Back in issue one of direct driller Mike Donovan of Practical Farm Ideas wrote about our budget no-till drill in his article “How to start drilling for 8k”. The drill had been bought and modified at the time to run along our John Deere 750a, partly to increase capacity to cope with a seemingly ever expanding workload in constantly tightening weather windows and also to provide a low disturbance tine option, complementing the disc coulter of the John Deere machine,
by Clive Bailye – twitter.com/TWBFarms
The question of tine vs disc on notill drills has been frequently debated amongst farmers. The disc can cope with extraordinary amounts of trash that would turn a tined drill into little more than a rake yet it some situations the disc can push straw residue into the slot, a process commonly referred to as “hair pinning” with undesirable agronomic consequences for the plant, whilst the tine avoids this by sweeping the seed zone clear of trash.
Coulter designs like the Cross Slot and Novag drills combine the trash handling ability of a disc drill with the slot clearing characteristics of a tine equipped machine but come at a cost both financially and in terms of power requirement, for the direct driller looking for a single drill this design of coulter possible best provides that solution.
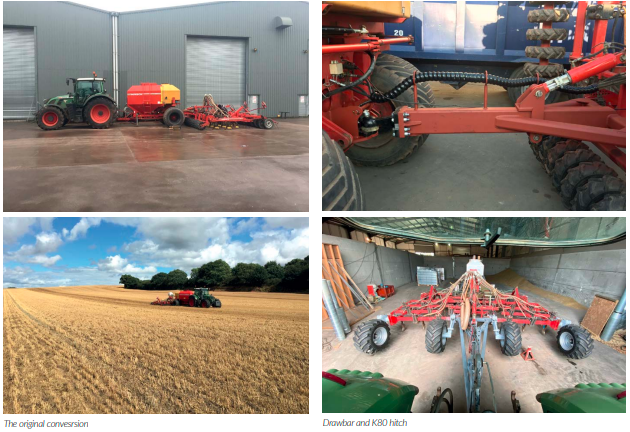
Some disc drills are fitted with row cleaners that clear the trash ahead of the coulter, as our farmed area grew and we needed to use both the 750a and converted C06 in situations with hair pinning potential we did ultimately end up with a set of Aricks row cleaners imported from Australia fitted to our 750a, which although a good solution, not a cheap option or always one available to UK farms. The initial modifications carried out to the CO6 are covered back in issue 1 but other than a good service, fitting a 2nd small seed / slug pellet / avadex applicator and conversion to a low disturbance point it was still mostly as it had left the Horsch factory. Since then we have covered many acres with this machine and the modifications have evolved to become what I now think it’s the perfect tine drill solution.
Drawbar
We opted to buy a European spec Co as the seed carts ran a far superior single floatation tyre than the small double castored wheel more commonly specified in the UK. As well as the obvious ground pressure advantage this design was much more stable on the road, the drawback however was a lack of machine following on the road making traffic islands and access to tighter gateways off narrow lanes somewhat of a challenge. The solution was to add an articulation between seed cart and toolbar creating a drawbar with K80 style ball hitch, doing this also created the ability to disconnect the toolbar from the seed cart completely if required and use it in the front hoper configuration described later in this article.
Conversion points
The drill was originally converted to low disturbance using Metcalfe points, these 12mm points provided a very low disturbance solution, however on our higher stone content soils they often lost the tungsten tip leading to premature wear, the seed tube was too narrow to flow large seed like peas and beans without blockage so needed upgrade to their larger tube diameter which was prone to rapid wear. To try and address these issues we set about making our own version, slightly wider at 15mm and using Ferobide wear tiles rather than the tungsten of the Metcalfe, the logic being that the Ferobide could be replaced if it broke off using farm workshop Mig welder rather than specialist induction welding that is required to reattached tungsten. We also added a slide plate to these farm designed points to protect the seed tube all of which gave a significant improvement to reliability and wear but at the cost of much more soil disturbance.
The other commonly used conversions for these drills are the Dutch Industries coulter and the Bourgault VOS (Versatile opener system) both offer a similar cast point with seed (and in some versions fertiliser) delivery run internally through the casting. Having run a test of both brands the Boulgault seem the better option, no only did it seem to wear better on our soil types but it offered more options for both solid and liquid fertiliser placement and a range of seed banding widths.
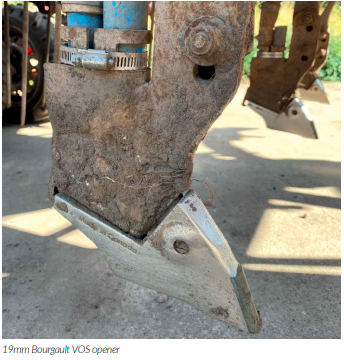
Possibilities with this coulter seem endless and open opportunity for companion cropping, seed and fertiliser banding and biological liquid placement separately or in the same slots. We started off using the 75mm twin band point which was very successful but in the terrible wet conditions and late drilling of autumn 2019 we moved to the single row 19mm point. I doubt we would have had half the area planted if we hadn’t used it. This point seems to be the sweet spot for us and I like the 250mm row widths which are the same as our Avatar disc drill. For farms with more challenging grassweed issues than we have I can see the wider twin row versions of this point would be a excellent solution. As well as the performance the wear rates seem low so I do not think we will look any further in the future than the VOS opener.
