After successfully completing the multi-year research project MARS (Mobile Agricultural Robot Swarms) in collaboration with the Ulm University of Applied Sciences and the EU research funding, AGCO and Fendt decided to develop the robot project up to series-production readiness for the Fendt brand.
The entire system, including small robots operating in swarms and a cloud-based system control will now be operated under the product name ‘XAVER’. ‘Xaver’ is a traditional Bavarian name with deep roots at Fendt. In the 1930s, the brothers Hermann and Xaver Fendt founded ‘Maschinen- und Schlepperfabrik Xaver Fendt & Co.’, named after their grandfather Xaver Fendt. Regarding the new robots the name ‘Xaver’ incorporates tradition and the latest agricultural technologies.
Fendt’s new Xaver system uses small robot units operating in swarms and a cloud solution to plan, monitor and accurately document the precise planting of corn. Satellite and data management in the cloud allows navigation around the clock operations, with permanent access to all data. The exact position and sowing time of each seed is accurately recorded. Knowing exactly where the seed has been planted opens up new potential for further processes, since subsequent operations such as crop protecting or fertilising, can be performed precisely at the individual plant. Planning for the required field, for seeds, seed patterns and -density is carried out via the Xaver app.
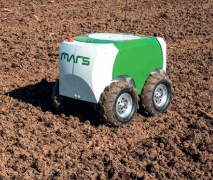
The intelligent OptiVisor algorithm plans the robot’s deployment based on the entered parameters, and calculates the optimal paths for the units involved and the time required for completion of the job. Software updates for the system can be downloaded “over the air”, just as a remote diagnostic can be run conveniently and locationindependt via the smart device.
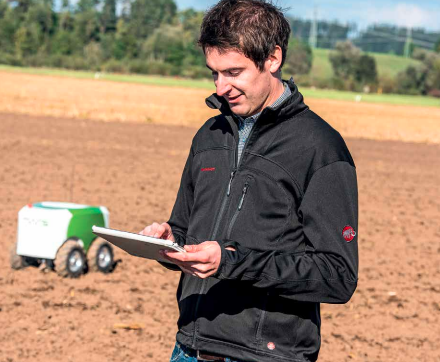
Intelligent fleet management
A key element of the Xaver project is the intelligent management of the deployed robots. For example, a Fendt robot system consists of 6–12 units, and can therefore attain an area coverage of around 1 ha/h. Each robot is in constant communication with the control intelligence. Data buffering and redundant communication help covering breaks in the network coverage. If a robot malfunctions, the paths of all units are automatically reoptimised, and the remaining robots take care of the work. Additionally, a mixed variety of crops can be planted in the field, since each robot can be filled with different seeds.
Resource efficiency and soil protection
Thanks to the battery-operated, electrical motor (approx. 400 W), the low weight (approx. 50 kg), and the autonomous operation, planting can continue round the clock, 7 days a week, even in conditions which conventional machines find difficult, e.g. due to the state of the ground or noise emissions. This increases the productivity and flexibility of the system. In relation to the large tyres, the ground pressure is almost negligible (approx. 200 g/cm²).
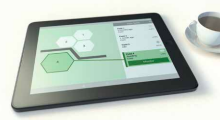
The robots need around 70% less energy to do the same work, and accordingly produce less CO2 when doing it. Since neither diesel nor oil is required to operate the robots, there is no leakage and there are no local emissions.
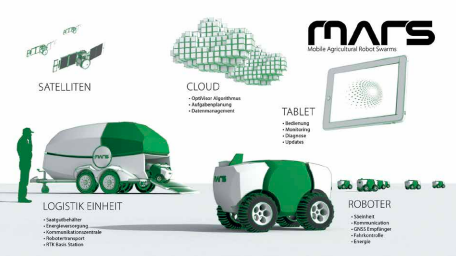
The robots are easy to mechanically assemble, do not use complex sensors, and are therefore highly robust. Their small size and light weight make maintenance easier, and means that the system is intrinsically safe.
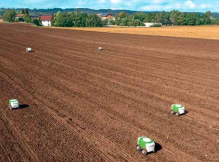
If you were at Agritechnica in 2017 then you will have seen the XAVER robots up close and the static demonstrations. For innovative farmers focusing on precision farming they are certainly of interest. Lets hope that more is unveiled at Agritechnica 2019 with regard to when we will actually see this technology on farm, but it certainly sounds interesting and not that far away.