Report by Chris Fellows, Direct Driller Magazine
Recognising an interest in reducing soil movement, AHDB has picked a new Monitor Farm that predominately uses a system of reduced tillage. The 4th July was the first event held at Rick Davies’ Newton Lodge Farm. It was a great chance for us to get to know Rick and understand how he farms at the moment and how he wants to move forward and change to meet the challenges of the future. The evening started with a brief introduction by Harry Henderson from AHDB. Held in one of Rick’s barns, Harry talked about why they had chosen this new Monitor Farm and why AHDB felt a Monitor Farm with a keen focus on cost control provides an interesting platform for local discussion.
Giving the growing relevance of direct drilling and soil health in the UK and the fact that Defra and Michel Gove himself are keen to promote (and maybe even push) the benefits of no-till practices then it’s interesting that this Monitor Farm joins a long line of Monitor Farms that have abandoned the plough. Therefore, the level of direct drilling representation at a Monitor Farm level is growing all they time just as overall interest in the practice grows.
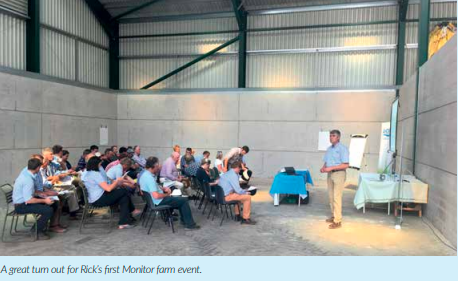
The important thing Harry stressed is that a Monitor Farm isn’t a demonstration farm, it is chosen as an example of a typical commercial farming business.

Harry also introduced AHDB’s Farmbench. Farmers can use Farmbench to better understand their cost of production. It allows them to compare their farm figures and performance against other growers in the local area and region. It is a confidential system that allows farmers to anonymously share information and by being able to talk to each other at meetings, learn from each other to find out where different systems can cut overheads. We will be discussing this topic of costings a lot in Direct Driller over the next few issues, as it is often so difficult to compare farms that are using conventional tillage to those using no-till and so often the benefits described have been anecdotal.
Harry presented a summary of Harvest 2017 Winter Wheat Group 4 figures, with a full economic cost of production per ton ranging from an average of £103.60 for the top 25% through to a average of £155.90 for the bottom 25%. The full breakdown of these figures is in Table 1.

Given the average sale price of Group 4 Wheats over the past 5 years, then some farms would be struggling to make a profit based on these figures. Harry then handed over to Rick, who talked about his farm. Rick is 4th generation and the family have been farming in Clifton Reynes since 1926. It’s predominantly an arable enterprise, with 404 ha farmed which is a mixture of owned and FBT. As with all farms, they have also diversified in several ways to help pay the bills. At Newton Farm they also have 14 office units, 4 industrial units, 52 Container Storage units and a Turf Sales and distribution business.
The big battle Rick is fighting is against black-grass. He even uses a plough (there we said it) as the “reset button”, should he think he has lost the battle in any given field. However even that doesn’t solve the problem, it just buries it and allows you to start afresh.
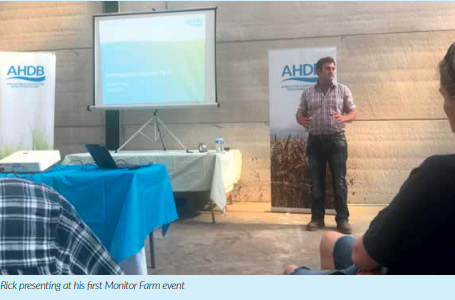
He’s using a different rotation in the fields that have a black-grass problem in conjunction with manual rogueing midseason. However, rogueing, comes a significant labour cost even though he does some of it himself. But it is one of the most effective ways to control black-grass. Rick told us that he is happy with the way he farms, but feels there are significant improvements that can be made to both the way he farms and to the profitability of his business. This was one of the main reasons he wanted to become a Monitor Farm. To open himself up to criticism and bring in ideas from other farmers. It’s a brave thing to do, when you know you aren’t perfect as there are always ways to improve and to put the way you farm on display for the world to see means everyone gets a “warts and all“ view. However, if you want to improve your business, then bringing in outside ideas is the best way to do it.
Rotations
In the fields that are black-grass free the rotation is: Winter Wheat, Winter Wheat, Spring Barley, OSR. In the fields with black-grass the rotation is: Wheat, Spring Barley, Spring Barley, OSR. These feel too tight for me and in the long term will struggle to be sustainable. I would expect that more beans and oats would need to be used in the future if Rick is to progress in his no-till development. He uses a Claydon 4.8 m drill for his drilling, rake and using a 12m Cambridge rolls to achieve a suitable seedbed.
