
If you are serious about reducing soil movement to reduce costs in fuel and labour without reducing yield through compaction what are your options, and how do you ‘dip your toe’ without financial commitment? “Just looking thanks” is the phrase while on a manufactures show stand whilst trying to form your own opinion. How do you do a bit of non-bias research on system change on your farm? AHDB’s Monitor Farm meetings are one way, either on-line or in the future back to face to face meetings. But again how do you build a system for your farm, based on your soil type, your area to be covered and time available to you?
To gain an idea of the size and width of a direct drill whatever design you choose you can look up the AHDB Machinery Calculator and mess with the width, forward speed and field efficiency (time spent actually drilling rather than turning and filling) and come up with a drill width to suit you. If the numbers don’t stack up, up the speed or more hours per day, eventually you will come up with a consensus of what you need.
But as the power needed increases so does the weight of tractor need to pull the drill. Can you assess the level of compaction going in below where your chosen drill is working? Based on the weight on the tyres, soil type and soil moisture, yes you can.
Terranimo is a website where you can select the tractor/implement combination or crop sprayer, combine harvester, beet harvester, Potato harvester, forage harvester for that matter. Select the tyres, calculate the weight on each tyre, select the soil type and soil moisture and calculate the depth of compaction based on the data you have entered. Hey presto you can generate a detailed report on your chosen set up. And, like the machinery calculator, if you don’t like what you see, change the numbers and try again. Nothing ventured and all that.
For the lucky living in Scotland the soils data is already entered, just pick your county and the soil data at 10cm steps to 150cm depth is available. Choose between dry, moist, and wet for your soil water content and choose if you plough and cultivator or not. For those not living in Scotland work is on going to bring England into the fold, but for now your soil type can be entered manually.
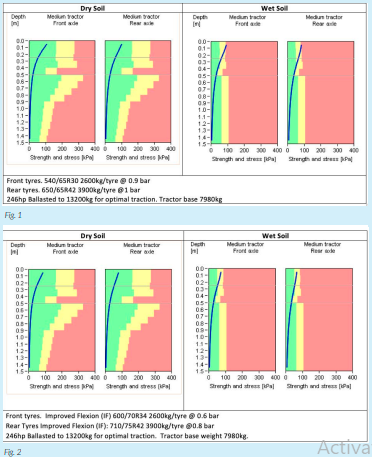
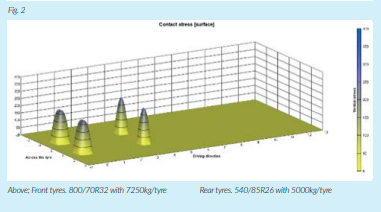
Of course, those reading these pages will be keen to remind of increased soil organic matter and higher magnesium content in clay soils would help too. But for now, lets keep it simple.
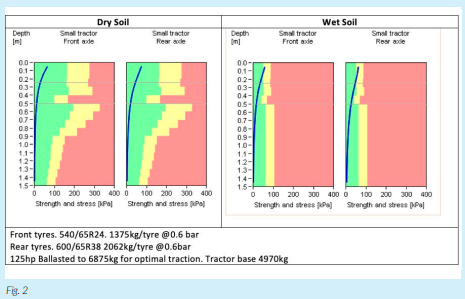
In choosing tyres there are over 800 tyre sizes, brands and designs to go at. Twin track and four track tractors are in there too. But I’m not pretending every brand and combination is achievable and the very latest tyre on the market may not be present. The website is the work of Aarhus University in Demark and the AHDB have been funding its availability in the UK.
So, looking at a typical 246hp drill tractor (Fig.1), if it is ballasted to achieve full traction then the graphs below represent the soils ability to carry the weight of the tractor on the tyres selected. The blue line represents the tractors front and rear axles and the boundary between green and yellow corresponds to 75% of the calculated soil strength, and the boundary between yellow and red shows 125% the soil strength. In the wet soil condition graph both front and rear axles reach 125% to a depth of 10cm and compaction is still ‘going in’ at 50cm. In the dry condition graph, the soil is able to support the tractor without undue compaction.
If the same tractor is fitted with wider IF (Increased Flexion) tyres, (Fig.2), then things improve. But it must be stressed that the tractor is fully ballasted for full traction, so its unlikely in the real world to need this level of ballast for drilling.
Looking at a 125hp tractor fitted with the optional wider tyres (Fig. 3) shows similar characteristics to the 246hp tractor on IF tyres and of course this is fully ballasted, worst case scenario. Removing the ballast, sheds almost 30% off the tractors weight.
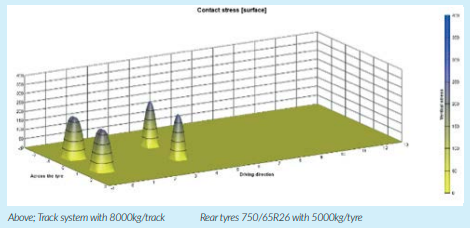
Choosing whether to go with tracks or a wheeled machine for your next combine? The Contact Stress function can point out the peak pressures from wheeled or tracked combines. Below is a typical large wheeled combine with 9-metre header fitted. With both grain tank and fuel tank full the front axle comes to 14500kg with 10000kg on the rear axle. Note the rear axle in this case is exerting more stress on the soil the front axle.
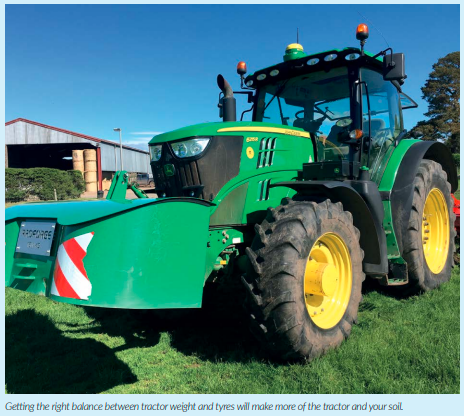
The same combine with the track option fitted show a marked improvement in soil stress, the front and rear rollers with two centre idlers exerting the peak pressures. This combine is also fitted with much larger rear tyres but still exert more stress than the track unit. Both combine calculations here used Dry Soil. But of course, this is not always available. Just as an illustration we have sent our fully leaden wheeled combine into wet, clay soil conditions. As you can see below the front axle did not find soil able to support its weight until at 50cm depth and the rear axle is little better. Yes, the combine is stuck. And if this where real, que the social media fest.

Obviously, the examples I have shown here, while real, are not likely to be what you need. So, get the kettle on, forget Strictly goes Dancing and have a go at calculating the right tyres, power, indeed farming system for your future.
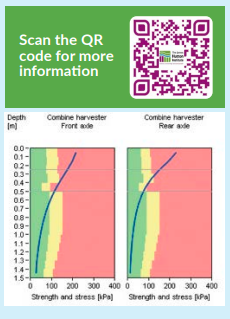