HORSCH PRONTO NT EXPANDS SEED DRILL FAMILY
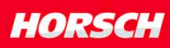
Available in 6m, 8m and 9m working widths, the Horsch Pronto NT features the well-proven TurboDisc doubledisc coulter at 20cm row spacing in combination with a compact, leading wavy disc, making it ideal for low disturbance drilling and direct seeding. Operational speeds up to 20kph allow for a high area output even at smaller working widths. Horsepower requirement is very low as the wavy discs cut through organic material and cultivate the soil only in the seed rows, creating a fine earth in the seed horizon.
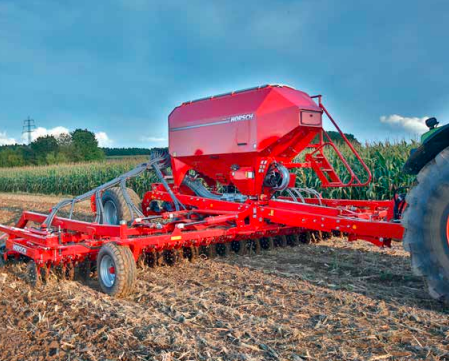
The necessary weight for operation of the wavy discs and seed coulters is transferred via the sophisticated hydraulic system of the machine. In very hard conditions, additional weight up to 1400 kg can be mounted on the frame. A large 4,000-litre seed hopper guarantees low idle times while a 5,000-litre double hopper allows seed and fertiliser to be applied at the same time. A micro-granular unit can be combined with double hopper as well as with the single hopper version allowing seed, fertiliser and microgranular compounds to be metered in only one pass.
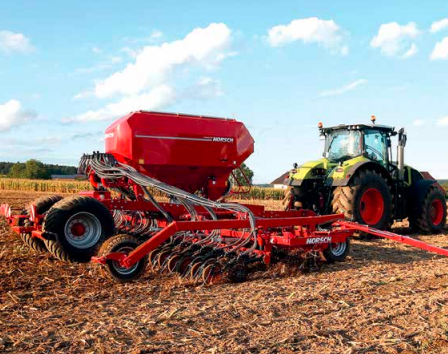
A PERFECT YEAR FOR EFFECTIVE STUBBLE MANAGEMENT
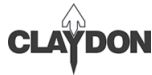
Stubble management is an essential part of any efficient, sustainable, profitable crop production system and conditions this season have been perfect to maximise the benefits. Jeff Claydon, who farms in Suffolk and designed the Claydon OptiTill® System, explains why.
Stubble management is an essential part of any efficient, sustainable, profitable crop production system and conditions this season have been perfect to maximise the benefits. Jeff Claydon, who farms in Suffolk and designed the Claydon Opti-Till® System, explains why. I guess that many who enter the world of no-till crop establishment think that all you need to do with such a system is to spray the stubbles with glyphosate and then direct seed. In a utopian world where Mother Nature is always kind, the farm is very clean and slug free you might be able to get away with that, but it’s not like that for most of us.
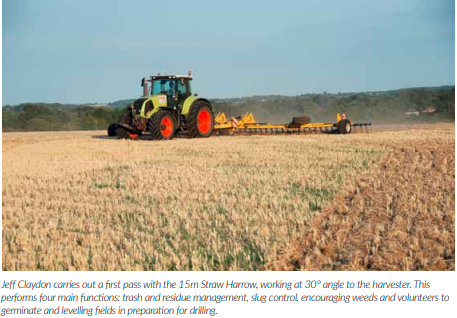
Back in 2002 when we were in the early stages of developing what is now the Claydon Opti-Till System we used to think that way too. Sometimes that approach produced fantastic crops, but others would be poor or even an outright disaster, so we spent many years trying countless different ideas, techniques and equipment to overcome this variability and achieve consistently good results. Initially, we genuinely thought that if we did not disturb the soil surface the weed seeds would degenerate, the chemical we applied would be closer to them and more effective, so our weed problems would quickly vanish. As it turned out we had more problems and to overcome them increased our use of expensive chemicals, thereby negating some of the savings in establishment costs that we were making. After years of continuous research, we have subsequently developed the knowledge and machinery to achieve the very best results, in all crops, soils and conditions.
Every season is different and the conditions it presents require careful assessment, regardless of which system you use, so we have learned to address the challenges that Mother Nature sets us. The last two years, for example, have provided perfectly contrasting conditions. In 2017 when we were harvesting in August the soil was wet and gummy, but this year it was dry and crumbly with plenty of natural cracking which went down much deeper than any subsoiler. When we finished harvest in July the soil was bone dry. As I write, on 28 August, over 80mm of rain has fallen in the month since harvest and we are seeing real benefits in terms of managing stubbles, which is a critical because otherwise slugs can pose a major risk. The adults rise to the surface, lay thousands of eggs under crop residue and quickly populate the area, making it hard to establish the following crop.
Where the combine stops there is a tendency to leave ‘Skylark’ patches due to the extra straw left in that area and the following crop growing on them will lack vigour, allowing weeds to develop while any seed in the straw, and sometimes on the surface, will lay dormant only to reappear in the next crop. We overcame those issues, and others, by developing the Claydon Straw Harrow.