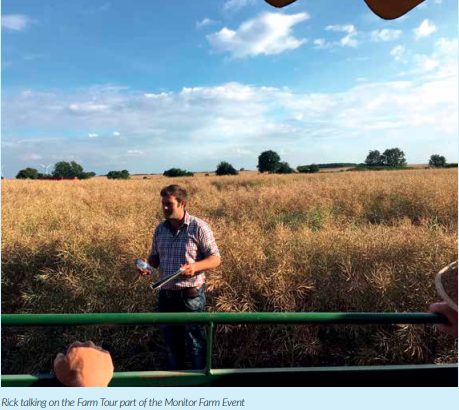
For first winter wheat he will Dyna-drive, then drill with the Claydon, rake and roll. For second Winter wheat, he drills with the Claydon, rakes and then ring rolls. For the Spring Barley, Rick will Dyna Drive in the autumn, then drill with the Claydon, rake and roll. Oil Seed Rape he just uses the Claydon and then ring rolls. Rick will also Flat-lift where required at OSR and second Winter Wheats. The thing that did surprise me was that Rick wasn’t using cover crops at all and he admitted it was an area where he didn’t have a lot of expertise. It would certainly help with organic matter levels and given he uses the Dyna-drive in the autumn anyway prior to Spring Barley then he could seed at the same time and not involve an additional pass.
Machinery
In terms of the machinery Rick is currently using on the Farm. They are as follows: 4.8m Claydon (2011). Then in no particular order he has: John Deere 7530 – 4250 (2008), John Deere 6620 – 6950 hours (2006), John Deere 6430 – 2100 hours (2012), Massey 3085 – 6900 Hours (1995), Case 1494 – 5700 hours (1984), Massey 7380 25ft – 1100 Hours (2013), Manitou 9m Telehandler – 7100 hours (1998), Amazone 24m Mounter 2800lt (2012), 3m Dynadrive (2015), low-disturbance flat-lift 2.4m (2018), Claydon 7.5m Rake (2012), 12m Twose Rolls (2000), 6 Furrow KV (1998), 8m Spring Tines (1995), 4m SKH Crumbler (1990), Rabe 4m Powerharrow (1985), KV 24m Spinner (2013), JCB 3CX – 5500 Hours (2002), 2 x Baileys 14T and a Warwick 16T.
Direct drilling is known to have a lower horsepower requirement. The 2006 John Deere has depreciated well. The reality is that this is still a lot of machinery for a no-till farm to have, but given the machine ages you could also say there in no harm in keeping them as they have very low depreciation.
Soil Pit
The first stop on the farm tour was the soil pit with Dr Jackie Stroud or Rothamsted and Ian Robertson of Sustainable Soil Management. The pit had been dug on the edge of a field adjacent to the river on part of the flood plain. As you would expect, even in the dry summer we had, the moisture levels were still good. The crops looked excellent at this location and Rick estimated that this part of the field would yield 12t plus per hectare. However, you could see a line in the field where the crops became drought stressed as the land raised up from the flood plain. So the field average was not going to be this high and he hoped it would yield just under 10 for the whole field. Rick explained that over the wet winter we had, although the land had flooded, it had not done so for extensive periods of time. Jackie explained the importance of worm activity in the soil and found some example for us to see and how reduced levels of tillage encouraged worm activity.
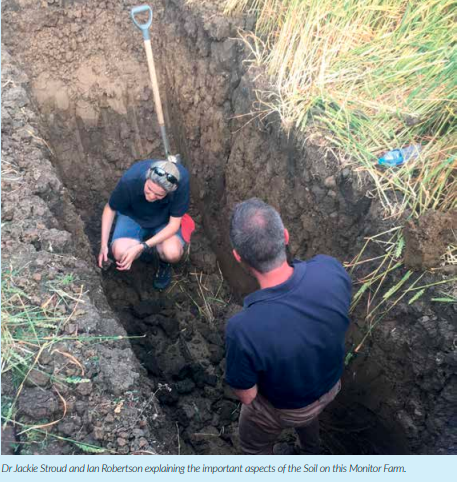
Ian went on to explain about root structure in reduced tillage situations and how the crops were able to better access moisture in the soils. These crops had roots going down 4ft into the soil and they were still green and growing well. With 6 weeks to go until harvest it is possible that the crops in this location never became drought stressed at all and will have excellent yield potential. Just one of the benefits of farming on a flood plain.
