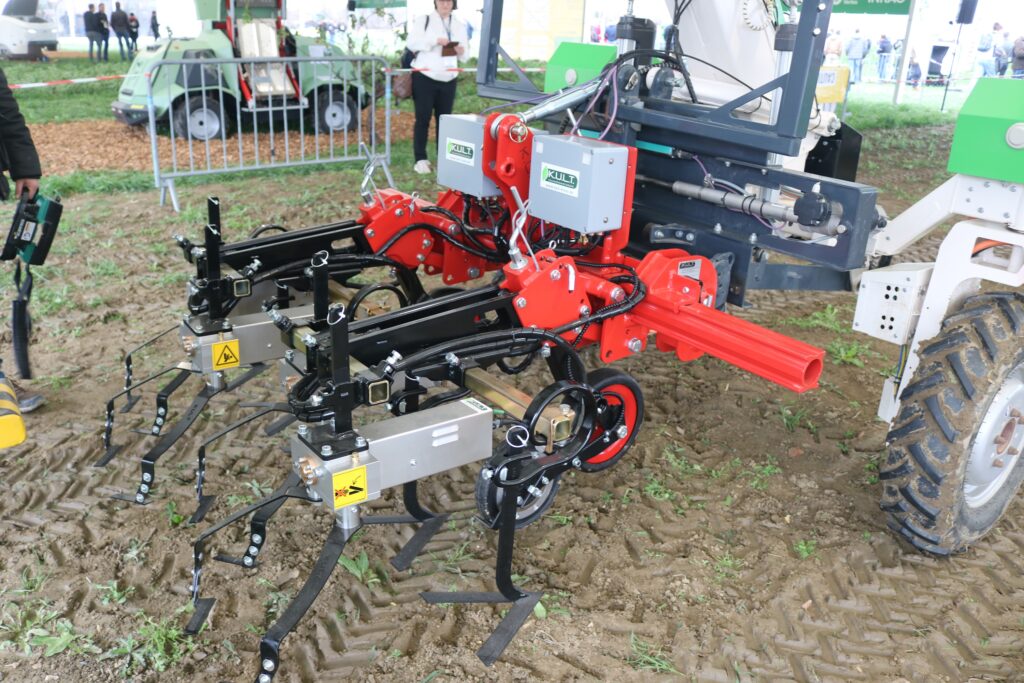
The K.U.L.T. iScan module can also be used to control in-row weeds mechanically. The plant-recognition system analyses images to detect the precise location of crop plants. The InRow eActuators then work