Packers
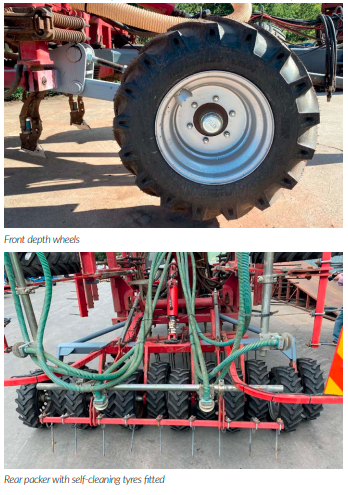
Our CO6 had clearly been loved by its previous Polish owner who had made several upgrades. Not only had they converted the rear packer to the later, more reliable sprinter style bearings but they had fitted a front packer to the toolbar. Such a front packer would have been ideal when the drill was used on cultivated land providing some consolidation ahead of the seeding. But in a none disturbed no tillage situation it was somewhat redundant. However when the drawbar conversion was done it served a new role in providing depth control at the front of the machine so was retained.
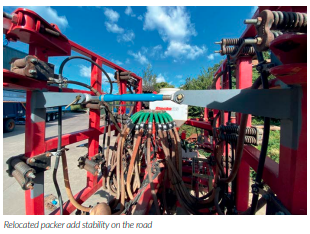
The tyres were a small diameter which in wet conditions could struggle to keep turning, they were also quite worn, punctures and a few tyres with damaged sidewalls ultimately made it more economic to replace its depth control role with 4 larger diameter wheels, we used the same size wheel and tyre as fitted to our 12.25 Horsch Avatar giving us a universal fitting spare.
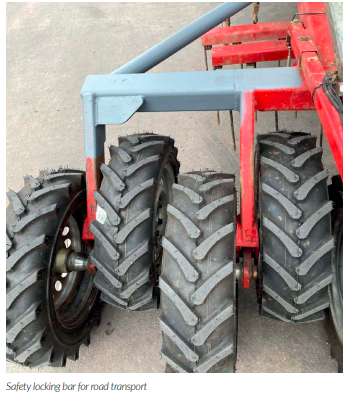
The rear packer ran the standard CO car pattern tyres that were again getting quite worn and were less than ideal in wet conditions so these have now also been replaced with a similar size BTK tyre with a self-cleaning tread pattern again helping with wet condition performance.
Safety and stability
With the addition of the drawbar the stability of the machine when folded was reduced, the high centre of gravity less anchored by a fixed linkage. The solution was to remove the first packer axle from each of the vertical wings and reattach it to the centre section, giving a wider, more stable wheelbase but still within the 2.95m road legal transport widths. Another small addition has been the addition of a fixed top link locking bar to hold everything securely on the road and not rely on hydraulics or straps.
Front Hopper
The move to having drawbar connection between seed cart and toolbar offered the possibilities of running the drill with a front hopper rather than the large seed cart. This offered the advantage of a much-simplified machine with far better visibility of the toolbar for the operator along with enhanced weight distribution and 2 less tyres on the ground. This created a drill that’s wet weather performance is truly exceptional and was able to complete 100% of our 2019/2020 workload through record wet conditions. The combination of undisturbed soil, optimal weight distribution over as few weight carrying tyres as possible and the low disturbance coulter allowing the rear packer to run clean without soil contact. All worked together to establish crops successfully through a very difficult season.
The hopper we chose was the Horsch Partner, this fully ISO hopper uses the same control software as our Avatar and incorporates the same blockage monitoring system so is familiar to operators. Like the Avatar it’s a very simple one man operation to calibrate and has metering and fan capacity to cope with a 12 m toolbar giving us options to use it with the Avatar (giving ability to drill up to 6 products, meaning less pre missing of cover crops ) or with other 12m wide seeders in the future fitting in with the 12/36m control traffic farming system we operate. The hopper can be split into 2 products giving seed / fert or companion cropping options which with the versatility of the Boulgault openers creates a new word of possibilities!
Costs and Conclusions
Of course, over the years of development the cost has now moved on from the original £8000 spent buying and converting the drill, approximately an additional £6000 was spend on drawbar, opener, and packer conversion. The seed cart has been sold offsetting some of the cost of the front hopper the cost of which can be anything from £1000 for a well-used Accord unit at a farm sale to £20,000 plus for a fully specified ISO 2 product unit with blockage monitors
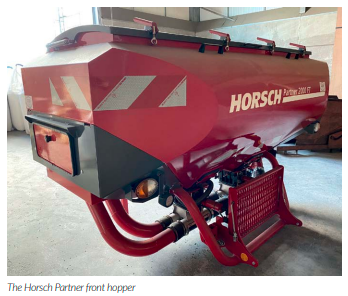
It’s taken us 4 seasons to fully develop this machine to where it is today, even after the additional spend it offers a relatively cheap and versatile no till tine drill that agronomically complements our Avatar disc drill, gives us additional capacity and offers a degree of insurance against wet conditions. It shows you don’t always need to spend huge amount on a new machine to direct drill. All it needs now (this winter’s project) is a sandblasting and a coat of shiny paint to smarten up all than “development mule” primer !
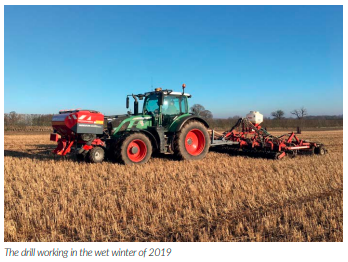
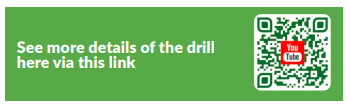