Farm Tour
Rick took us around a number of fields, given some fields were on a flood plain, there were vast differences in the crops. Drought stress had meant that some were really struggling. We stopped at some of the better OSR with Rick saying why he felt this field had done better than the fields by the entrance that we all drove past on the way in. By Rick’s own admission, he certainly isn’t proud of some of his crops this year, but given the weather conditions, it looked like he was still going to get good yields overall, but nothing ground breaking on average.
It will be good to get an update from Rick in the future on what his yields were and how much they were down on 2017. It has been theorised that no-till farms wheat will yield closer to average figures than conventional tillage farms in a year that has had limited rainfall. Hopefully we will have more data on this in the coming issues. This year Rick explained that he was growing 242 Ha of Milling Wheat (Crusoe, Skyfall, Gallant and Zyatt), 55 Ha of Oil Seed Rape (V316, Campus and Elgar), 64 Ha of Spring Barley (Explorer), 17Ha grass and 26 Ha of margins, mid-tier and tracks.
Cost of Establishment
Looking specifically at the cost of establishment, which for many is the key driver to a move to a reduced tillage system, Rick was able to share a number of figures. The figures themselves had come from Labour and Machinery reviews being conducted by Strutt & Parker across the Monitor Farms. What can be seen from these figures is that there is clearly room for Rick to reduce his cost of establishment further. On a no-till farm you could see fuel usage as low as 3-4 litres per hectare. And with this reduced fuel cost, comes reduced repair and labour costs.
Having said this, the review showed that Rick had one of the two lowest wheat operational costs, with the other lowest cost producer also direct drilling. However, in general, they said there wasn’t a significant correlation between establishment strategy and labour/ machinery costs. Some of the cheapest producers were still using the plough in the rotation. The reviews recognized that this is because these producers had lower labour, depreciation and repair costs, and therefore the type of cultivation or increased fuel usage made less of a difference.
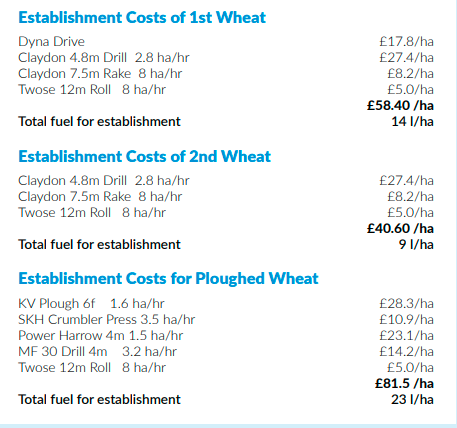
Taking into account all farms, when investigating a farm’s machinery costs. The labour and machinery reviews found that on average 26% was fuel, 35% was depreciation and 19% was repairs. Therefore, if a grower was adopting a mixed cultivation strategy and running well-maintained 2nd hand machines and implements it could still be as competitive as a direct drilling farm, despite the higher fuel costs. As always, it is so difficult to compare like for like in these situations, but it doesn’t seem that there was a lot of no-till farm data in the mix here.
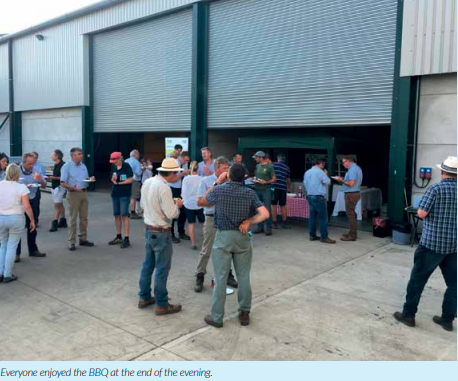
The Evening BBQ
The evening ended enjoying the summer whilst having a BBQ and chatting to the other farmers who had turned up from the local area to find out more at the Monitor Farm event. The number of farmers attending is a testament to the Monitor Farm programme and the part it plays in helping farmers learn from each other. My lasting impression was of Rick’s eagerness to keep learning and keep improving the way he farmed. He recognised that he still had his fair share of problems and having made the big leap to massively reduce the amount of ploughing, he now could make further changes to improve his profitability.
Future meeting dates at the Northampton Monitor Farm:
27th November 2018, 18th December 2018, 22nd January 2019 and 13th February 2019. For further information, please visit: cereals.ahdb.org.uk/Northampton or contact Harry Henderson on harry.henderson@ahdb.org.uk.