in between plants within the row to hoe the soil as close to the crop as possible.
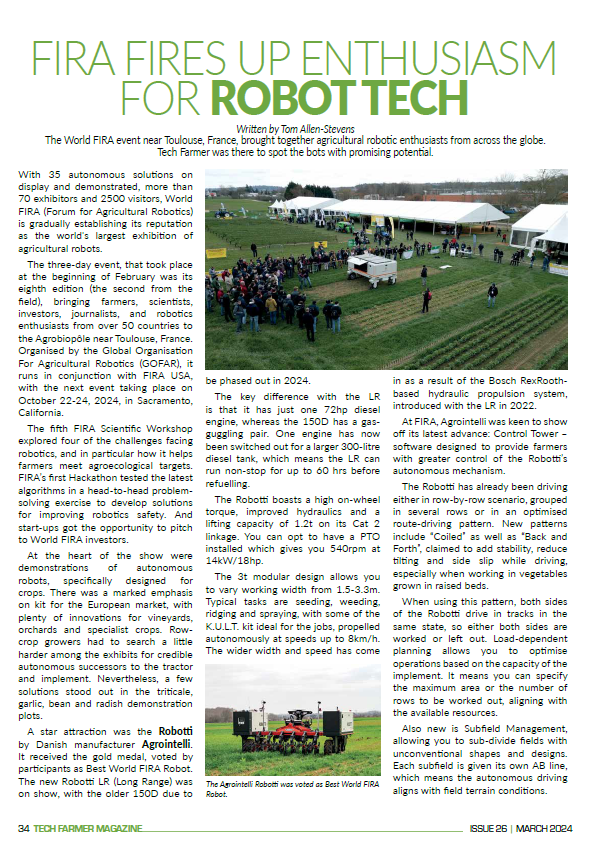
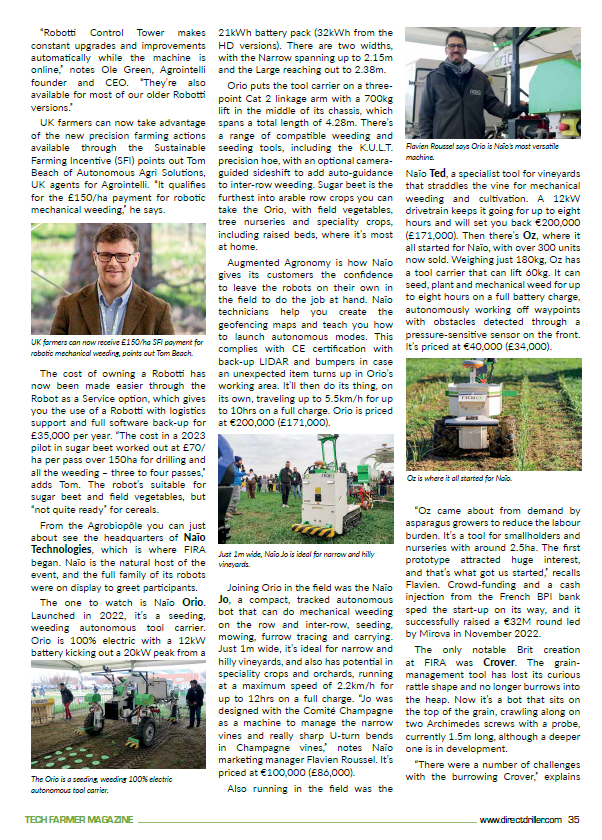
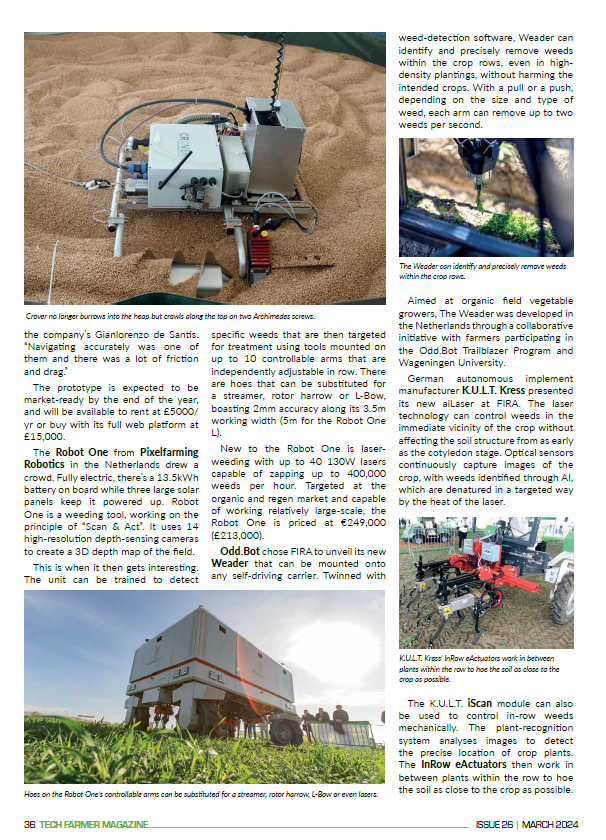
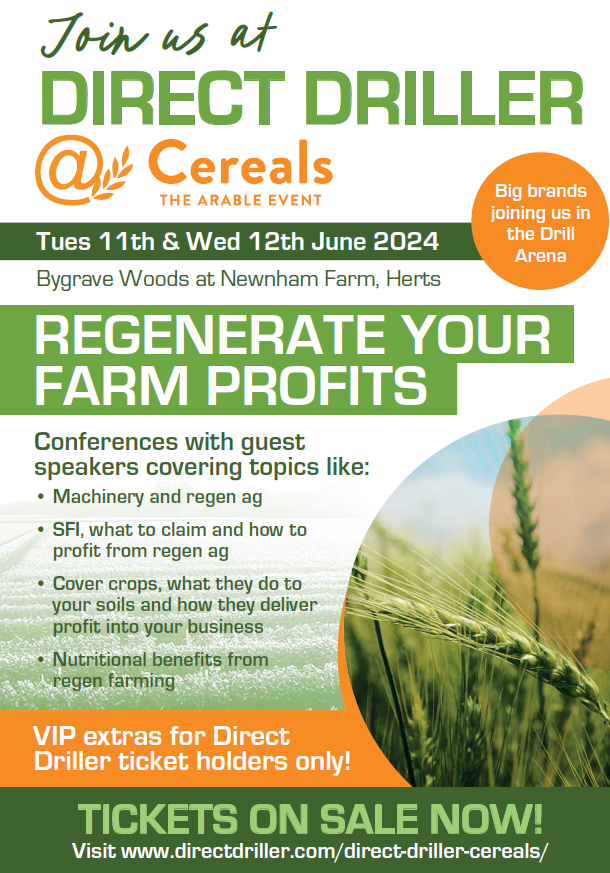