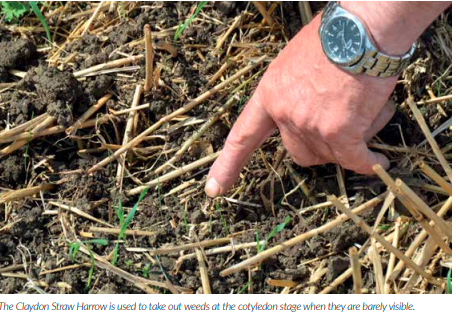
In 2007 we tried using a straw harrow on the Claydon farms, but quickly dismissed it because it appeared to do very little. How wrong we were, because where it had been used the crops were much better and more even, with far fewer slug and weed issues. After that, we further developed the straw harrow into the implement it is today, getting the weight and balance exactly right to achieve the best results. Within a week of finishing harvest this year we ran our 15m straw harrow across the entire farm (see it in action on www.claydondrill.com/videogallery). Operating at 18kph, at an angle to the combine, the 15m straw harrow covers 25 hectares an hour and, using less than 2.5 litres of diesel per hectare, distributes the chopped straw while creating a fine, level, 2cm-deep tilth which encourages volunteers and weeds to grow. The key is to follow quickly behind the harvester before the soil bakes hard, because creating this fine tilth on the surface will halt the capillary action in the soil, preventing it from drying and baking out.
Two weeks later, on 15 August, we had liberated countless one-leaf volunteers and the first flush of weed seeds had germinated. We then went over all our 400-hectare farm with the straw harrow to remove them. Everything wants to grow in a healthy soil and after just a few days we had another flush, so on 25 August the straw harrow was used again to remove them, with the benefit of destroying any slugs that had emerged in the meantime.
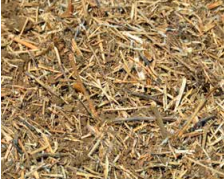
In the days and weeks before drilling we will have the opportunity to take out additional flushes. The weather is currently ideal and with each shower more germinate. Ideally, we will stop straw harrowing two weeks before drilling and will apply full-strength glyphosate to clean up any remaining weeds before winter wheats are established quickly and efficiently with the unique Claydon Opti-Till® drill. We use the straw harrow only when necessary, after we have assessed weed and pest issues. A pass of the harrow is fast, uses very little fuel and has a very low wearing parts requirement. Compared to a single pass of a deep cultivator, it is very inexpensive, and the cost is minimal in the overall scheme of things.
Our 15m Straw Harrow operates at 18kph and covers 25 hectares per hour, 400 hectares in 15 hours, which is the same output as our 24m sprayer. We use around 2.5 litres of fuel per hectare, so each time we straw harrow the farm we use around 900 litres. With red diesel at around 60p per litre it costs £540 to complete one pass with the Straw Harrow. With glyphosate costing around £3 per litre and applied at three litres per hectare the cost of chemical alone would be £3240, added to which you would still require nearly as much fuel to power the sprayer as to operate the Straw Harrow.
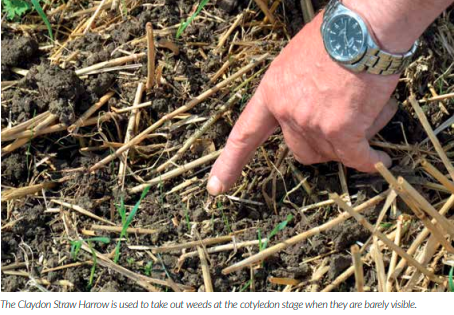
That means we can cover the farm four times with the Straw Harrow for roughly the same cost as one application of glyphosate, which is considerably cheaper than any other single cultivation pass using traditional cultivation equipment. Having farmed in the days before glyphosate I would not wish to return to that situation, so we must do all we can to preserve this valuable chemistry. When, finally, we do apply glyphosate it is as a single, fullstrength dose prior to drilling, which maximises its effectiveness and reduces the risk of resistance developing.
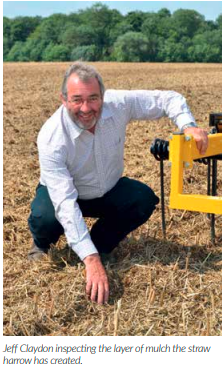
The Claydon Opti-Till system has been continuously developed over the last 16 years to enable crops to be established much more cost effectively and efficiently with reduced pressures from slugs and weeds. It also allows us to produce consistent highyielding crops. Our long-term average wheat yield is 10t/ha, but even with just 23mm of rain falling between 1 May and harvest this year yields were just 10% below that at harvest. Grain quality was excellent, achieved the top specification and with 13.8% protein, 350 Hagberg and a specific weight of 78h/l at 12% moisture it sold at £192 per tonne. I am sure that many farmers would be happy with that, whatever system they operate. To learn more about the Claydon OptiTill System and techniques to improve your farm’s performance contact your local Claydon dealer and arrange to visit our farm. You have nothing to lose and everything to gain.